Feature Article
YAMAGATA CASIO×HIOS
“Consistently Adhere to Made in Japan”
Harmony of craftsmanship and digitization
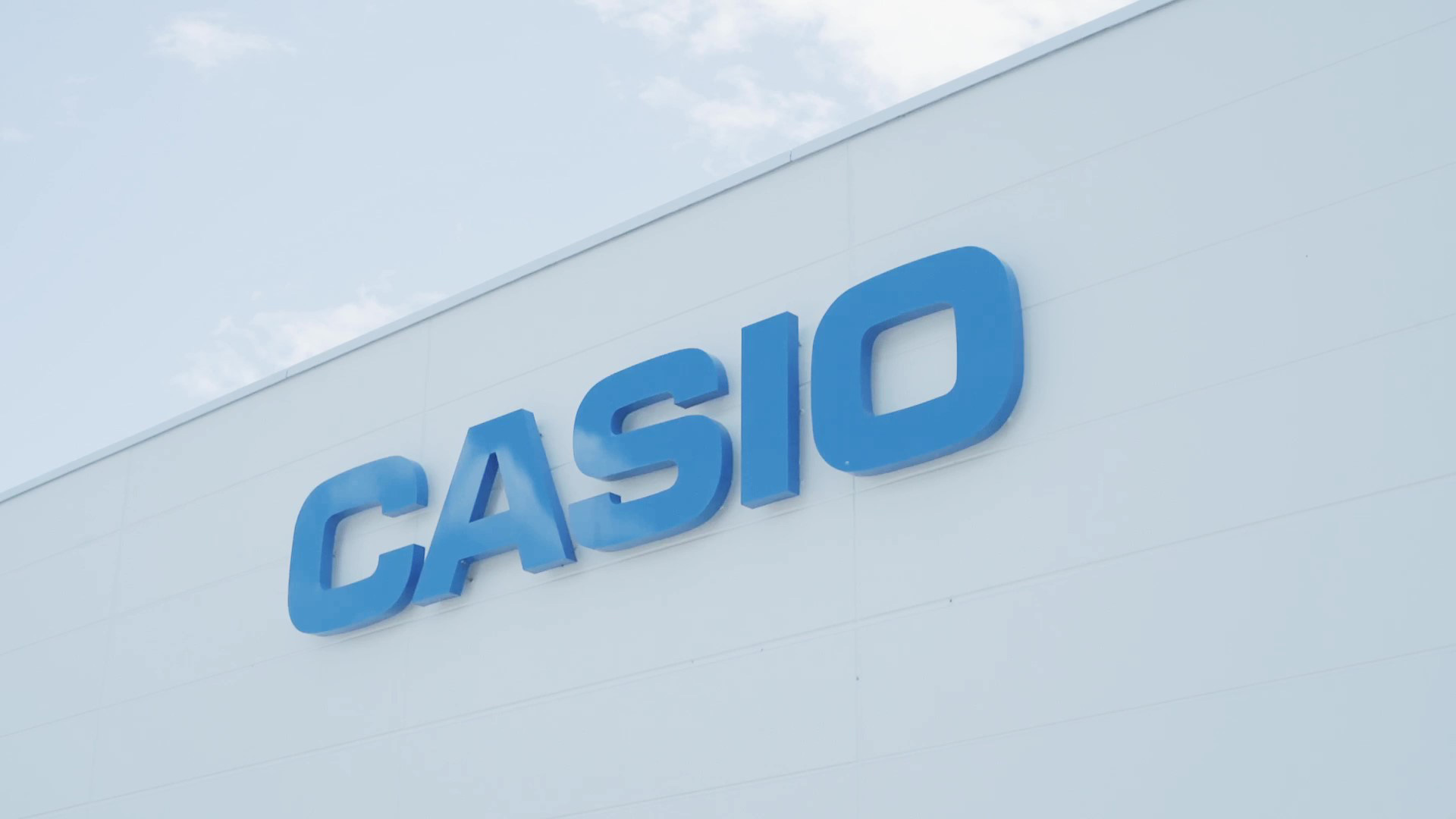
Yamagata Prefecture is known for the largest harvest of fruits such as cherries, pears, and akebia in Japan and hot springs in all of its municipalities. In this prefecture, there is a manufacturer that consistently adheres to Made in Japan: YAMAGATA CASIO. As the only manufacturing site in Japan of the CASIO Group, which is known for the production of G-SHOCK, this manufacturer was established in 1979, has 607 employees, and produces watches, calculators, and medical devices. Maintaining its presence as a mother factory that controls group manufacturing sites in Thailand and China, it has promoted digital production. In early June, when the harvest season of “Sato Nishiki”, premium grade cherries, had just started there, we visited this manufacturer in Higashine City, with a population of 48 thousand, located in the central part of Yamagata Prefecture.
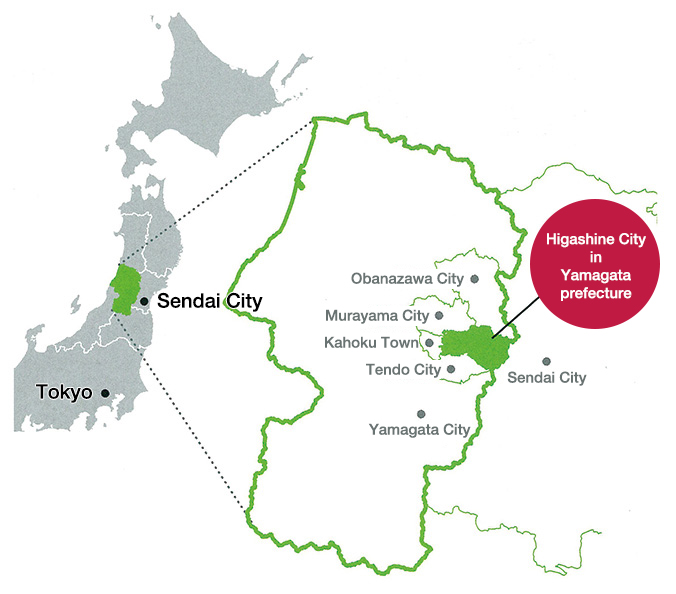
Improving QCD toward realization of Smart Factory
Takumi Fukushi
President and chief executive officer of YAMAGATA CASIO CO., LTD.
and executive officer and production manager of CASIO COMPUTER CO., LTD.
President and chief executive officer of YAMAGATA CASIO CO., LTD.
and executive officer and production manager of CASIO COMPUTER CO., LTD.
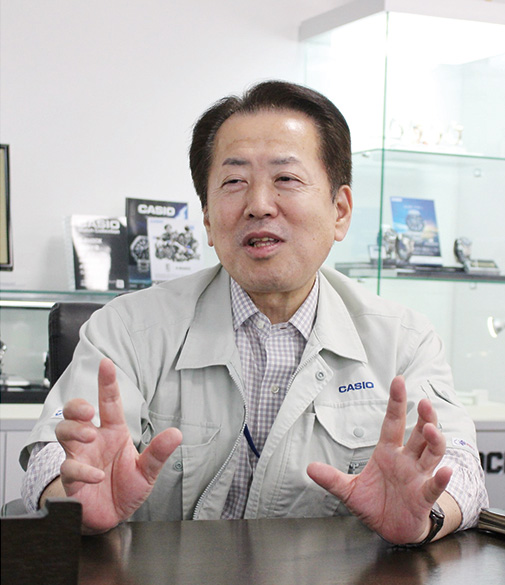
They “will improve the “perceived quality” with craftsmanship to continue production as a mother factory in Japan,” said Mr. Fukushi.
Promotion of the digitization of screw fastening
You take a vertical integrated approach to manufacture CASIO products from the design and production of molds, molding, decorating, to assembling in one factory. What area do you focus on to improve productivity and quality?
“CASIO COMPUTER has promoted various production reforms such as the PLM (Product Lifecycle Management) on the development side and the SCM (Supply Chain Management) on the procurement side. As a manufacturer, we are committed to realize Smart Factories. In other words, we are trying to make a factory that reforms the operating process to improve, advance and sustain QCD (quality, cost and swift delivery) through digitization. We make such efforts horizontally involving all internal organizations. Even if each organization reforms, it is difficult to see the result.”
As a mother company, specifically, how do you deploy such horizontal approach to overseas factories?
“We have seven scientific calculator production lines in the Thai factory. However, they definitely don’t work simply by introducing automatic machines. After YAMAGATA CASIO planned and tested a new automation theme, its evolved version has been partially deployed in overseas factories. In such case, the personnel of YAMAGATA CASIO visit the overseas factories to set the new machines. Although some automation can be realized by only buying equipment, such automation doesn’t help us win competitions. We need to consider ways to lower the cost and improve the quality. Newly constructed automation lines have greatly improved production capacity while contributing to quality improvement. We use HIOS electronic screwdrivers for fastening screws. The Thai factory also employs them: 3 units out of 11 are HIOS products.”
Safe screw fastening by INTRTORQUE
How does YAMAGATA CASIO use HIOS products?
“We use HIOS products in screw fastening of back covers of watches. This part is the key to assure waterproof performance. An o-ring between the back cover and the case tightly compresses the air. HIOS has been our business partner for over 30 years. HIOS products achieve extremely stable torque, which directly impacts on our products’ quality. And controlling the torque with them is also easy.”
“For manufacturing scientific calculators, there is a takt condition that two screws have to be fastened in seven seconds per unit. When we considered the automatic supply of screws to meet this condition, we noticed that products from other companies were too large, costly, and not cost effective. So, we consulted HIOS regarding this matter. Their readiness was excellent – their products were able to meet our target tact condition, and the implementation cost was about 10% lower.”
“For manufacturing scientific calculators, there is a takt condition that two screws have to be fastened in seven seconds per unit. When we considered the automatic supply of screws to meet this condition, we noticed that products from other companies were too large, costly, and not cost effective. So, we consulted HIOS regarding this matter. Their readiness was excellent – their products were able to meet our target tact condition, and the implementation cost was about 10% lower.”
How many HIOS products does your company use?
“Now we are using about 1,500 HIOS products at five manufacturing sites in the Yamagata Headquarters, Yamanashi Branch, China (two sites) and Thailand. Most of them are screwdrivers. We use about 940 units. Screw feeders and peripherals follow. The HIOS hexalobular “INTRTORQUE” guides a bit to the center of a screw and helps stable screw fastening. We employ this for OCEANUS OCW-P2000.”
Predictive maintenance by HIOS products
Does your company record data on screw fastening and utilize such data?
“In the first place, we have visualized the process data by aggregating data on the number of screw fastenings and frequency of errors in our line of scientific calculators. We are now utilizing such data to improve work efficiency and quality. We believe it can be useful in many other ways. For example, currently we regularly replace the bits well before expiration of their useful life. In the future, we will implement predictive maintenance in which optimal replacement timing is determined based on recorded data. This can save on running costs and eliminate unexpected production stops.”
Production shift to overseas countries has been mainstream for a long time. Under such circumstances, what kind of efforts you are making in order to continue production in Japan?
The raison d'etre of YAMAGATA CASIO is in manufacturing of high-end watches such as “MR-G”, the highest class of the G-SHOCK product line, and “OCEANUS”, a premium watch for business use. Our mission includes elaborate production of high-end products backed by highly technical skills. We will not be able to survive in the domestic market without daily efforts toward evolvement of operators, production facilities, inspection equipment, and automation technology. We also have to exercise effective supervision over overseas factories. In addition, we value the user first and try to improve “perceived quality” so that customers are satisfied with using our products. Our manufacturing lets customers feel the quality of craftsmanship. We hope that our customers feel the benefits of having our products and recognize the value, that is more than the amount they paid. That’s the manufacturer we want to be.”
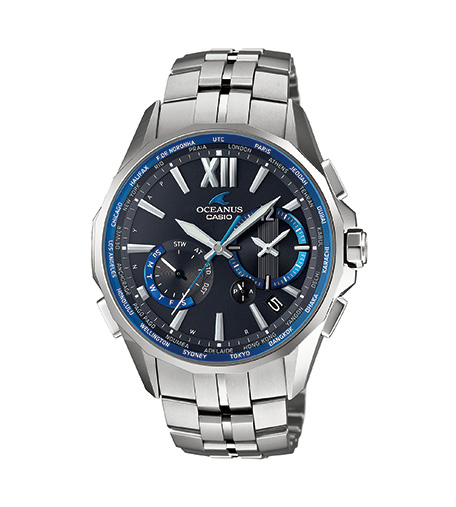
“OCEANUS Manta” with its refined blue color
Factories dedicated to manufacturing watches produce quality products
Exceptional craftsmanship
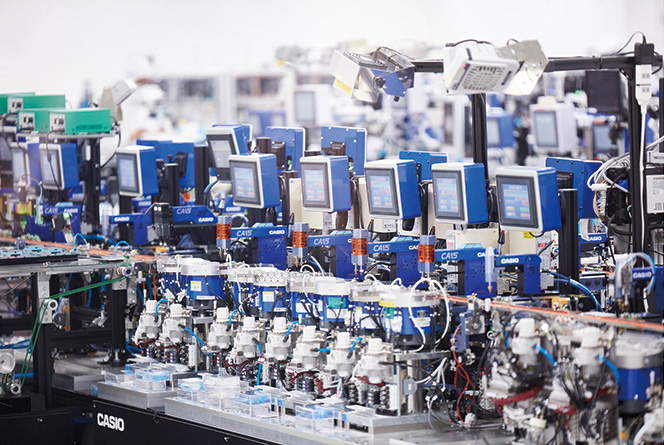
The assembly factory is surrounded by metal wires with earthquake-resistant properties. It is full of equipment with few operators.
“MR-G”, the highest class of the G-SHOCK product line, and the “OCEANUS”, premium watch for business persons, feature titanium exteriors where super-hard coating of diamond-like carbon is applied to the full-metal case with shock-resistant structures. The showroom in the new building completed in 2018 showcases these products. They are manufactured at the factory dedicated to watches which is located next to the showroom.
Monitors and small devices are tightly packed in the manufacturing lines. There are about 10 operators in the space between them. First I thought that if an earthquake happens, it can cause a catastrophe, but felt relieved after hearing that “this area surrounded by metal wires is isolated from other areas and there will be no problem even if an earthquake with seismic intensity of 6 or greater happens”. Not to mention, assembling parts that are all miniscule, including a gear with a shaft diameter of 0.2 mm to be molded to join with a magnet part.
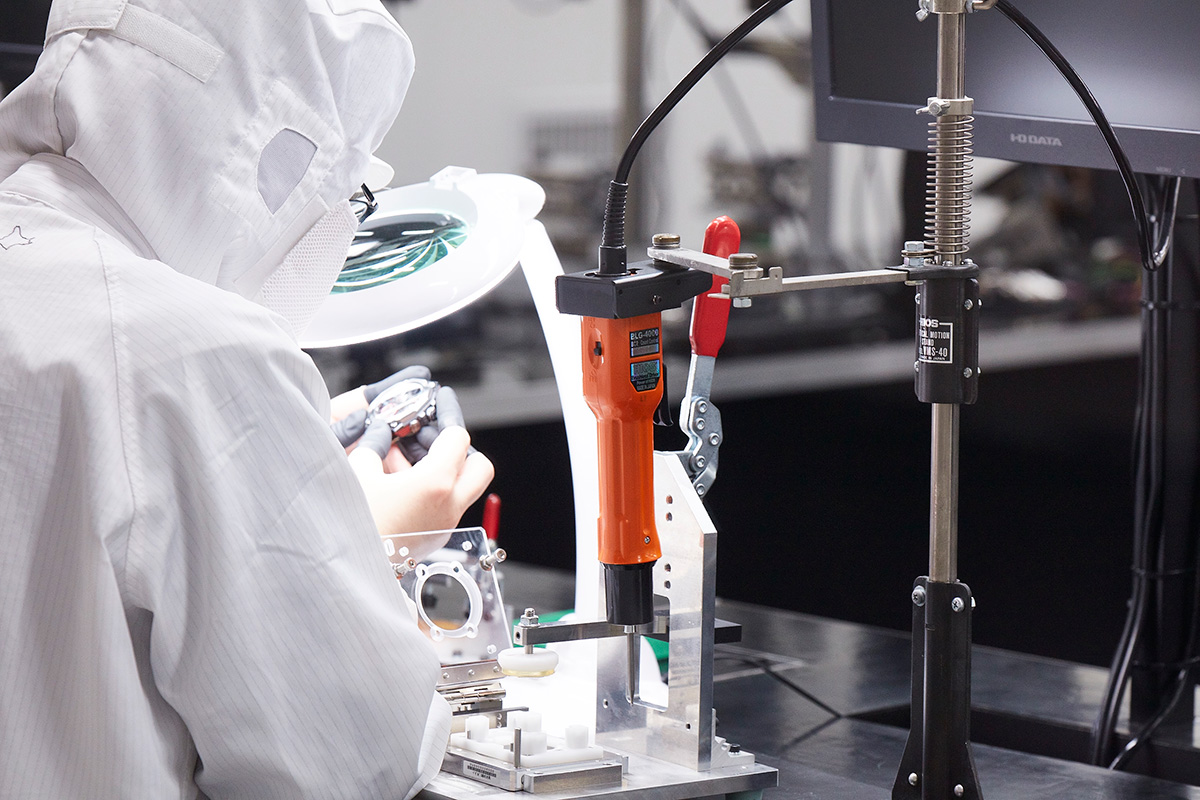
A meister securely fastening screws using the JUKUREN Screwdriver with the magnifier.
In the center of the factory, the production processes are lined up as: assembling of product modules → attachment of solar panels and dials → fitting of needles → adjustment of the position and angle of needles → adjustment of the height of needles → fitting of cases and attachment of back covers.
More than nine million units of G-SHOCK are produced annually, and five to ten percent of them are produced here. This factory manufactures high-end models only (price of MR-G is over 300,000 yen).
More than nine million units of G-SHOCK are produced annually, and five to ten percent of them are produced here. This factory manufactures high-end models only (price of MR-G is over 300,000 yen).
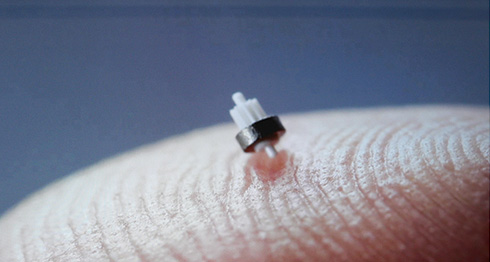
A gear made of resin on a fingertip. It is molded with magnets after they are set to a mold.
A gear made of resin on a fingertip. It is molded with magnets after they are set to a mold.
The scientific calculator factory realizes fast production by introducing automation
Improving every day by quantifying human movements
Improving every day by quantifying human movements
The scientific calculator factory has advanced automation by applying the technologies of the watch movement line. Director Shinichi Kimura explained that soldering, screw fastening, and image inspection can be performed without human operation.
“Automation eliminates variation of the quality, which enables us to achieve flexible production and respond to improved or decreased production load. If the production decreases, we can leave machines idle, not humans.”
According to him, it is possible to produce 3,500 units in one day and 7,000 units with two shifts. The production technologies established here have been deployed overseas.
“Automation eliminates variation of the quality, which enables us to achieve flexible production and respond to improved or decreased production load. If the production decreases, we can leave machines idle, not humans.”
According to him, it is possible to produce 3,500 units in one day and 7,000 units with two shifts. The production technologies established here have been deployed overseas.
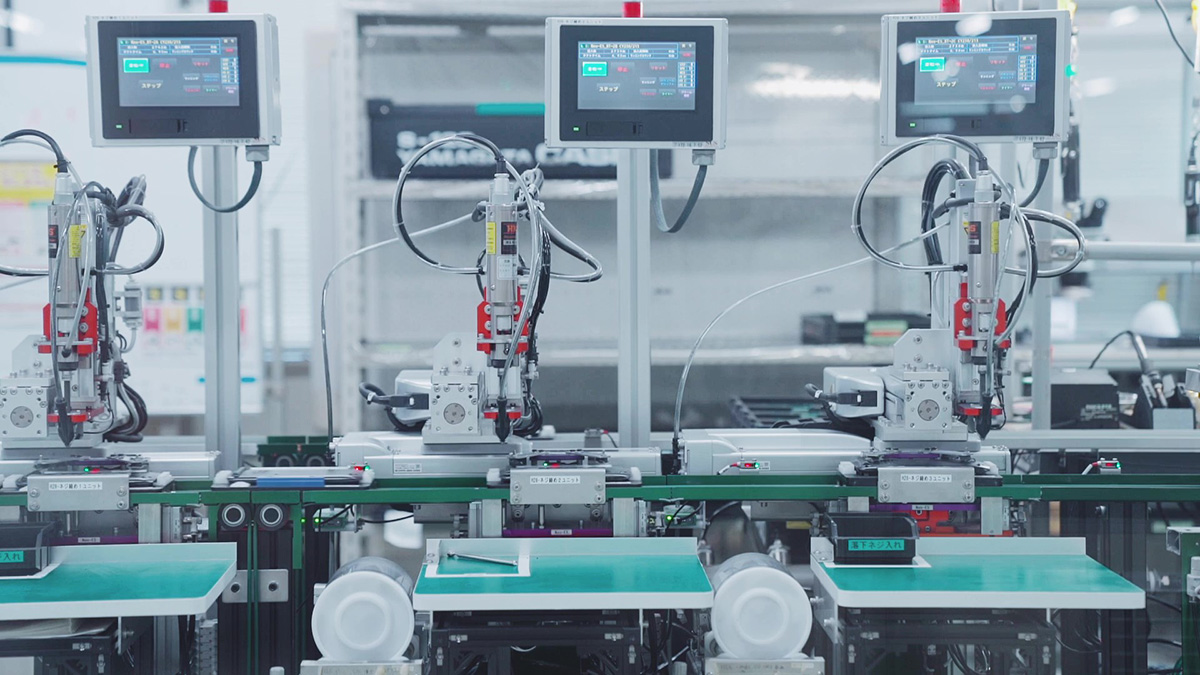
The screwdriver for HIOS automatic machines including screw feeders enables fastening of two screws within seven without variation – this process used to consume more time.
Of course, human operators are still needed. According to Mr. Kimura, for lubricant application and soldering of lead wires, “we rely on manual operation for tasks that are not suitable for automation. It is not always good to mechanize everything. We need to consider cost as well.” When we looked closer, several cameras are installed around the operators. They are recording data on how many workers perform each specified task, with what posture, and how long it takes.
“It’s part of the commitment to realizing a Smart Factory. When production efficiency decreases, it’s possible to analyze where the cause lies and improve it.”
What percentage does the work time constitute of the labor hours? How is the expected work time for a specific task different from the actual time? Such data is numerically analyzed. In such a situation, it is a concern that operators cannot feel at ease. However, the work efficiency and product quality have surely improved.
“We make improvements from the standpoint of eliminating unnecessary efforts and reducing lead time as much as possible. We will combine automation and manual operation and commit to improve QCD as a whole while relating this to the realization of a Smart Factory.”
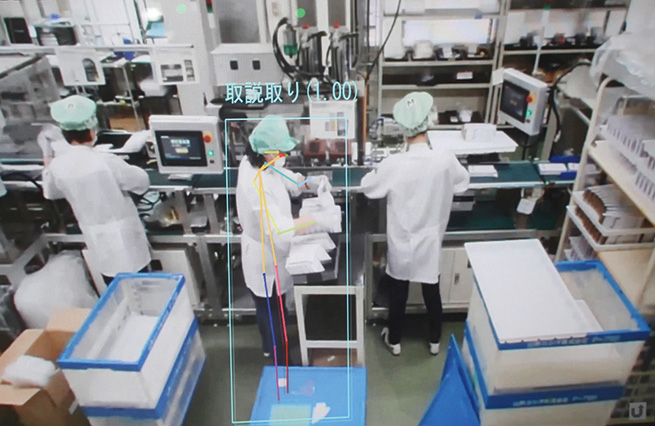
Camera image recording the movements of operators