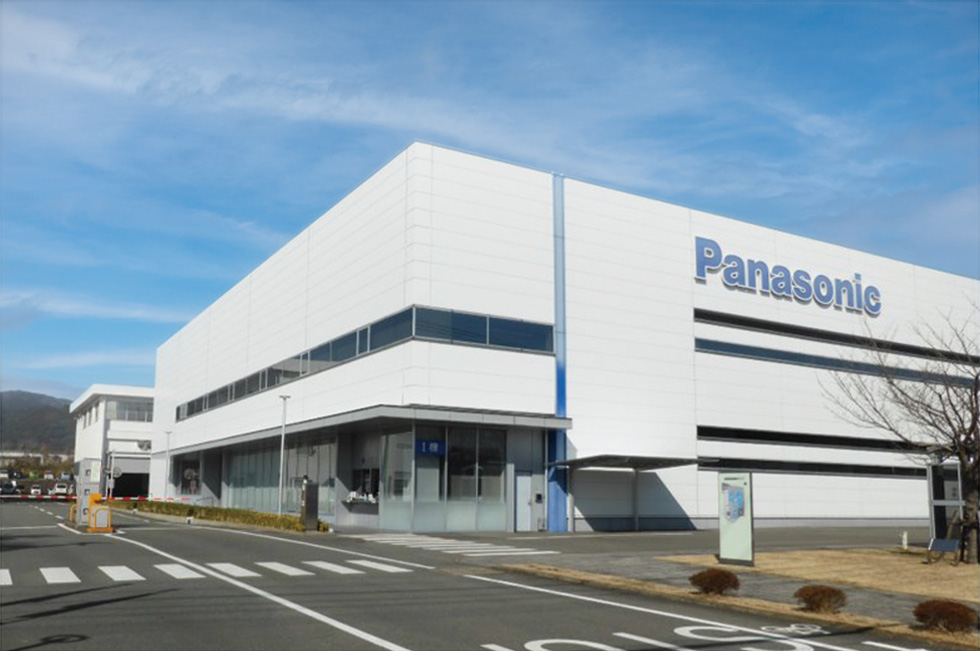
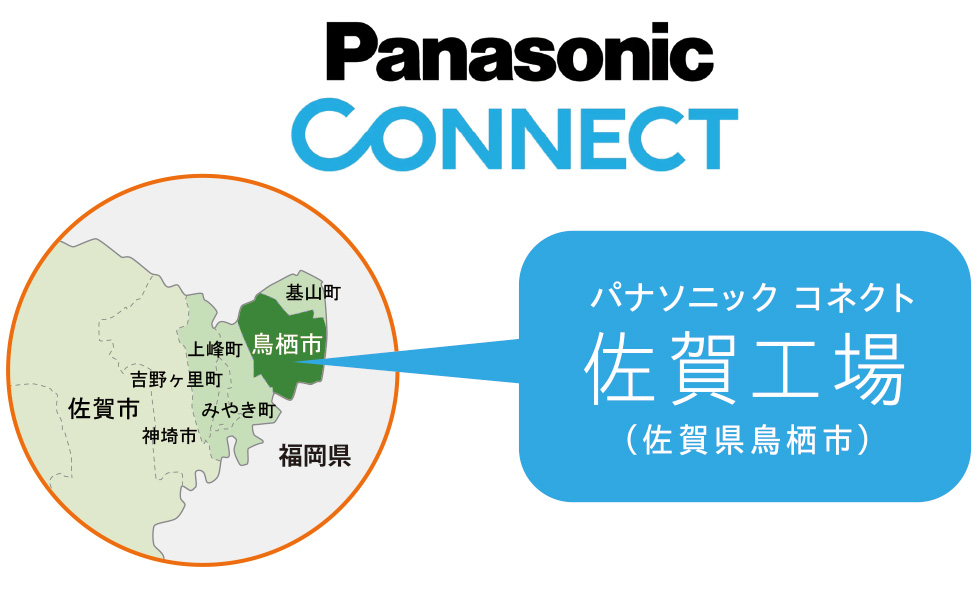
“変種変量生産”を最先端技術で最適化
佐賀県鳥栖市は福岡市にも近く、国道や鉄道の結節点にある交通の要衝。人口は佐賀市、唐津市に次いで同県内3位で、駅前に隣り合うようにサッカー・Jリーグのサガン鳥栖がホームグランドを構える。その鳥栖市に立地する同工場は1964年に操業開始。パナソニック コネクトの直轄工場として約200人が勤務する。80年代以降は全国からさまざまな製品が移管されてきており、主にB to B向けの製品を製造している。同工場の特徴は多種多様な製品を顧客が求める量・リードタイムで生産する〝変種変量生産〟。膨大な製品数を手がける一方、ロットの単位は100台以下が70%を占め、頻繁な機種切り替え作業が発生する。自動化の困難な変種変量の製品を効率良く生産するため、IoT(モノのインターネット)などを駆使して徹底的な現場の見える化やデータ化を推進してきた。近年はサイバー・フィジカル・システム(CPS)の活用を本格化し、モノづくりの革新を進めている。
CPSで生産計画を最適化
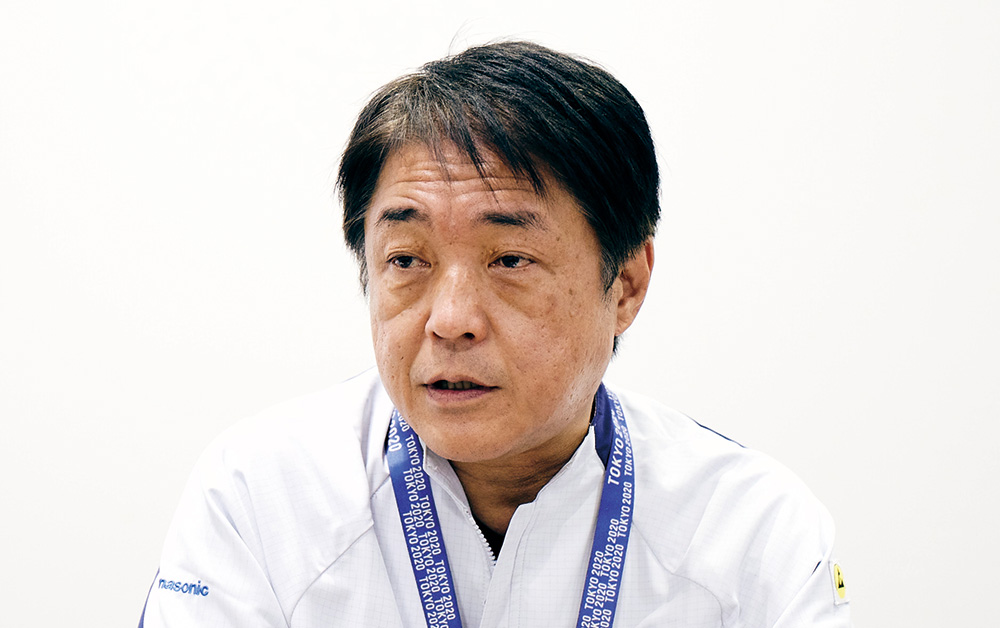
パナソニックコネクト株式会社 佐賀工場 高橋俊也 工場長
「モノづくりを一から見直してきた」。パナソニック コネクト佐賀工場の高橋俊也工場長はそう話す。同工場は膨大な品種を扱い、ユーザーのリードタイムがそれぞれ異なる。製造現場では先を見込んで受注がなくても作り続けようという動きがでるが、これが工程間の非同期を生んで無駄な在庫の発生などにつながる。こうしたさまざまな課題をどう解決するか。納期を含めて全てをまとめることは「人間業ではできないところまできていた」(高橋工場長)という。そこで2018年から在庫起点でモノづくりの見直しに着手。その中でサイバー・フィジカル・システム(CPS)という手段を同工場の特徴にするために「パナソニックグループのテクノロジー本部とも連携して取り組んできた」(企画課の中川愼治氏)。データを使った可視化で生産計画を最適化することを目指している。現在、実装工程から組み立て工程に取り組みが広がってきたところだ。将来は人工知能(AI)を用いた作業の分析やスキルに応じた作業員の配置など、さらなる人の作業のデジタル化を見据える。製造現場のねじ締め作業に、ねじ締めのエラー検出やデータ連携が可能なデジタル変革(DX)に対応したハイオスのデジタルドライバー「熟練工BLG-BC2」を採用したのも、こうした取り組みをにらんだものだ。例えばねじ締め不良を自動で検知し、締め付けごとにデータを取得できる機能や、ねじ締め本数を設定すると残りの本数をカウントダウンで知らせる熟練工のスクリューカウンター機能を使えば不良を出さずに安心して作業できる。 数ある電動ドライバーの中からハイオスを選択した理由について高橋工場長はDXに対応した機能とともに、「ドライバーとして信頼性が高い。これまでも長くハイオスのドライバーを使わせてもらっている」と話す。今後、データ連携機能などさらに活用を進め、モノづくりの進化に役立てる考えだ。
“ねじ締結技術”で製造を次のステージへ
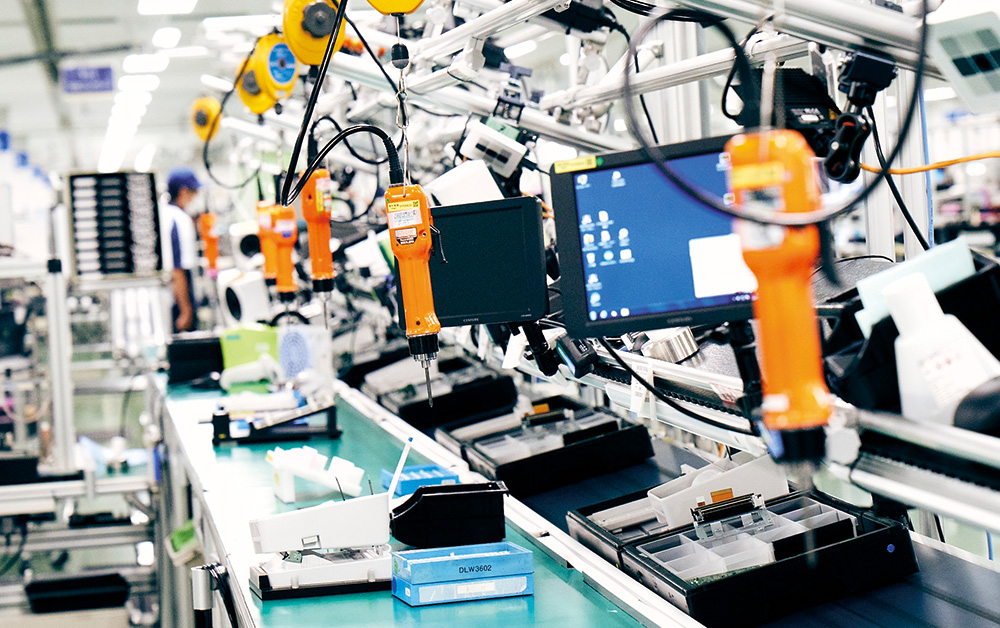
生産ライン 熟練工BLG-BC2
ハイオスは”ねじ”というモノづくりを支える基本の分野で、独創的な技術力と高品質に裏打ちされた製品を供給してきた。同社の戸津勝行社長は「踏み込んでいけば行くほど奥が深い」と話す。ねじとビットとドライバーを三本の矢に例え、「これで一対。これを一つひとつ紐解いていく」とさらに研究開発に力を入れる構えだ。 現在、注力しているのはねじ締めのデジタル化。ねじ締め不良はないか、締め忘れはないか、既定のトルクで締めたか、定量的なデータを残してトレーサビリティ可能にすること。「熟練工BLG-BC2」を採用したパナソニック コネクト佐賀工場が取り組む「見える化」「データ化」と、まさに軌を一にしている。その優秀さが評価され、従来の電機、機械業界などだけでなく、車載関連業界でも採用が広がっている。9月には一般社団法人サステナブル経営推進機構が主催する「第5回エコプロアワード」(後援:財務省、農林水産省、経済産業省、国土交通省、環境省)で「奨励賞」を受賞した。ねじ締め不良を大幅に削減できる「トツプラねじ」「インタトルク」、ブラシレスモーターの採用でカーボンの排出を抑えた「熟練工」など、環境と作業者に優しい一連の製品がサーキュラーエコノミーの実現に貢献すると評価されたためだ。ハイオスは今後もねじ締めの進化に向けて挑戦し続ける。
人を助ける“熟練工”ドライバー

製造技術課 松岡洋輔課長
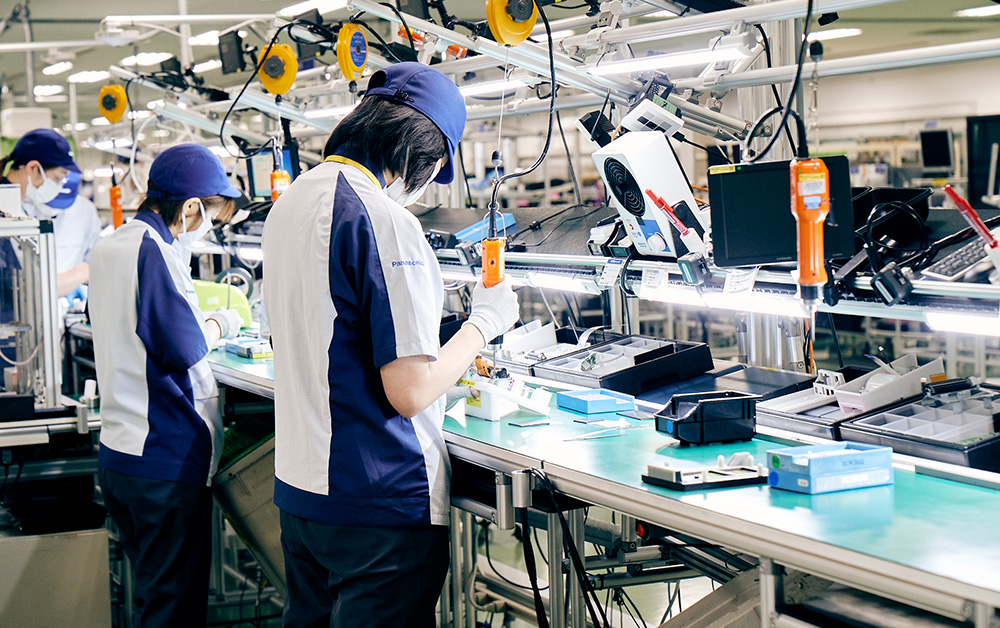
生産ライン
パナソニック コネクト佐賀工場の主力製品である決済端末の生産ライン。かつては機種ごとに複数の専用ラインを引いていたが、製品によって生産量がばらついたり繁閑の差が大きかったりするため、2019年から20年にかけて混流生産のラインを立ち上げた。現在は一つのラインで複数の機種を生産する。そのラインにずらりと並ぶのがハイオスのオレンジ色のデジタルドライバー「熟練工BLG-BC2」。作業中はねじを締めるリズミカルな音が耳に響く。製造技術課の松岡課長は「採用したのは他社製品と比べて機能やコストパフォーマンスに優れているため」と話す。 従来は一日3機種など連続して流れる同ラインを現場のリーダーが管理していたが、切り替えやペース配分を全て管理するのは困難。このため、それぞれのラインに入った作業者や作業の履歴などをデータベース化・共有化して活用する仕組みづくりを進めている。ラインには作業のペース配分をコントロールする送り台やねじの本数を管理する皿など、現場ならではの工夫が各所に施されている。従来は人手に頼っていた検査も、工場の生産技術部によって自動化している。 現場の知恵を集めた生産ラインでハイオスの「熟練工BLG-BC2」を採用したのは「充実した機能で安心して作業ができる」(松岡氏)。同工場では他にも、ハイオスの自動化タイプのドライバーも利用している。「熟練工」の特長は①ねじ締めごとの合否判定(様々なねじ締め不良を検知)②ねじ締め本数をカウント③データをクラウドで一元管理。佐賀工場ではこうした機能を活用し、ゆくゆくはドライバーに関わる情報をデータベース化し、どのような条件で不具合が発生するのかしないのか、データをAIで分析して利活用することを目指している。 日々、改善に取り組む生産ラインだが、まだまだ課題はあるという。例えば製品・工程の切り替え作業時間の短縮は生産性向上に直結するテーマだ。モノづくりにこだわり続ける同工場と、モノづくりを支えるねじ締めにこだわり続けるハイオス。新たなコラボレーションが期待できそうだ。
(日本物流新聞社2022年7月10日号掲載)