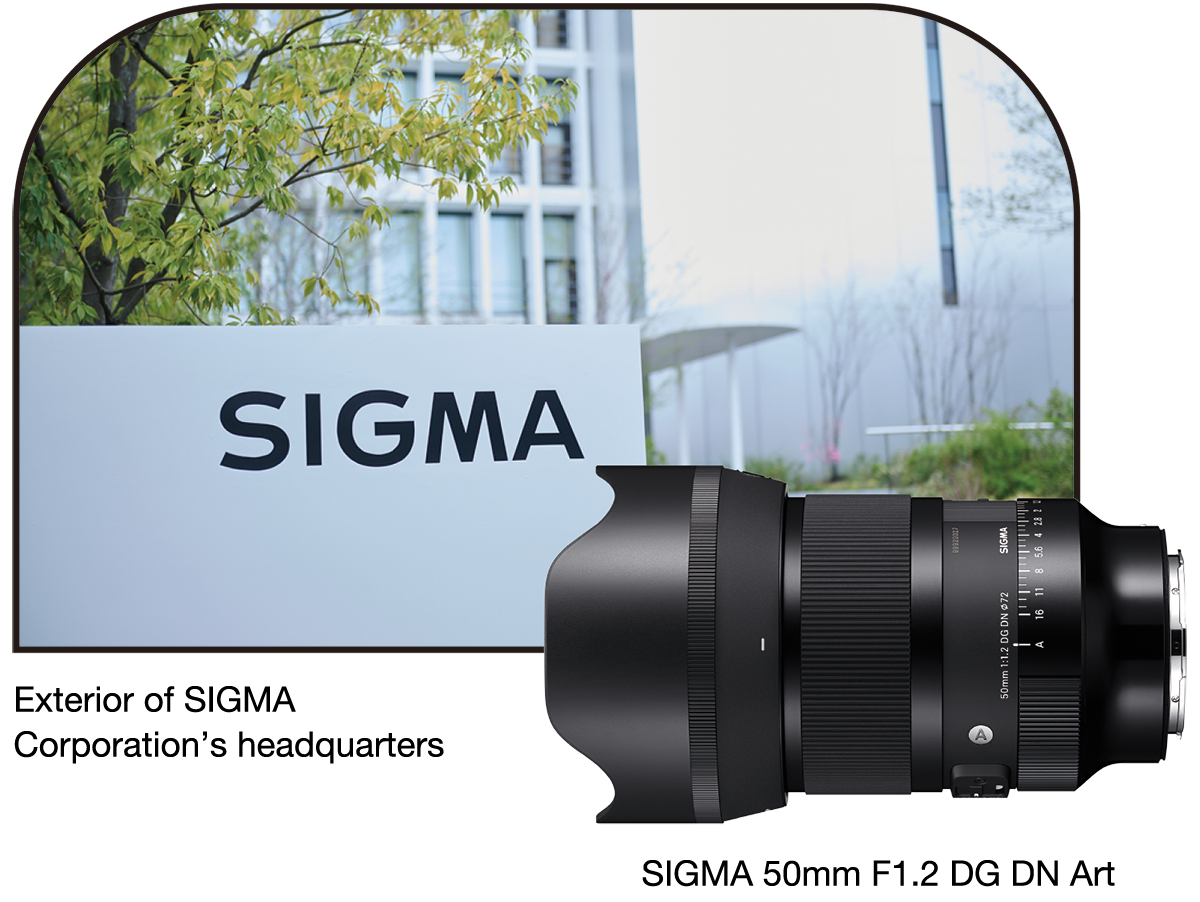
the president
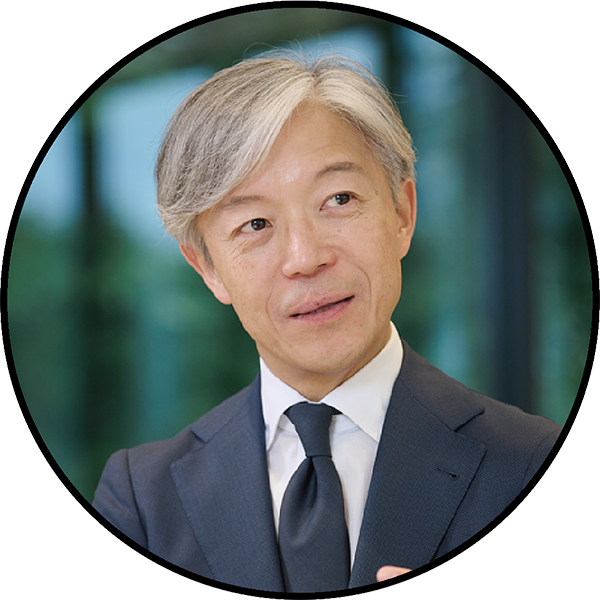
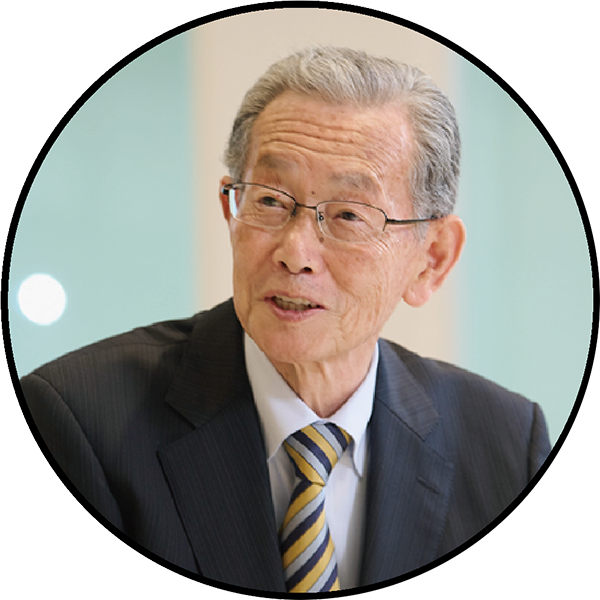
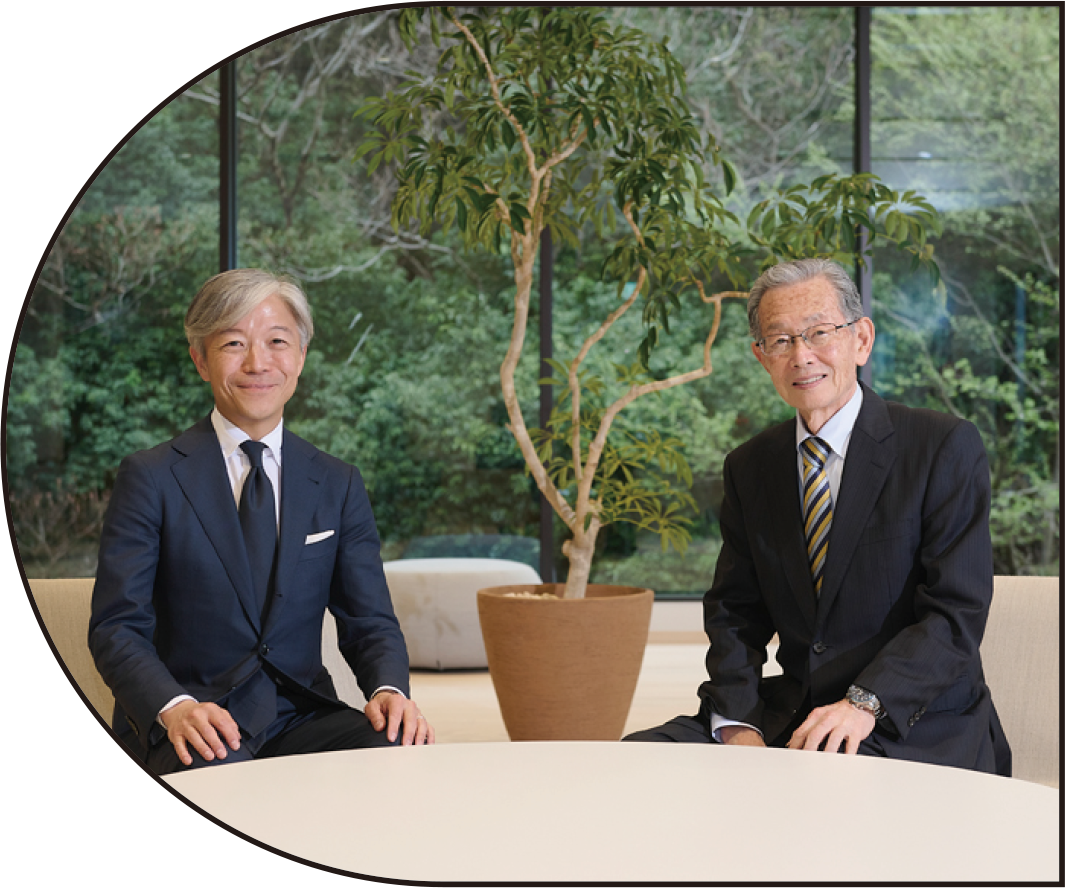
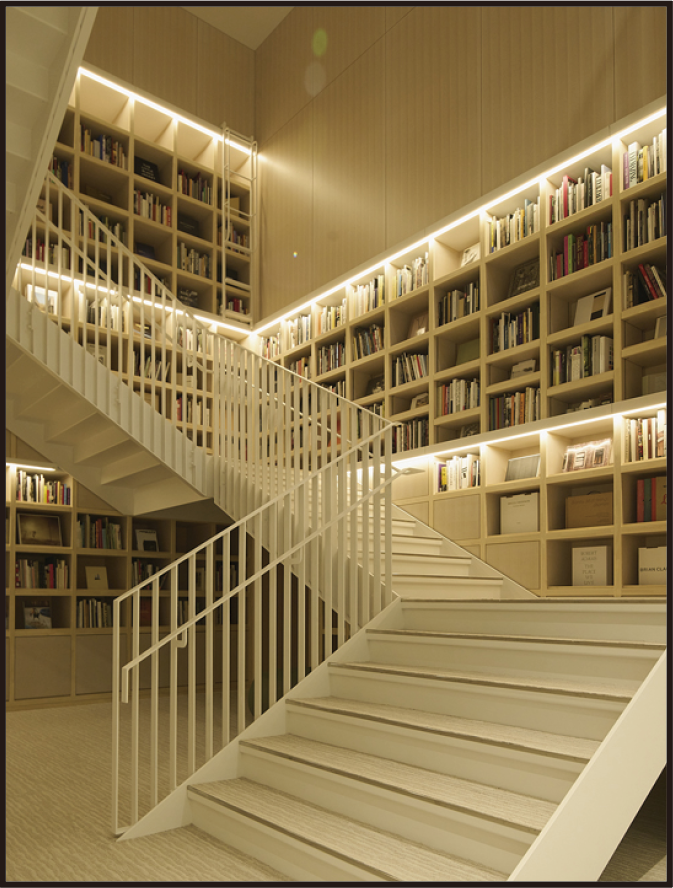
Commitment to overwhelming excellence in quality
Totsu:SIGMA has developed many groundbreaking products different from major camera manufacturers. What is the intention behind this?
Yamaki:When you think about buying a camera, the first thing that comes to mind is products from domestic manufacturers such as Canon, Nikon, and Sony. Then, naturally, you buy lenses from the same manufacturer, too. As an interchangeable lens manufacturer, we have to make sure that consumers choose our products. In other words, we have to develop products that overwhelm them with groundbreaking performance and quality and then be recognized by that. HIOS constantly develops and markets a series of highly competitive products. We use many of your electric screwdrivers in our factories.
Totsu:Thank you. HIOS was established in 1970 when screws with straight slots were still widely used. Straight slot screws were not easy to use, and about 3 years before that, we devised the Totsu Screw with improved slot and that enabled stable screw fastening. We established the company to widely market this screw. For the following half century, we have had a journey as a manufacturer specialized in screws and screw fastening. What is your philosophy of manufacturing?
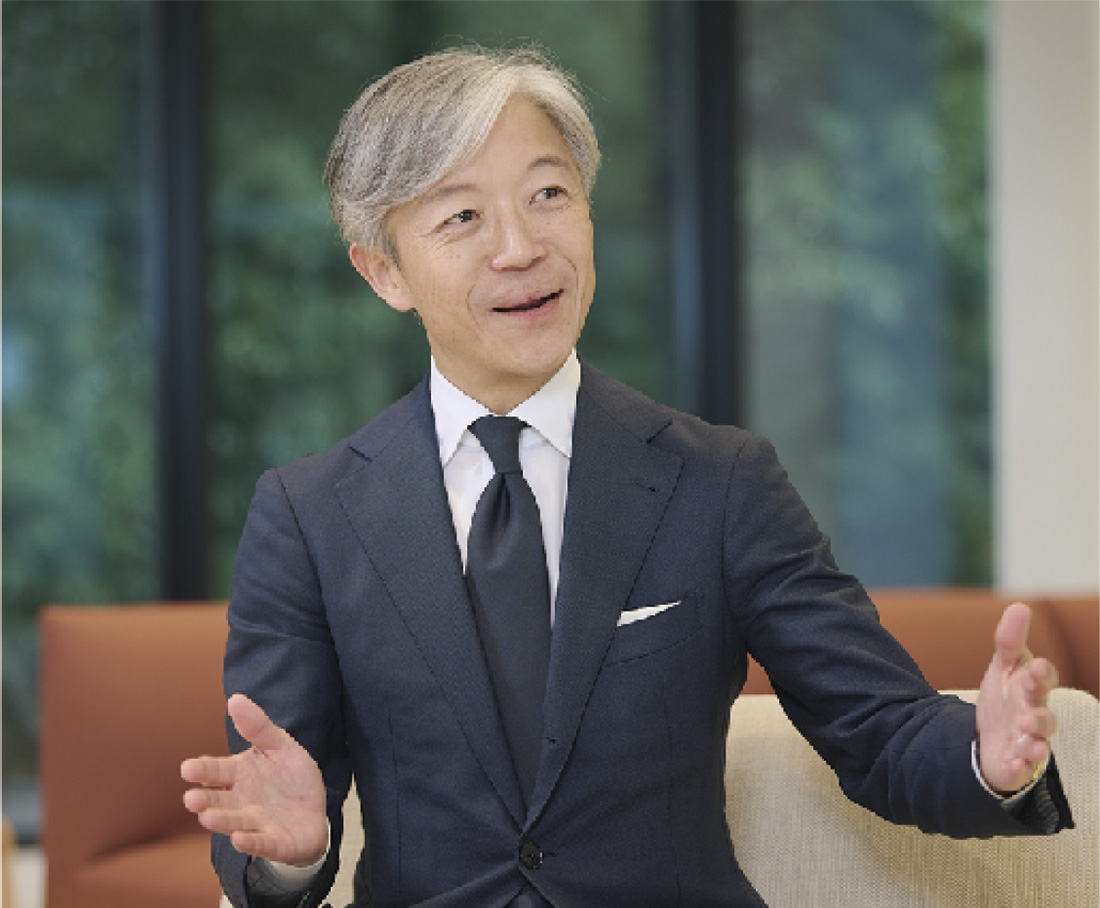
Yamaki:SIGMA's products are not born from market research. The starting point is the passion to "Create something that we truly aspire and can be proud of." It is not about high sales, but taking pride in our products. We constantly follow this credo with great sincerity. In order to maintain this approach, we choose not to go public. And what is your philosophy, Mr. Totsu?
Passion drives innovation
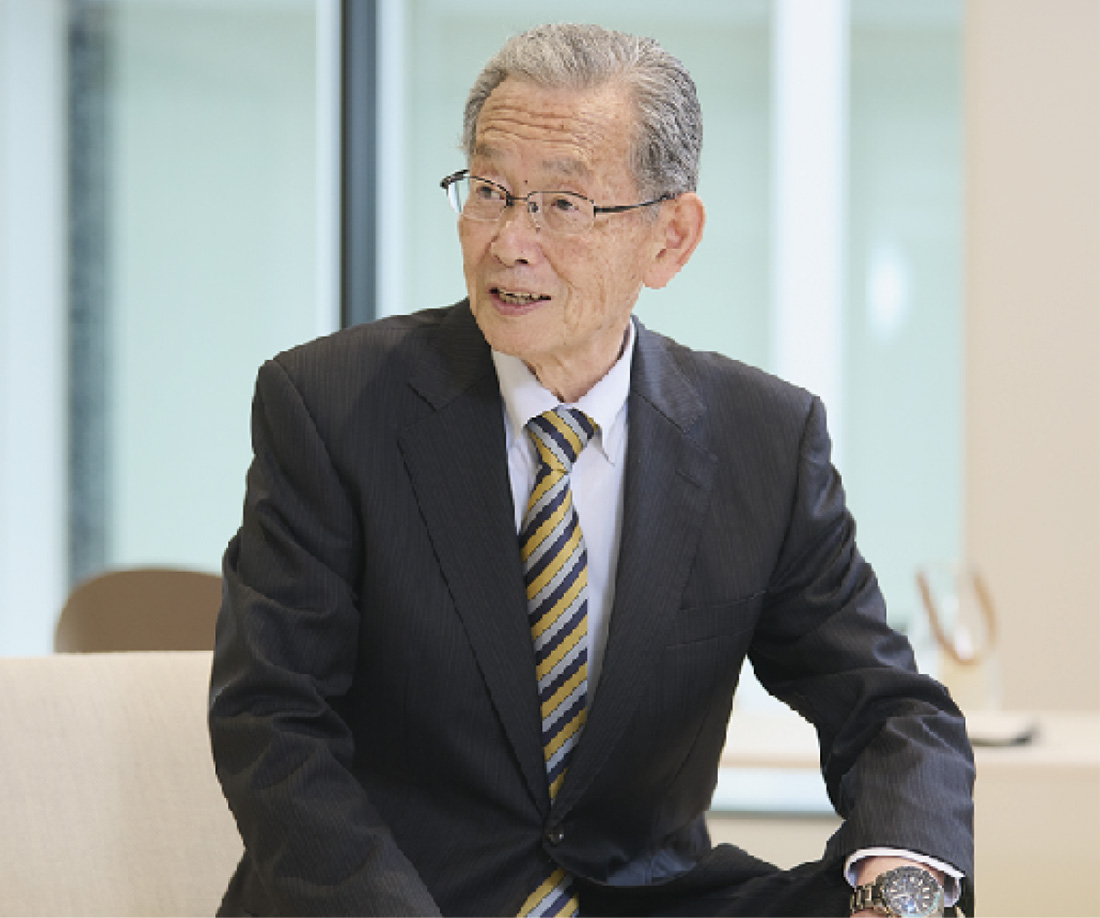
Totsu:Screws and screw fastening may seem simple, but actually they are so intricate with many factors correlated. Proper screw and screw fastening bring about a wide range of positive effects, from product safety to workability of operators. When we think about screw innovation and start to see what we previously didn’t see, then something new that we hadn’t seen comes up. We're constantly researching to bring about innovation in the world of screw fastening that people tend to miss. So far, we've applied for about 200 intellectual property rights including patents. I don't want to copy and don't want to be copied. In the actual manufacturing, I heard that all of SIGMA's products are manufactured domestically.
Yamaki:All 84 models of lenses and cameras are manufactured at the Aizu Plant in Bandai-machi, Fukushima Prefecture. Even during recessions such as the repeated appreciation of the yen and the collapse of Lehman Brothers, in order to protect jobs and manufacture added-value products, we have maintained domestic production. I believe that we have reached the highest level that we can attain, not only for lens processing but also plastic molding, magnesium processing, painting, substrate mounting, product assembly, and processing of molds and small metal parts.
Totsu:I’ve heard that you use our electric screwdrivers on your assembly line.
Yamaki:Interchangeable lenses need to be accurately assembled so that the optical axis are set as designed. We have heard about reputation of HIOS’s electric screwdrivers and that they can securely fasten small precise screws. In addition, they are ideal for workplaces where many female operators work because they are compact, lightweight, and easy to use. What vision do you have for HIOS’s product development?
Aiming to be a world-class brand
Totsu:There are two major themes: automation of screw fastening and environmental friendliness. The trend of automation of screw fastening by robots is growing day by day, and we are pursuing technologies for fastening by smaller robots, higher precision, and durability. We are also working on the development of highly adaptable screws that can be easily dismantled as a measure to address environmental issues of high global concern. Mr. Yamaki, what is the future vision of SIGMA as a company?
Yamaki:We would like to contribute to the development of filming and photographic culture, and to become the world's best company in optical technology. In the 20th century, German manufacturers held that position. Now, SIGMA is becoming the driving force behind the development of optical technology in the 21st century.
Totsu:Screws and screw fastening are fields that can change many things. We will do our best so that HIOS’s philosophy is recognized worldwide. Thank you for your time today.
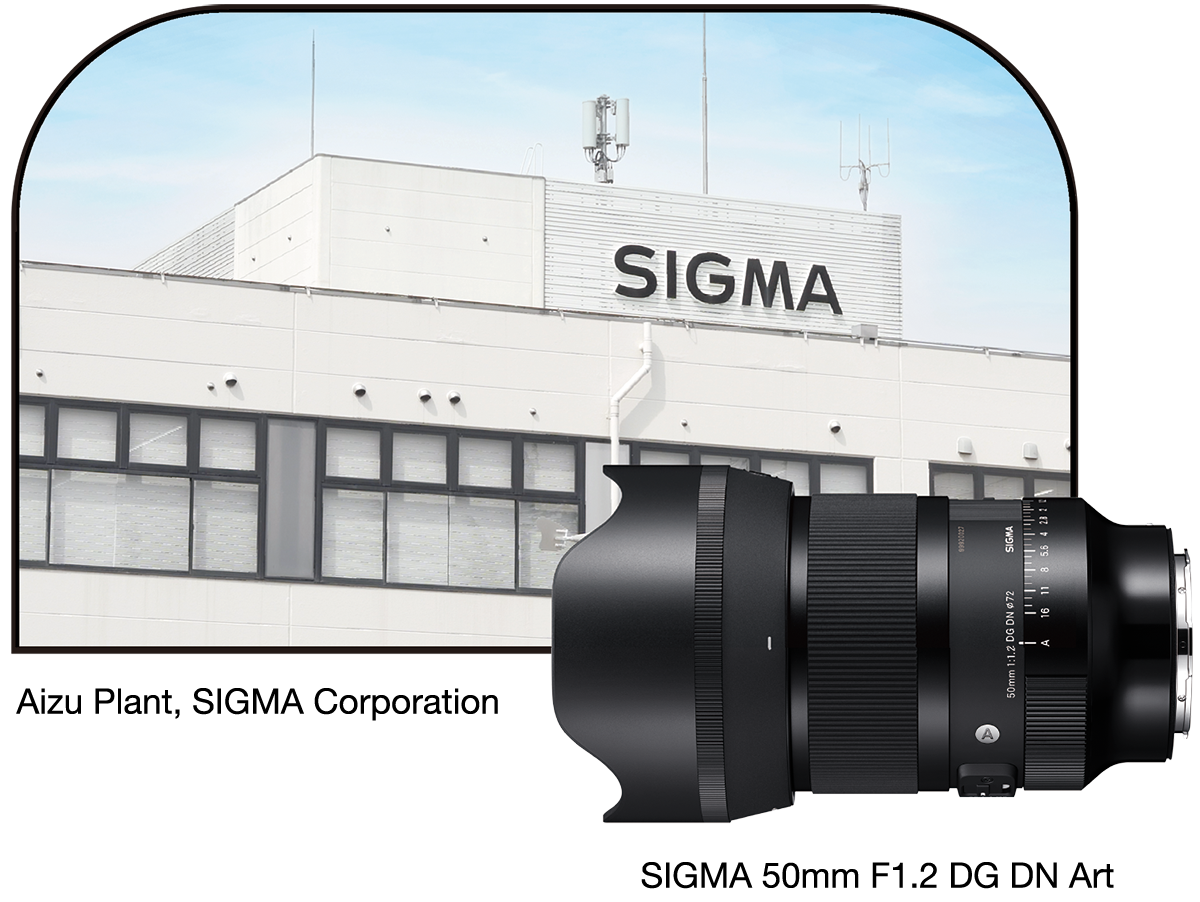
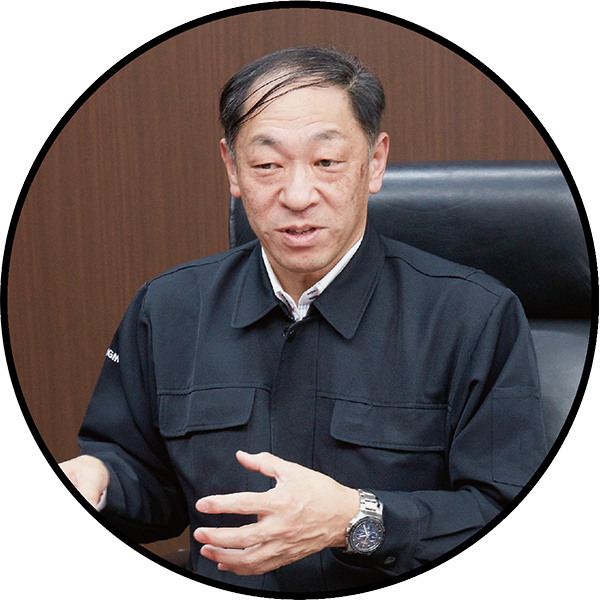
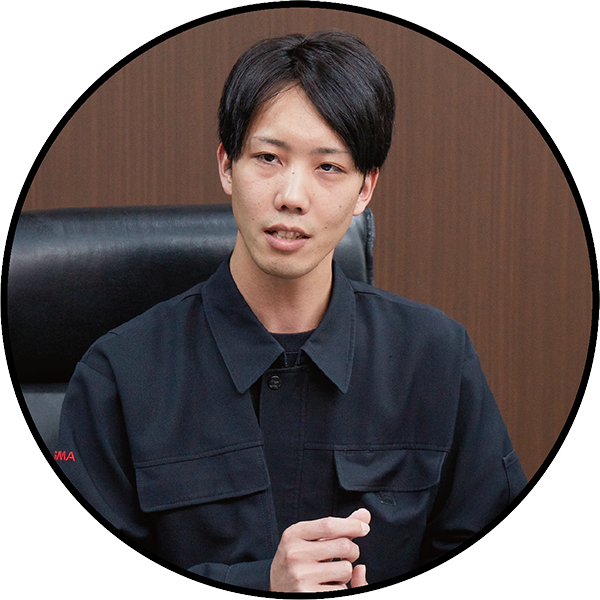
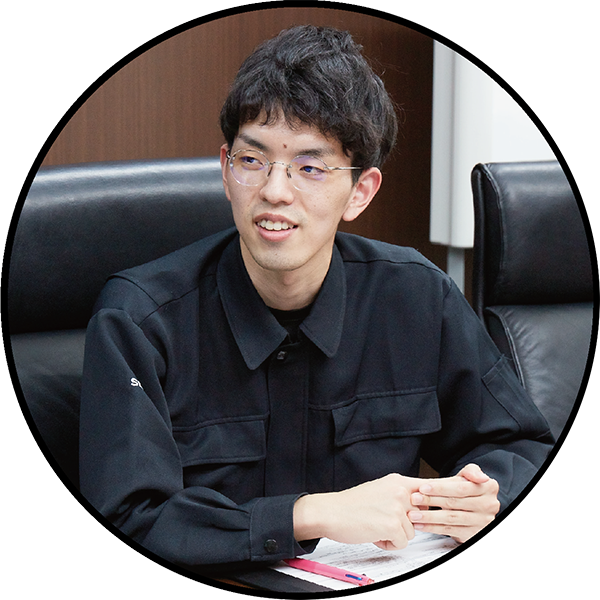
Brushless screwdriver to support monthly production of 70,000 units
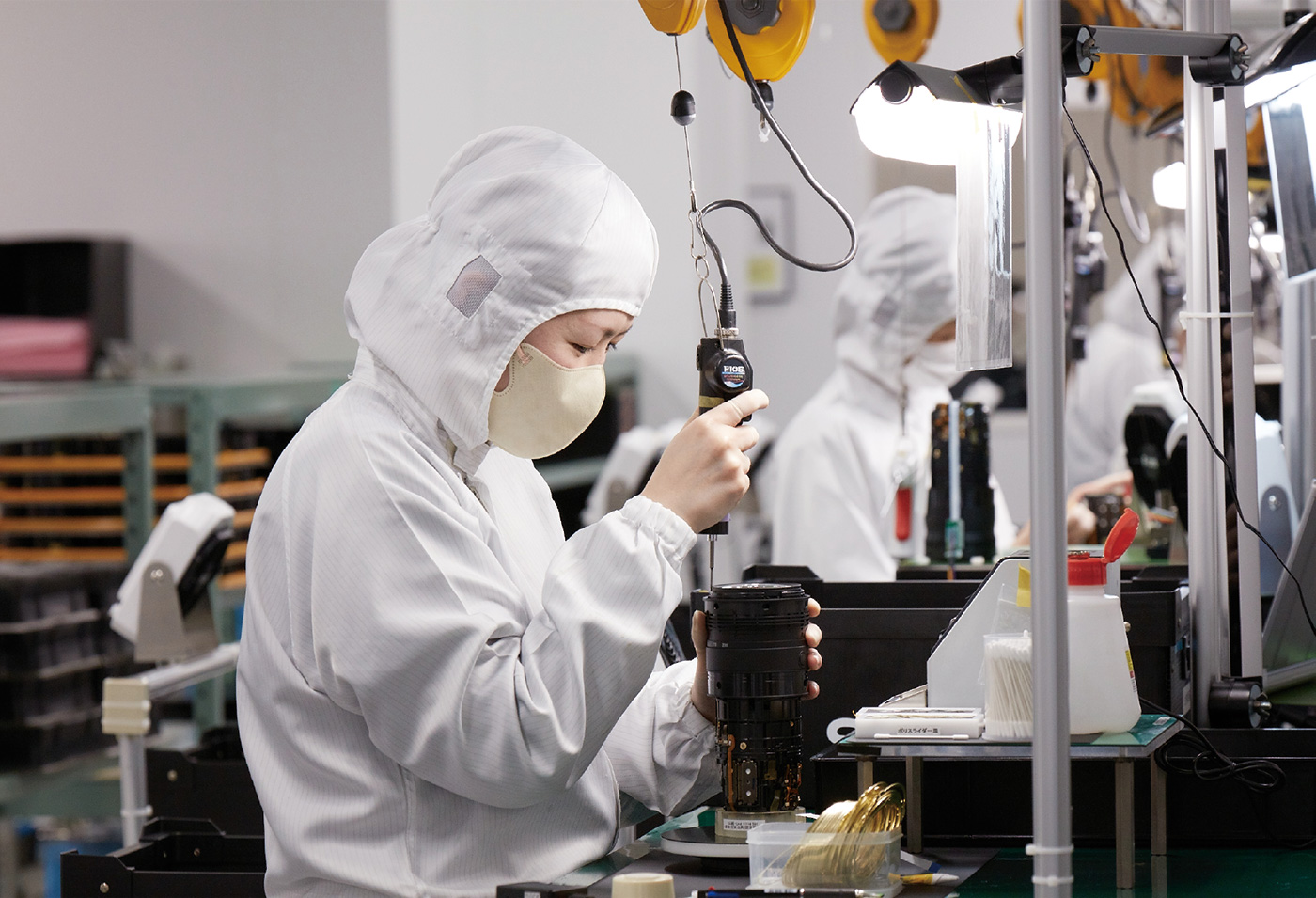
Yutaro Kida, who has worked on production technology for six years, comments about SIGMA's manufacturing, "We try to give our products a sense of quality." For example, the lens is designed so that the lens ring smoothly moves when the lens is zoomed, then the user feels the sense of quality. A graceful feel is also important when it comes to the click of the hood on the lens and the appearance of the inside of the lens barrel when looking through interchangeable lenses. Interchangeable lenses are assembled in a clean room to prevent dust and other contaminants from entering the lens. There are 200-300 parts, and operators are assigned to each process. Most of the operators are females. They work with precision parts. The workability is improved by ingenuity at the design stage and devising jigs, and operators assemble the parts with great skill.
The HIOS electric screwdriver is the key to this efficiency. The screws used are 1.4-2 millimeters in diameter and 1.0-10 millimeters long. They rhythmically fasten small cumbersome screws with electric screwdrivers. The plant uses 650 units, and all of them are HIOS products. The BL-2000, which uses a brushless motor, accounts for 90% of the total. Yuki Suzuki, a member of the Assembly Engineering Division who has worked at SIGMA for 10 years, says, "Maintenance-free and stable torque performance lead to consistent assembly quality."
A brushless motor without a carbon brush, doesn’t generate carbon particles. This eliminates the cleaning of the interior of screwdrivers that used to happen once a month. At Aizu Plant, it took seven years to switch to BL-2000. The switching was completed three years ago.
Pursuing high levels of assembly quality
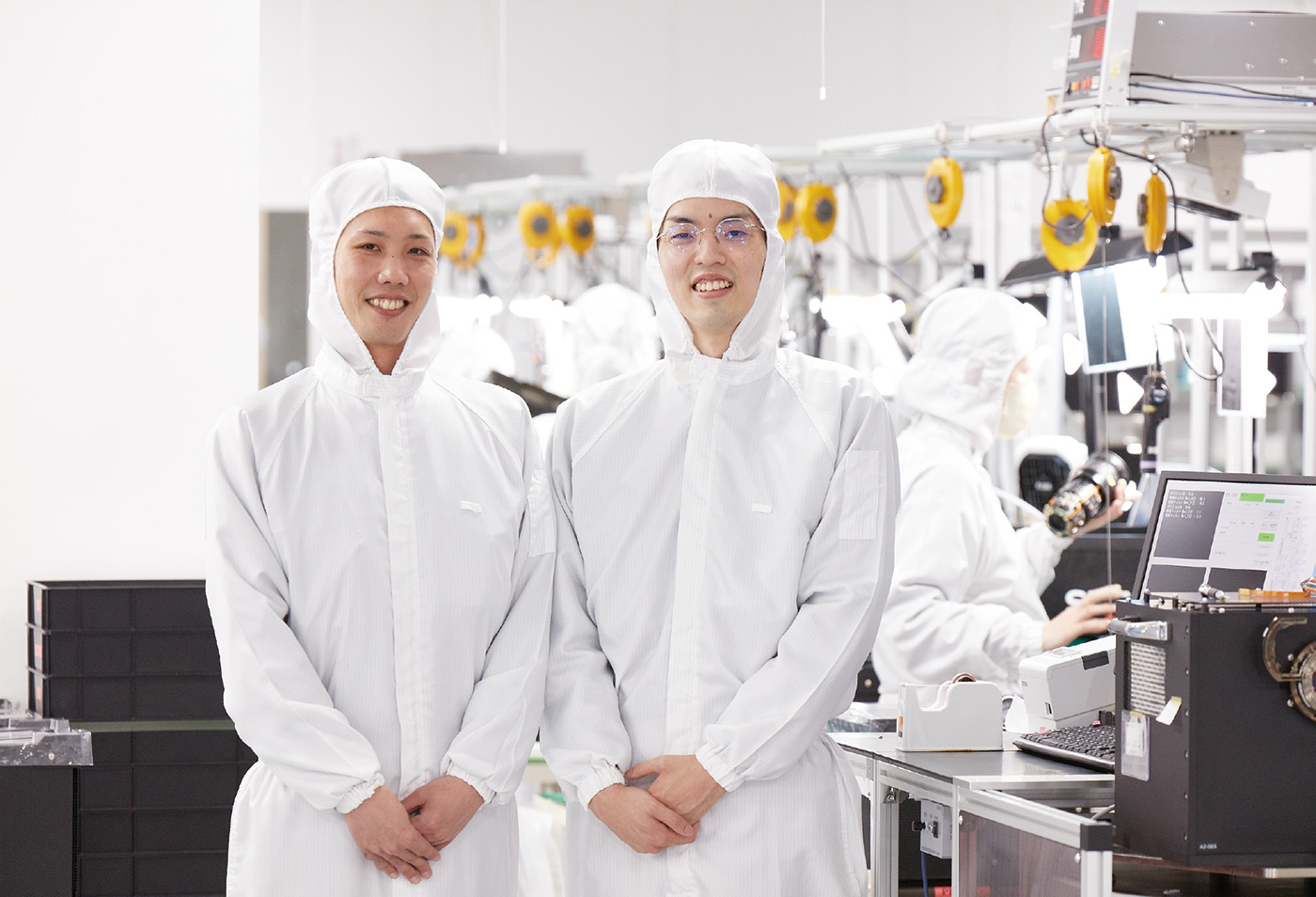
The screwdriver's lightness of 254 g also contributes to the assembly quality of interchangeable lenses. The screwdriver can be held stably, improving work accuracy and efficiency. The lighter workload also reduces fatigue.
The shape of the screwdriver and the position of the operating switches are also designed to improve workability and reduce fatigue. It is said to be easy to grip and feels good. Most importantly, Suzuki says, "I've never heard of it to break down." He greatly relies on the electric screwdrivers of HIOS. The Aizu Plant is the only manufacturing site for SIGMA, a company that focuses on domestic production. Competitiveness holds the key to SIGMA's growth, and there is no end to the pursuit of advanced manufacturing. In order to win the unwavering trust of customers, HIOS will continue to take on challenges in manufacturing. (Courtesy abbreviated)