
Venturing into next-generation manufacturing with ultra-low-volume, high-mix production
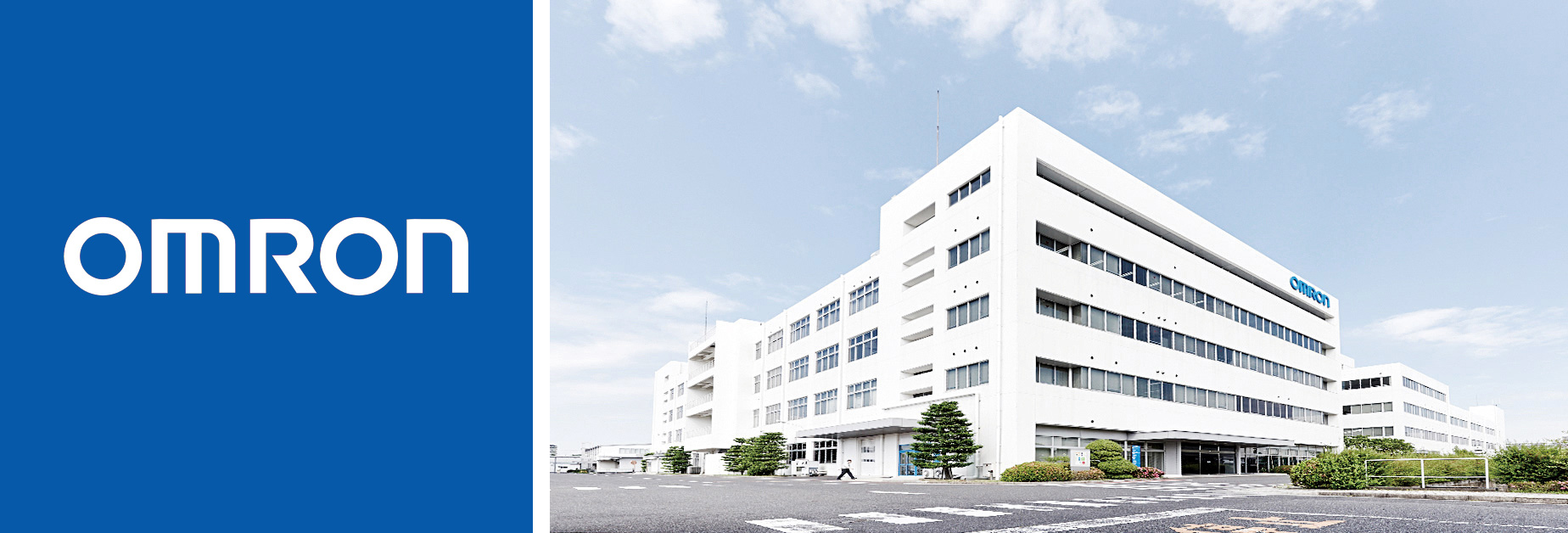
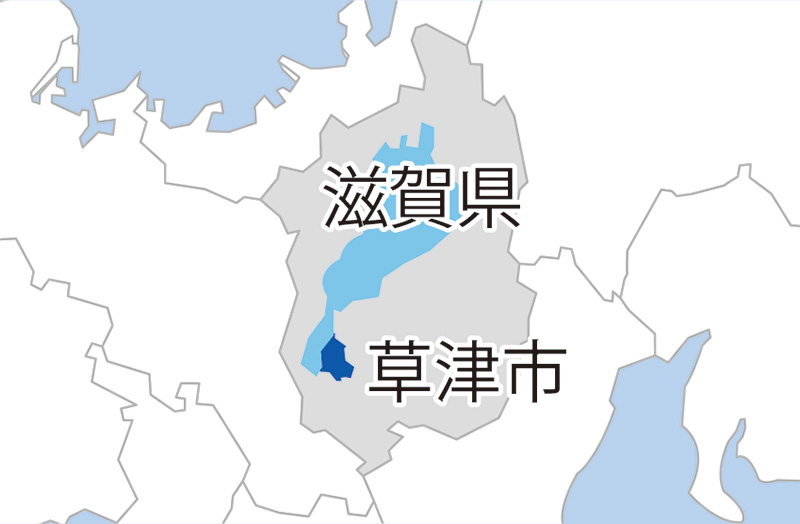
OMRON Kusatsu Factory
(Kusatsu City, Shiga Prefecture)
Lake Biwa, Japan's largest and oldest freshwater lake, is said to have a history of approximately four million years. Facing the southeast of the lake, Kusatsu City, Shiga Prefecture continues to develop as a focal point between Kinki and Chubu metropolitan areas. It is one of the few cities in Japan where the population continues to grow despite the country's declining birthrate and aging population. Kusatsu Factory, the main base of OMRON's factory automation business, is at the forefront of manufacturing in this region. Inheriting the philosophy of the company's founder, Kazuma Tateishi, the Kusatsu Factory works on uninterrupted productivity improvement.
Semi-automation and big data analysis are sources of competitiveness
OMRON Kusatsu Factory manufactures PLCs, servo drivers, image processing devices, and other control devices that are at the "heart" of factory automation. According to OMRON, they are "highly functional products mounting circuit boards”. While it is difficult to improve efficiency in ultra-low-volume, high-mix production, the factory promotes thorough production improvement through advanced automation and big data analysis. The interview revealed a next-generation production line that is a fusion of OMRON’s technology, on-site capabilities, and unique corporate philosophy.
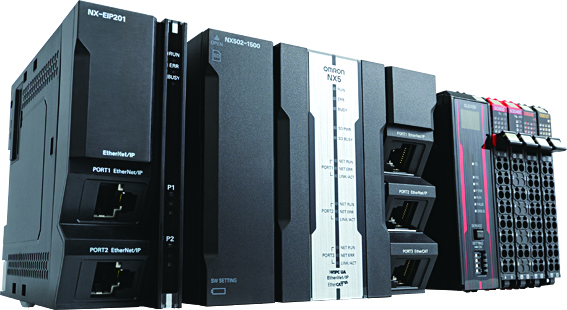
OMRON's NX5 automation controller. The Kusatsu Factory mainly produces this type of controller for factory automation.
ILOR+S leads to dramatic productivity improvement
OMRON Kusatsu Factory is characterized by its ultra-low-volume, high-mix production. The factory is housed in a single building: board mounting shop on the first floor, and assembly and inspection shops on the second floor. Thus, the production area is limited; however, it is surprisingly able to produce as many as 4,800 items. Masahide Kunimoto, Chief of Production Technology Section, Production Management Department, commented as if that is just a simple fact, “As we took on niche manufacturing, the number of items has increased rapidly.” On the second floor of the factory, about 50 cell lines, each measuring 6m x 4m, are lined up in a row. Although the factory doesn’t always produce 4,800 items, it is definitely an ultra-low-volume, high-mix production factory, as 20 units or less per month are produced for more than 85% of the products. The items on the line change from moment to moment, and it is easy to imagine how difficult it is to automate and streamline the production process. How can this challenge be overcome? As it turns out, the solution lies in the company's business activities. OMRON manufactures all of the ILOR+S* required for factory automation in-house, and can use them effectively by bringing out its strength. Furthermore, OMRON identifies issues based on the knowledge of skilled engineers and analysis using IoT, and promotes automation at appropriate points. The goal is not unmanned automation, but rather cooperation between humans and machines. This is in line with mixed-flow cell production and with the corporate philosophy that "what machines can do should be left to machines, and humans should enjoy activities in more creative fields.” “We are willing to leave to people what they are good at, and let machines do the repetitive tasks that machines are good at. Unnecessary automation increases cost and is meaningless," says Mr. Kunimoto.
*Collective name for Input (Input device), Logic (controller), Output (output device), Robot (robot), and Safety (safety-related device)
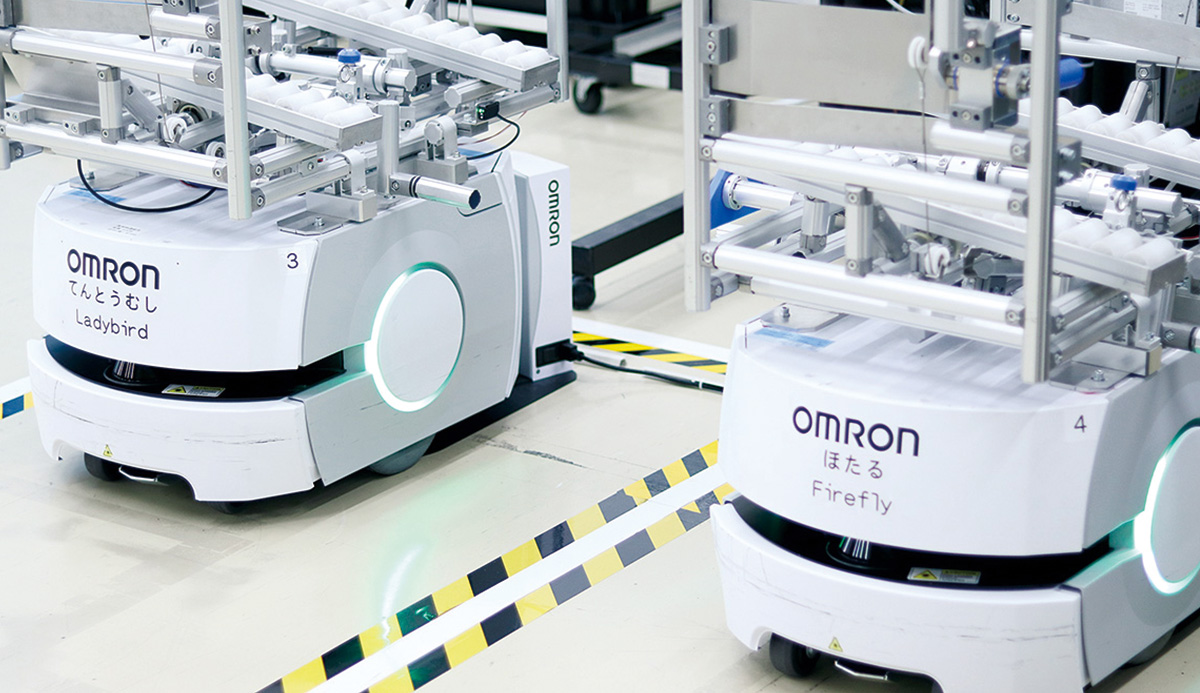
AMRs manufactured in-house transport finished products and supply empty boxes.
System derived from on-site knowledge
that is never lost in a huge amount of data
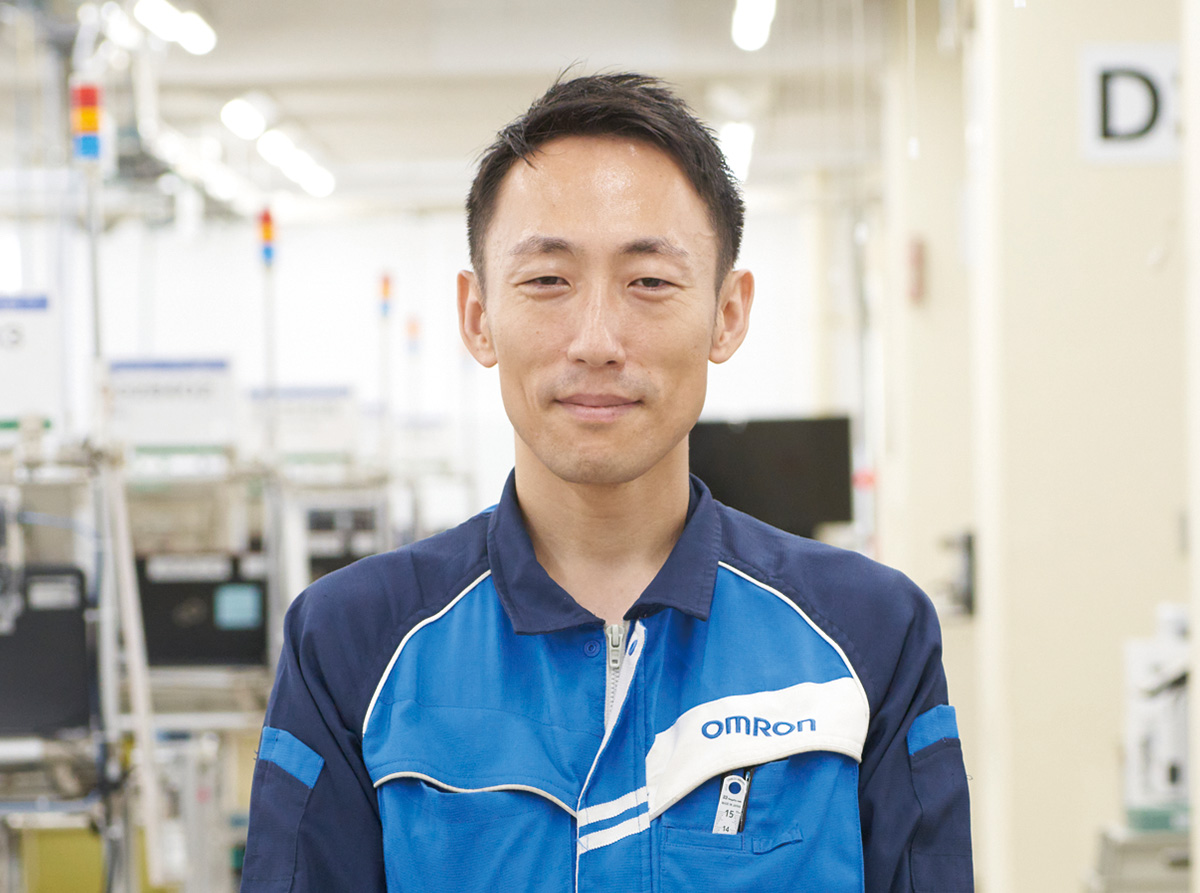
Masahide Kunimoto, Chief of Production Technology Section,
Production Management Department, Kusatsu Factory, Production SCM Headquarters
OMRON Industrial Automation Business Company
Production Management Department, Kusatsu Factory, Production SCM Headquarters
OMRON Industrial Automation Business Company
Characterized by ultra-low-volume, high-mix production, the Kusatsu Factory is promoting automation. For example, we have automated the transport of finished products using proprietary AMRs. A sensor detects a finished product when it is placed on the AMR. This reduces the workload considerably compared to human patrols. We have also replaced the visual inspection of servo drivers with proprietary image processing devices and AI. Automation has improved productivity by more than 200%; however, the factor that leads to this result is the CLCS, which visualizes production on the line by absorbing data from devices at the shops and creating charts and graphs. If the first run yield is low, that is where we start to improve. Because issues can be identified at a glance, the efficiency of improvement is far greater than that of improvement methods depending on intuition. On the line where the system was introduced, the improvement cycle was shortened by three months. Although CLCS is useful for improvement, the original goal was to improve quality. That is why sensors were introduced in the production lines to build a system where, for example, if a screw needs to be fastened four times, the equipment in the next process will not work unless the screw is fastened correctly four times. In IoT, we tend to be overwhelmed by a huge amount of data trying to get all the data at once. However, we calculate the necessary amount of data backward on site and are able to achieve good results at low cost. Specifically, we acquire the number of NGs and their contents from various devices, and one of the means is using the HIOS electric screwdriver "JUKUREN".
“JUKUREN,” which prevents mistakes,
becomes an educational tool for new staff.
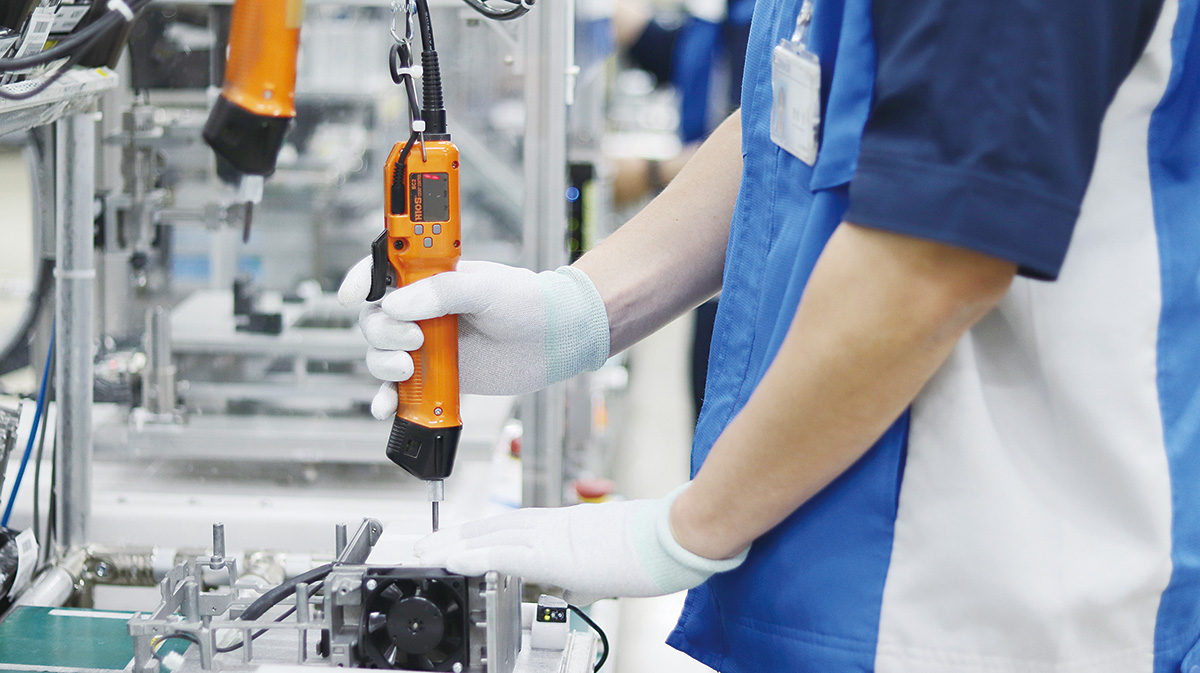
Although JUKUREN has worked with this company longer than I have, I have used JUKUREN for quite a long time. It is especially useful in assembling servo drivers, which have many screws and require torque management. It is great that it is easy for anyone to use and the quality standards including torque, wrong screw fastening, and number of fastenings can be guaranteed. Another advantage is that control can be achieved with a single screwdriver. The Kusatsu Factory uses a large number of JUKUREN, and external devices would take up a lot of space. The most common screw fastening problem at the Kusatsu Factory is missing of screw fastening. Also, since the type and number of screws vary by item, there is also a risk of using the wrong types of screws. Such problem can be prevented by a system that includes JUKUREN. JUKUREN has the function to change settings externally, automatically switching the number of fastening settings as the item to be manufactured is switched. Clearly, the CLCS has reduced the number of defects. The CLCS also serves as a gateway to success for new staff, who first enter the line where the CLCS is installed and then move on to other lines after they become familiar with the system. JUKUREN and CLCS have fostered a sense of security that “even if a human makes a mistake, the system can catch it.” Staff members start to use JUKUREN from the training stage. If they have to use different devices at real production lines, they will be confused. In a positive sense, JUKUREN is an integral part of our production system. Talking about the future policy of the Kusatsu Factory, first of all, last year as we had a shortage of parts and materials, and our customers had to wait longer because of that. From now on, we will pursue productivity and the ability to respond to demand fluctuations, and pursue overall efficiency that is not limited to a single line through highly versatile automation. We also aim to achieve ppb (defect rate of 1/1 billion) in board mounting. Although it is extremely difficult, we will continue to work on production improvement as our mission.
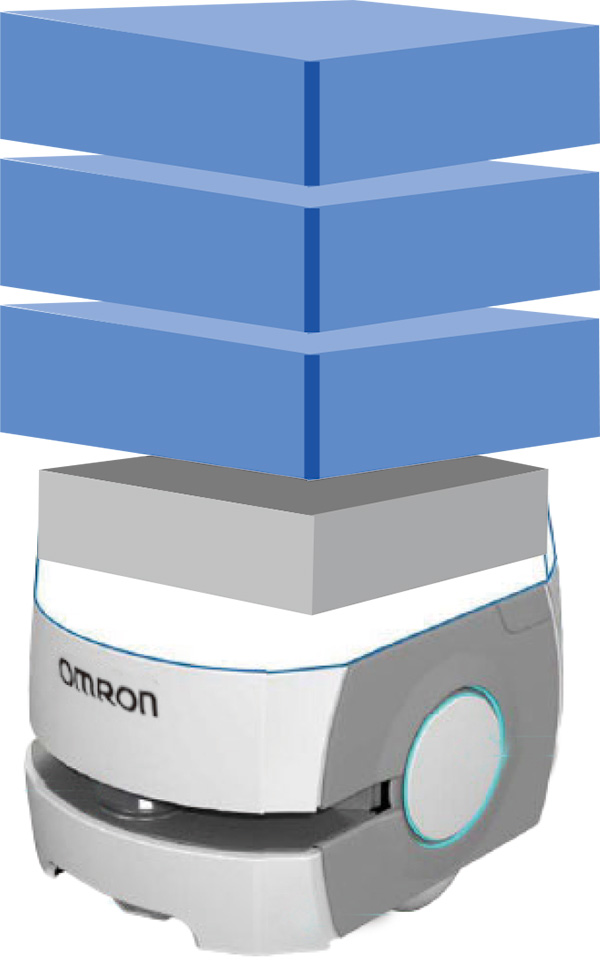
Electric screwdriver is key to defect elimination

HIOS JUKUREN screwdrivers lined up on the servo driver assembly line.
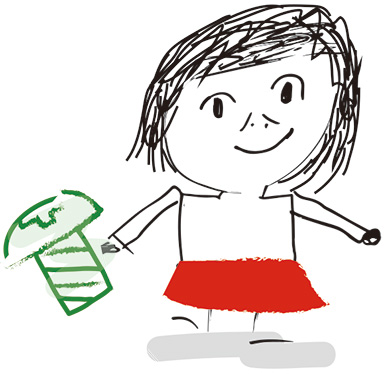
As an example of automation, the Kusatsu Factory has introduced collaborative robots for board mounting. When mounting the boards, solder paste is applied over a metal mask, and the mask must be changed and cleaned every time the item to be manufactured changes. The collaborative robot feeds the masks into the washer. Mr. Kunimoto explains the introduction background, “Collaborative robots move slowly because there is no fence, and people are better in the sense of productivity improvement. However, industrial robots cannot be moved after installation, resulting in loss of flexibility in the line. We chose collaborative robots so as to be able to switch between humans and robots.” The factory is also promoting multifaceted automation, such as finished product transport using proprietary AMRs and visual inspection using proprietary image processing equipment. Through a series of "semi-automation," the cell line has dramatically improved productivity by more than 200%. Such a successful production improvement in the factory has been largely down to the "CLCS (Cell Line Control System)”. The CLCS visualizes production on the line. For example, by summarizing a first pass yield, cycle time, and other data in charts, they identify issues to take appropriate improvement actions. CLCS is also effective in improving quality. In fact, the company has established a system in which “the next line doesn’t physically start unless the previous process is complete” on 13 assembly lines. The key here is the HIOS electric screwdriver "JUKUREN," which detects and prevents various defects, such as missing fastening of a screw or wrong screw length. The screwdriver outputs the work data, which is used for CLCS's big data analysis. The system contributes to both defect prevention and productivity improvement. The Kusatsu Factory further advances a series of measures to achieve a "ppb level" defect rate in board mounting, which means a "defect rate of 1/1 billion. This is undoubtedly the industry's top-level goal. Although this is no mean feat, Mr. Kunimoto states, "If we can achieve the ppb level, we will be able to provide our customers with knowledge.” The Kusatsu Factory continues to evolve.