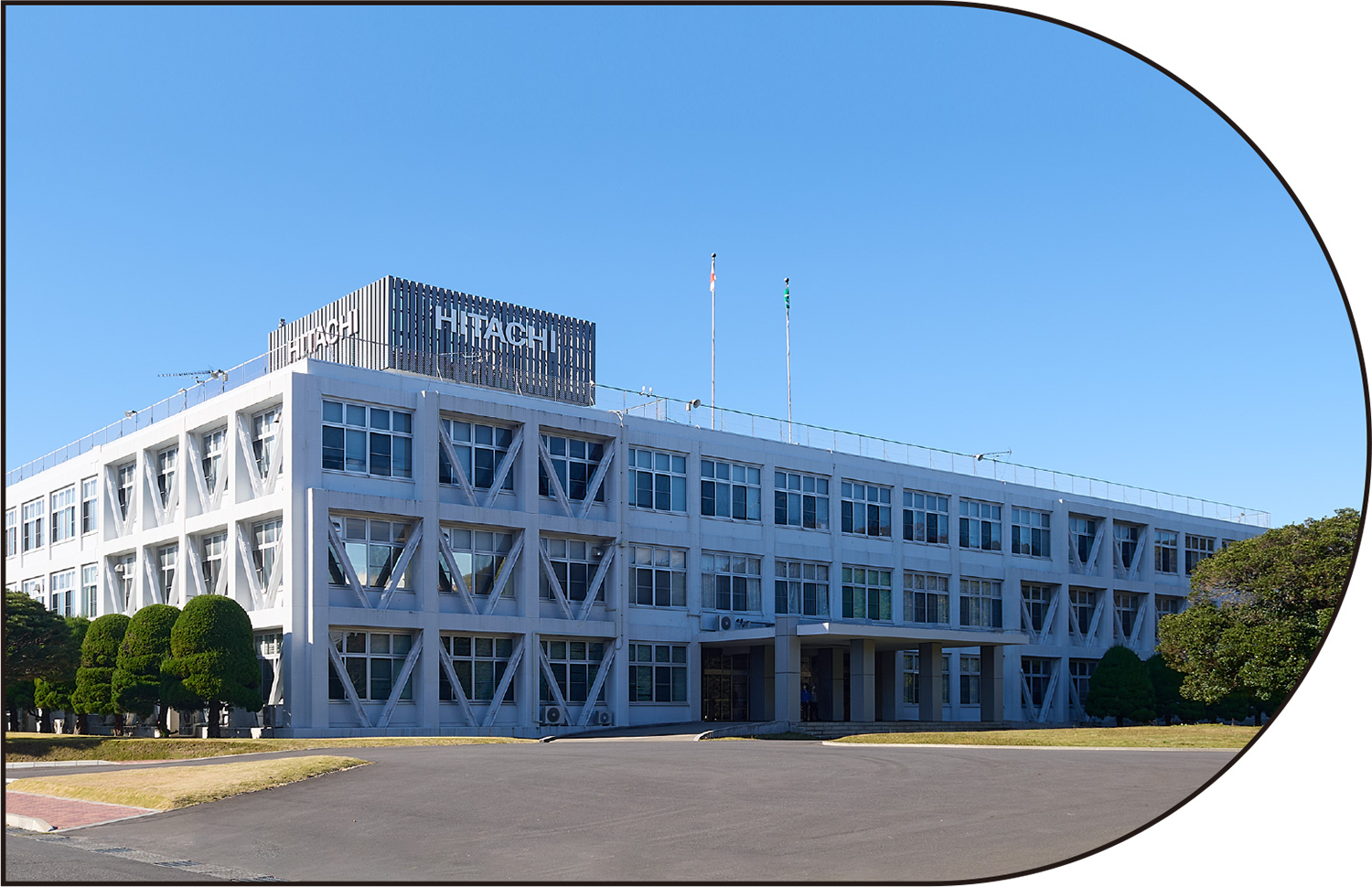
日立グローバルライフソリューションズ×ハイオス
ねじ締め自動化&サステナビリティで挑む
「ジャパンクオリティ」の高品質家電
日本国内における家電生産を牽引してきた日立グローバルライフソリューションズ。その主要製造拠点・多賀事業所では自動化や生産性向上を主眼においたアップデートが行われており、より良い製品作りをより効率的に行うラインが構築されている。そんな製造現場で採用されているのがハイオスの「ねじ締結ソリューション」だ。
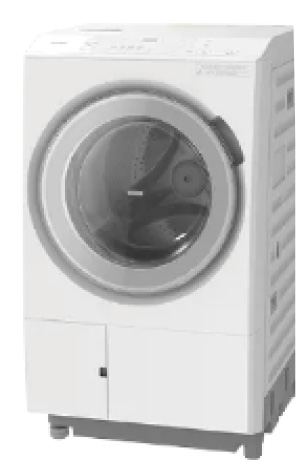
Interview01
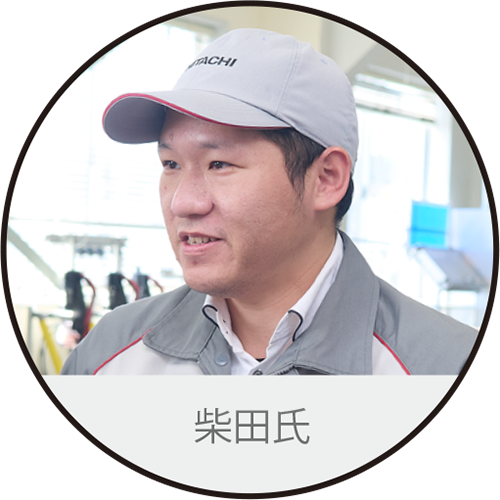
日立グローバルライフソリューションズ(以下、日立GLS)の多賀事業所は、1939年に日立初の電気製品の量産工場として操業をスタート。扇風機の生産を皮切りに掃除機やワープロなど、時代のニーズに合わせた製品を生産してきた。
現在は、洗濯乾燥機、衣類乾燥機、掃除機、炊飯器、IHクッキングヒーターなど白物家電を中心に生産。人々の快適な暮らしを支えている。
東京ドーム10個分という広大な敷地には、同社家電製品の中核を成す生活家電本部が置かれており、生産技術部、製造部や生産管理部などモノづくりに関わるリソースが集約されている。
かつては隆盛を誇った国内家電メーカー。だが、コモディティ化の進展とともに、多くの企業が撤退や廃業、事業規模の縮小を余儀なくされていった。しかし、日立GLSは冷蔵庫、洗濯機、掃除機などにおいて高いシェアを堅持。付加価値の高い「ジャパンクオリティ」の家電を世に送り出している。その競争力の源泉は、80年以上に渡る家電生産におけるノウハウと、たゆまぬ生産技術の革新にある。
そんな同社のモノづくりを「ねじ一本」から下支えしているのが、産業用電動ドライバーのパイオニアメーカー・ハイオスだ。同社は1970年の創業以来、ねじ締結における専業メーカーとして、自動車産業から精密機器まで数多くのメーカーに最適なねじ締めソリューションを提供してきた。
多賀事業所において洗濯機、掃除機、掃除ロボットを手掛ける製造部がハイオスのドライバーをはじめて導入したのは2015年のこと。導入に至った経緯を第一製造部の柴田慧技師が述懐する。
「製造工程におけるねじ締め不良やねじ締め忘れを改善できないかと思い、様々なメーカーの電動ドライバーを比較検討しました。その中で、同じトルク帯の製品でも機能的にダントツで優れていたのが、当時発売してまもないハイオスさんのBLG(熟練工シリーズ)でした。ねじ締めエラーを高精度に検知できるほか、本数管理も簡単に出来るので、これならと思い導入を決めました」
現在は、洗濯乾燥機、衣類乾燥機、掃除機、炊飯器、IHクッキングヒーターなど白物家電を中心に生産。人々の快適な暮らしを支えている。
東京ドーム10個分という広大な敷地には、同社家電製品の中核を成す生活家電本部が置かれており、生産技術部、製造部や生産管理部などモノづくりに関わるリソースが集約されている。
かつては隆盛を誇った国内家電メーカー。だが、コモディティ化の進展とともに、多くの企業が撤退や廃業、事業規模の縮小を余儀なくされていった。しかし、日立GLSは冷蔵庫、洗濯機、掃除機などにおいて高いシェアを堅持。付加価値の高い「ジャパンクオリティ」の家電を世に送り出している。その競争力の源泉は、80年以上に渡る家電生産におけるノウハウと、たゆまぬ生産技術の革新にある。
そんな同社のモノづくりを「ねじ一本」から下支えしているのが、産業用電動ドライバーのパイオニアメーカー・ハイオスだ。同社は1970年の創業以来、ねじ締結における専業メーカーとして、自動車産業から精密機器まで数多くのメーカーに最適なねじ締めソリューションを提供してきた。
多賀事業所において洗濯機、掃除機、掃除ロボットを手掛ける製造部がハイオスのドライバーをはじめて導入したのは2015年のこと。導入に至った経緯を第一製造部の柴田慧技師が述懐する。
「製造工程におけるねじ締め不良やねじ締め忘れを改善できないかと思い、様々なメーカーの電動ドライバーを比較検討しました。その中で、同じトルク帯の製品でも機能的にダントツで優れていたのが、当時発売してまもないハイオスさんのBLG(熟練工シリーズ)でした。ねじ締めエラーを高精度に検知できるほか、本数管理も簡単に出来るので、これならと思い導入を決めました」
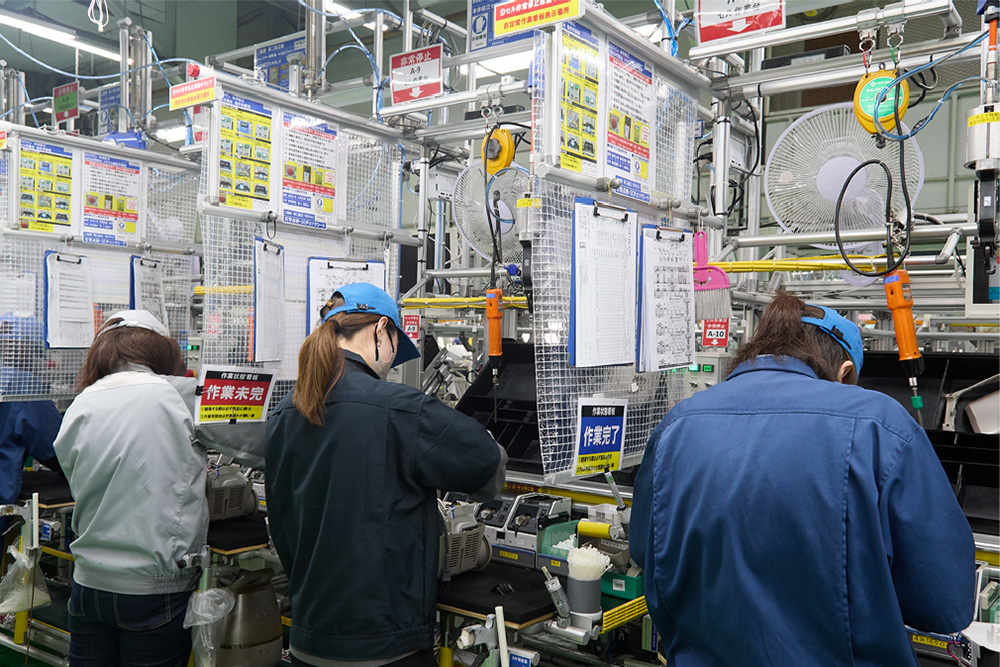
生産ラインの写真=トルク管理や本数管理が簡単に可能
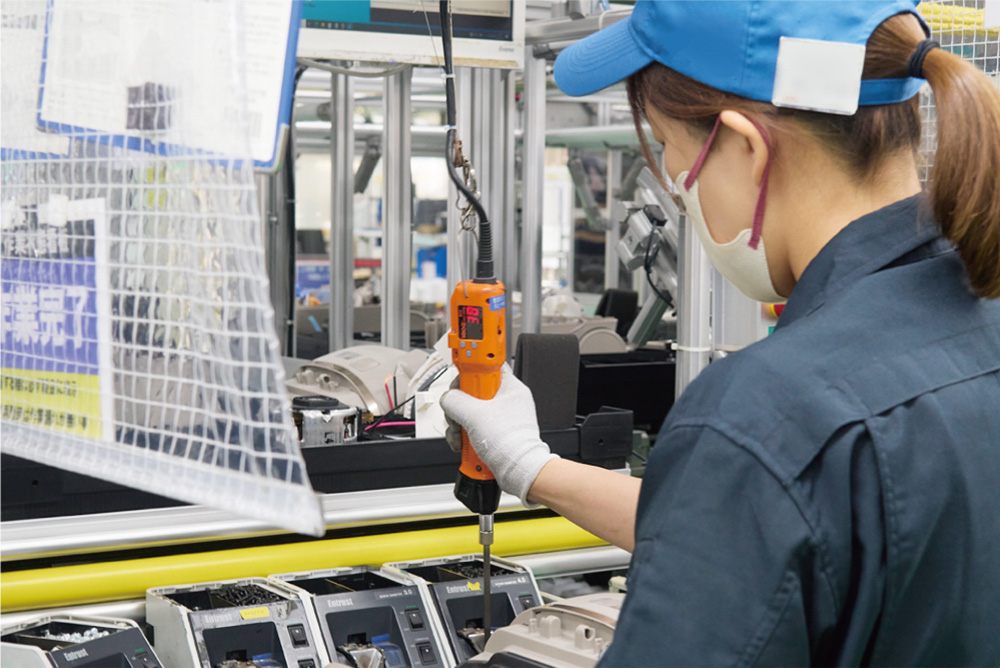
ねじ締め不良改善を目指しハイオス製ドライバーを導入
ミス激減、作業者負担を軽減。
Interview02
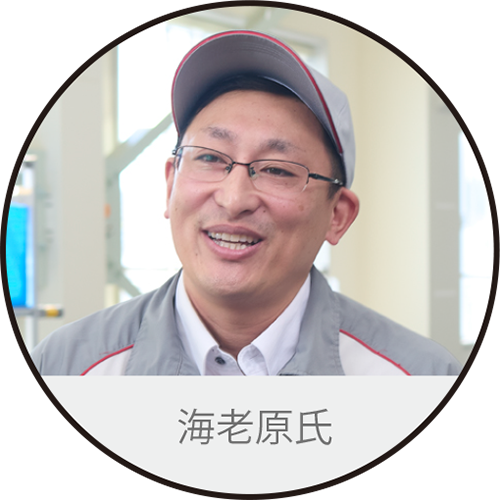
かくして実際の製造現場に投入されたハイオス「熟練工」シリーズ。その導入効果を第一製造部の海老原大輔主任が話す。
「規定の締付トルク値で適正な締付回転数によって員数管理ができるので、ねじ1本1本の締付品質が向上しましたね。ねじ浮きやカムアウトといった不良もリアルタイムで検出してくれるので、安定した品質を維持することができています。また締結完了の信号をドライバーからシリアル通信で生産ラインに接続できるので、“作業が完了していないと次工程に送れない”といったシステム構築の重要なツールとしても活用しています」
作業者にとって日々扱う電動ドライバーは、手の延長のようなものであり、使いやすさもキーポイントになる。
「作業者からは従来品より熟練工のほうが使いやすい、という意見が大半です。他社の電動ドライバーはグリップ部分が太く真円形状なのですが、熟練工は細身かつ楕円形状なので、すごく握りやすいと女性の作業者さんに好評です。また本体重量も軽いんですよ。他社製品は700㌘くらいありますが、熟練工は400㌘ちょっと。肉体的な負担もかなり軽減されたという声も上がっています。また、アタッチメントの滑り止めはカラーバリエーションが豊富で、異なるトルクで複数本の熟練工を使っている現場ではこちらを活用させて頂いています。赤の滑り止めはトルク設定1N・m、緑は0.7N・mというように識別でき、非常に便利です」(海老原氏)
「規定の締付トルク値で適正な締付回転数によって員数管理ができるので、ねじ1本1本の締付品質が向上しましたね。ねじ浮きやカムアウトといった不良もリアルタイムで検出してくれるので、安定した品質を維持することができています。また締結完了の信号をドライバーからシリアル通信で生産ラインに接続できるので、“作業が完了していないと次工程に送れない”といったシステム構築の重要なツールとしても活用しています」
作業者にとって日々扱う電動ドライバーは、手の延長のようなものであり、使いやすさもキーポイントになる。
「作業者からは従来品より熟練工のほうが使いやすい、という意見が大半です。他社の電動ドライバーはグリップ部分が太く真円形状なのですが、熟練工は細身かつ楕円形状なので、すごく握りやすいと女性の作業者さんに好評です。また本体重量も軽いんですよ。他社製品は700㌘くらいありますが、熟練工は400㌘ちょっと。肉体的な負担もかなり軽減されたという声も上がっています。また、アタッチメントの滑り止めはカラーバリエーションが豊富で、異なるトルクで複数本の熟練工を使っている現場ではこちらを活用させて頂いています。赤の滑り止めはトルク設定1N・m、緑は0.7N・mというように識別でき、非常に便利です」(海老原氏)
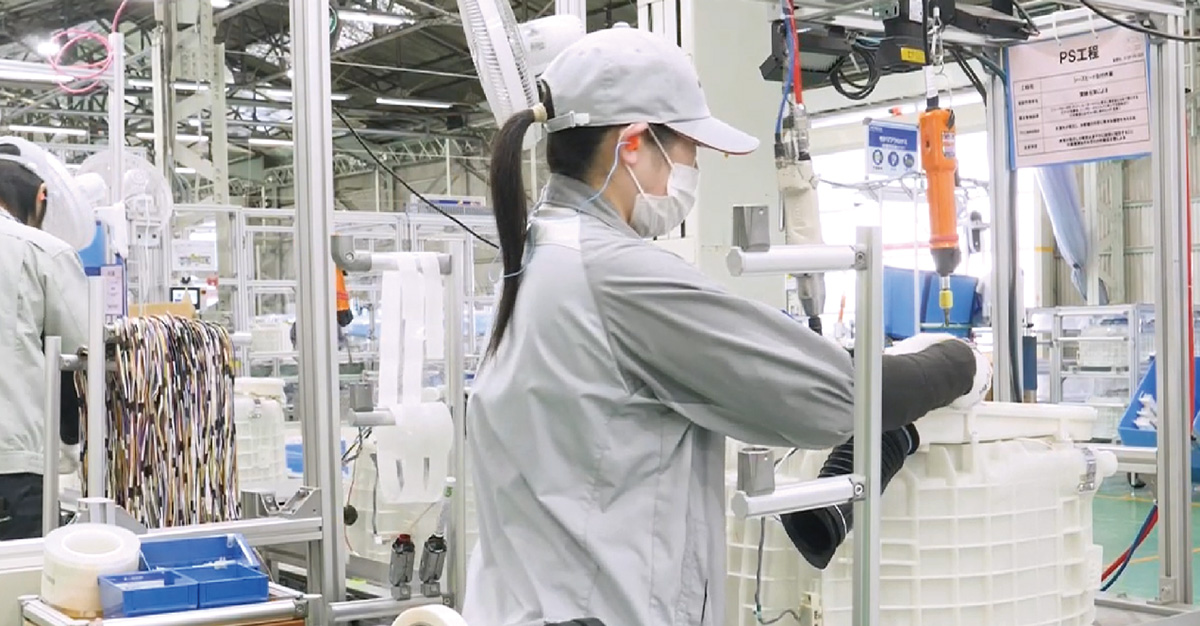
女性でも握りやすく作業負荷を軽減する
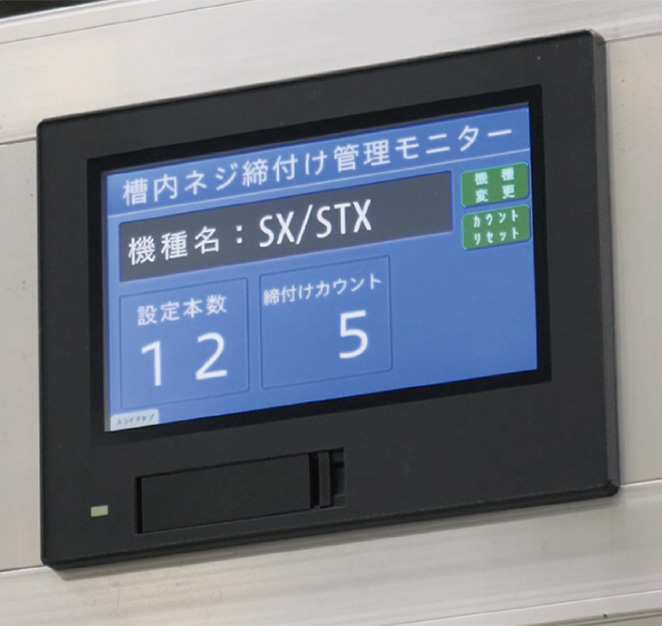
締結本数はモニタ管理でミスを低減
インタトルク&トツプラねじラインを止めない自動化を実現
Interview03
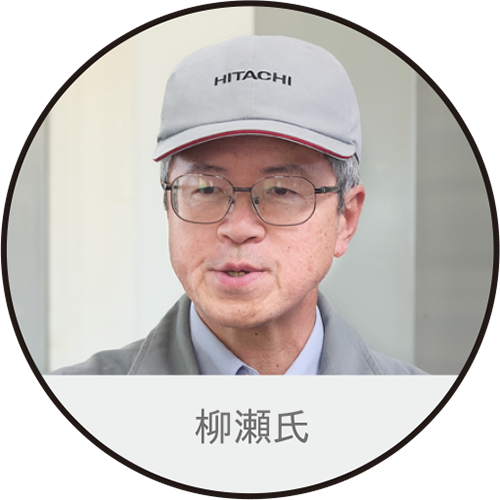
人手を介した高品質のモノづくりに、電動ドライバー「熟練工」が活用される一方で、自動化ラインにおいてもハイオスの「ねじ締めソリューション」が採用されている。ハイオスは電動ドライバーメーカーでありながら、「ねじ締め専業メーカー」でもある。自らを「ねじバカおやじ」と称する戸津勝行社長が創業当時に開発した「トツねじ」は、マイナスねじに窪みを付け、ビットとねじの嵌合性能を飛躍的に高めたねじ。
現在この技術を生かし、プラスねじに窪みを付けた「トツプラねじ」や、星型ねじ(ヘクサロビュラ)に窪みを加えた「インタトルク」を展開しており、これらは多賀事業所第一製造部の自動化ラインで採用されている。
多賀事業所の自動化ライン構築に尽力した第一製造部の柳瀬誠治氏が語る。
「製造ラインにおいて自動化したかった箇所は、横方向へのねじ締めでした。ねじ締め自動化は、タテ方向は比較的やりやすいのですが、横方向となると難易度がグッと上がります。通常のねじと自動機用ドライバーでは、ひんぱんにチョコ停が起こってしまう。それがインタトルクを試験的に使ってみたところ、トラブルが激減しました」だが、ここでのインタトルク採用は見送られる。その理由を柳瀬氏が話す。
「インタトルクの性能はびっくりするくらい良かったのですが、製品販売後のメンテナンスを考えた時に少し躊躇してしまう部分がありました。当社の家電はお客様に長くお使い頂くために、日本中にアフターサービス体制を敷いているのですが、そのサービスマン全てにインタトルク専用の工具を行き渡らせるとなると難しい。そこでトツプラねじを試験してみたところ、インタトルクと遜色ない結果が出ましたので、そちらを採用させて頂きました。トツプラねじでしたらメンテナンスは普通のプラスドライバーでもできますから」
トツプラねじを採用した製造ラインは導入から3年あまり、ほぼトラブル無しで現在に至っているという。さらに掃除機のモーター部分のねじ締め自動化においては、インタトルクに白羽の矢が立った。
「自動化する前は手作業で普通のプラスねじを使っていましたが、小径のねじですので、手作業中にねじが倒れたり、カムアウトして十分なトルクがかからないなどの問題が頻繁に起こっていました。そこを自動化するタイミングでインタトルクを採用させて頂きましたが、やっぱりカムアウトしないし、直進性に優れているのでねじの座りが抜群に良く、狙ったところを外さない。加えて、締めたあとに食いつかずにしっかり離れてくれるので、トラブルが全く起こらない。ビットとねじの形状が変わるだけで、これほど大きな差が生まれるのか、と感心しました」
インタトルクは特殊形状のねじであり、馴染みのない現場も少なくないだろう。そこでハイオスは近年、新たに「インタトルクマイナス」を開発。こちらはインタトルクの星型形状にマイナス溝を追加した設計により、既存の嵌合性能を維持しつつ、マイナスドライバーでも使用可能。自動化に最適な「締めやすく外しやすいねじ」として、メンテナンス、サービスの現場はもちろん、幅広い現場での活用が期待されている。
ドライバーだけではない「ねじ」へのこだわりが、難易度の高いねじ締め工程における「ラインを止めない自動化」を実現している。
現在この技術を生かし、プラスねじに窪みを付けた「トツプラねじ」や、星型ねじ(ヘクサロビュラ)に窪みを加えた「インタトルク」を展開しており、これらは多賀事業所第一製造部の自動化ラインで採用されている。
多賀事業所の自動化ライン構築に尽力した第一製造部の柳瀬誠治氏が語る。
「製造ラインにおいて自動化したかった箇所は、横方向へのねじ締めでした。ねじ締め自動化は、タテ方向は比較的やりやすいのですが、横方向となると難易度がグッと上がります。通常のねじと自動機用ドライバーでは、ひんぱんにチョコ停が起こってしまう。それがインタトルクを試験的に使ってみたところ、トラブルが激減しました」だが、ここでのインタトルク採用は見送られる。その理由を柳瀬氏が話す。
「インタトルクの性能はびっくりするくらい良かったのですが、製品販売後のメンテナンスを考えた時に少し躊躇してしまう部分がありました。当社の家電はお客様に長くお使い頂くために、日本中にアフターサービス体制を敷いているのですが、そのサービスマン全てにインタトルク専用の工具を行き渡らせるとなると難しい。そこでトツプラねじを試験してみたところ、インタトルクと遜色ない結果が出ましたので、そちらを採用させて頂きました。トツプラねじでしたらメンテナンスは普通のプラスドライバーでもできますから」
トツプラねじを採用した製造ラインは導入から3年あまり、ほぼトラブル無しで現在に至っているという。さらに掃除機のモーター部分のねじ締め自動化においては、インタトルクに白羽の矢が立った。
「自動化する前は手作業で普通のプラスねじを使っていましたが、小径のねじですので、手作業中にねじが倒れたり、カムアウトして十分なトルクがかからないなどの問題が頻繁に起こっていました。そこを自動化するタイミングでインタトルクを採用させて頂きましたが、やっぱりカムアウトしないし、直進性に優れているのでねじの座りが抜群に良く、狙ったところを外さない。加えて、締めたあとに食いつかずにしっかり離れてくれるので、トラブルが全く起こらない。ビットとねじの形状が変わるだけで、これほど大きな差が生まれるのか、と感心しました」
インタトルクは特殊形状のねじであり、馴染みのない現場も少なくないだろう。そこでハイオスは近年、新たに「インタトルクマイナス」を開発。こちらはインタトルクの星型形状にマイナス溝を追加した設計により、既存の嵌合性能を維持しつつ、マイナスドライバーでも使用可能。自動化に最適な「締めやすく外しやすいねじ」として、メンテナンス、サービスの現場はもちろん、幅広い現場での活用が期待されている。
ドライバーだけではない「ねじ」へのこだわりが、難易度の高いねじ締め工程における「ラインを止めない自動化」を実現している。

自動化に最適な「インタトルク」を採用
家電メーカーとねじ専業メーカーによるサーキュラーエコノミー
Interview04
ハイオスのねじ締めソリューションは、安定した締結や自動化移行だけに留まらない。昨今、製造業に求められている環境配慮においても大きな役割を果たす。
ねじ締めトラブルによる製造ラインの停止や歩留まり率低下は、生産性及びエネルギーの有効活用において大きなマイナスとなる。この点において、ハイオスのねじ締めソリューションは大きな強みを持つ。そもそものねじ締めトラブルが激減するだけではなく、ねじを締める上で必要なドライバービットの消耗も、他のドライバーと比べて格段に少ない。
「トツプラねじ、インタトルク向けビットの組み合わせだと接触面積が大きく、締付時にビットにかかる応力を分散してくれるのが特徴で、金属疲労によるビットの交換頻度が低減しましたし、安定した締付で信頼性が向上しました」(海老原氏)
他社のドライバー、通常のねじではこうはいかない。他の製造現場でも従来使用していた十字ねじ、十字ビットからトツプラねじとハイオス製の十字ビットへの置換により、ビット交換の頻度が10分の1以下に低減した事例もある。
また、製造した製品の修理やリファービッシュ、リサイクルの際には「解体・分解のしやすさ」が極めて重要な要素となる。この点において、「締めやすく、外しやすいねじ」であるハイオスのインタトルク、トツプラねじは、資源循環型のモノづくりに最も適しているねじと言えよう。
バリューチェーンにおける脱炭素化をはじめ、再生可能エネルギーや再生プラスチックの活用など、サステナブルなモノづくり推進している日立GLS。創業以来、環境と安全に配慮した製品開発に取り組み、自社ビルのBELS取得などカーボンオフセットにも真摯に向き合ってきたハイオス。
両社の「ねじへのこだわり」が地球に優しいモノづくりを牽引する。
ねじ締めトラブルによる製造ラインの停止や歩留まり率低下は、生産性及びエネルギーの有効活用において大きなマイナスとなる。この点において、ハイオスのねじ締めソリューションは大きな強みを持つ。そもそものねじ締めトラブルが激減するだけではなく、ねじを締める上で必要なドライバービットの消耗も、他のドライバーと比べて格段に少ない。
「トツプラねじ、インタトルク向けビットの組み合わせだと接触面積が大きく、締付時にビットにかかる応力を分散してくれるのが特徴で、金属疲労によるビットの交換頻度が低減しましたし、安定した締付で信頼性が向上しました」(海老原氏)
他社のドライバー、通常のねじではこうはいかない。他の製造現場でも従来使用していた十字ねじ、十字ビットからトツプラねじとハイオス製の十字ビットへの置換により、ビット交換の頻度が10分の1以下に低減した事例もある。
また、製造した製品の修理やリファービッシュ、リサイクルの際には「解体・分解のしやすさ」が極めて重要な要素となる。この点において、「締めやすく、外しやすいねじ」であるハイオスのインタトルク、トツプラねじは、資源循環型のモノづくりに最も適しているねじと言えよう。
バリューチェーンにおける脱炭素化をはじめ、再生可能エネルギーや再生プラスチックの活用など、サステナブルなモノづくり推進している日立GLS。創業以来、環境と安全に配慮した製品開発に取り組み、自社ビルのBELS取得などカーボンオフセットにも真摯に向き合ってきたハイオス。
両社の「ねじへのこだわり」が地球に優しいモノづくりを牽引する。
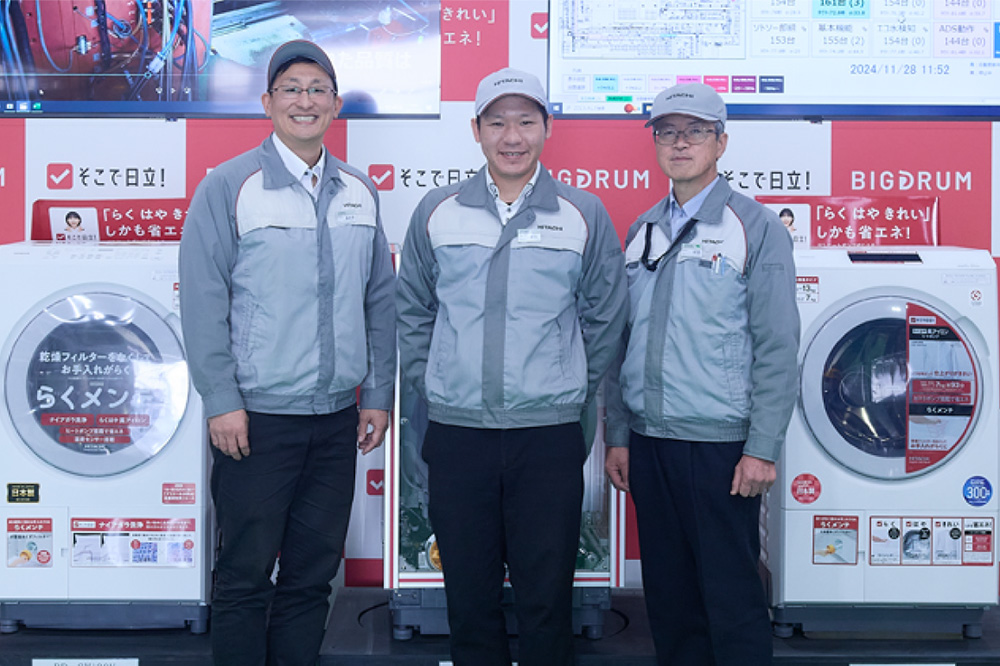
写真左から海老原氏、柴田氏、柳瀬氏