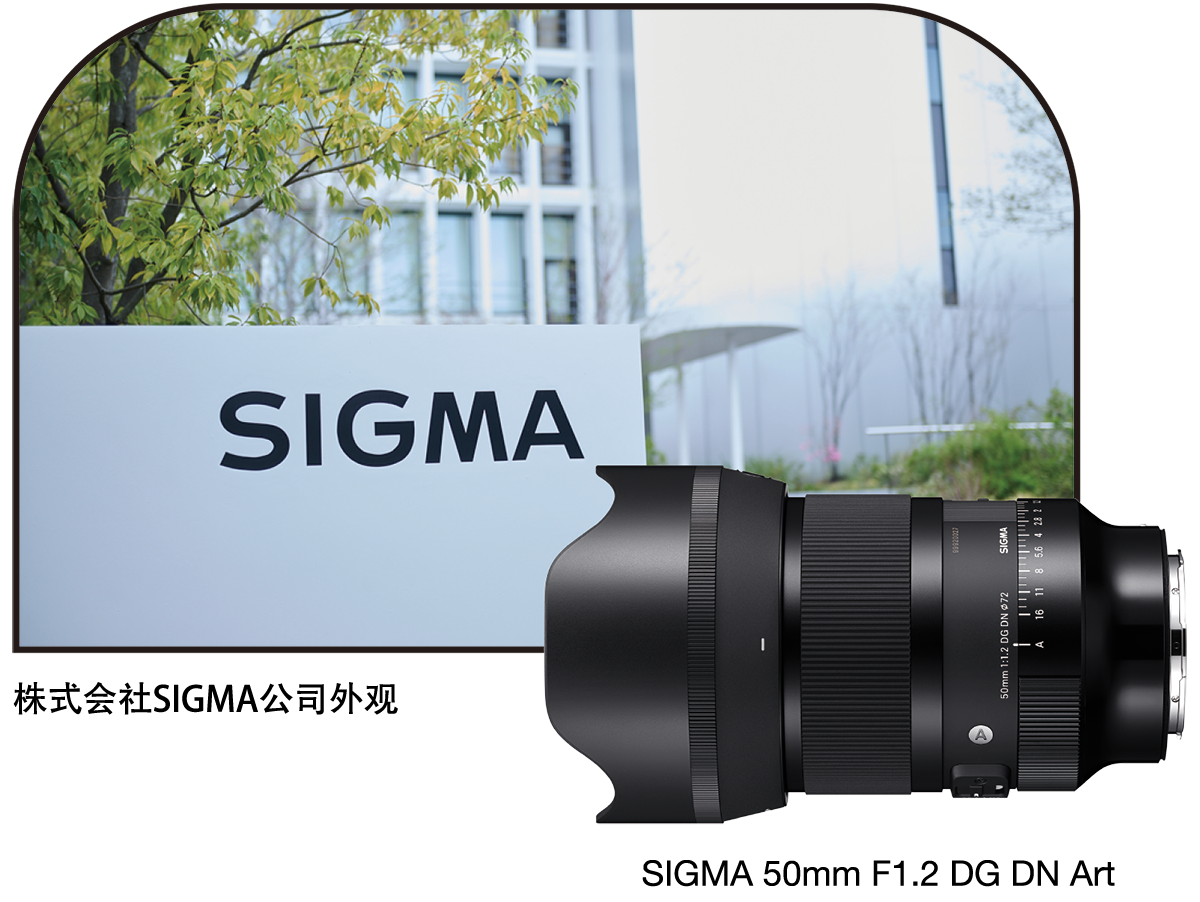
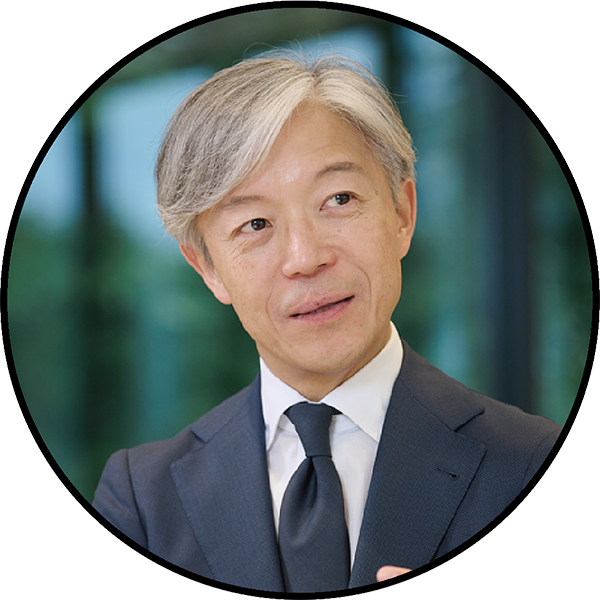
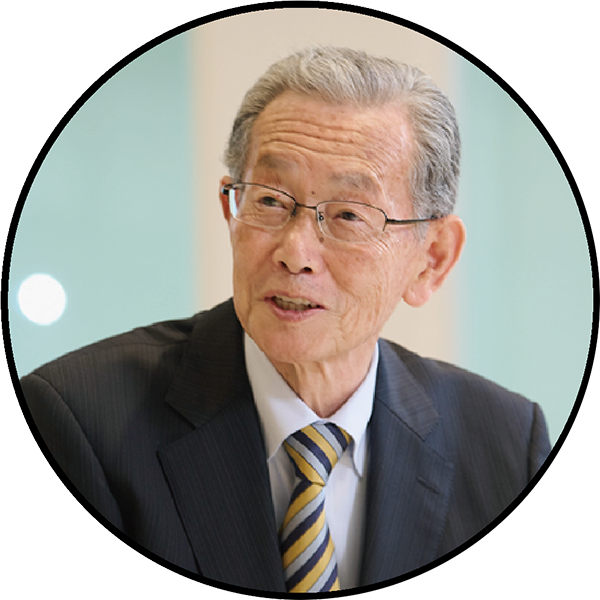
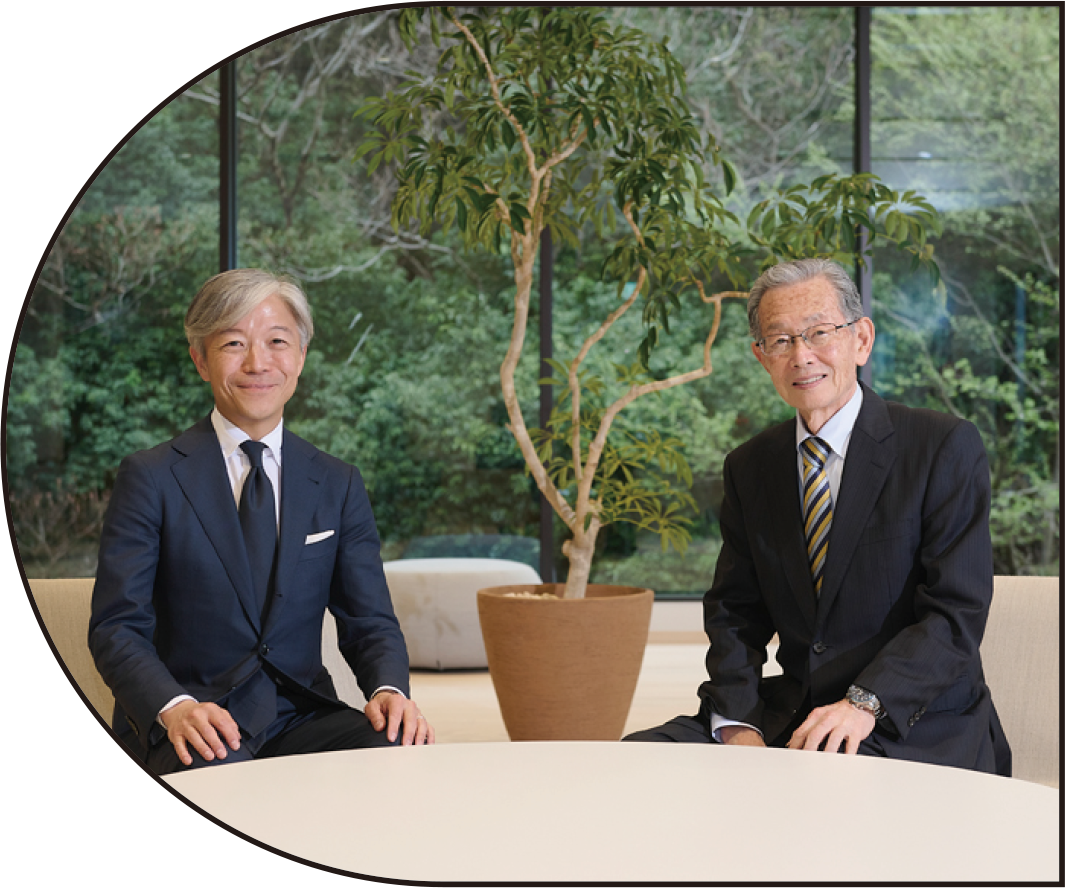
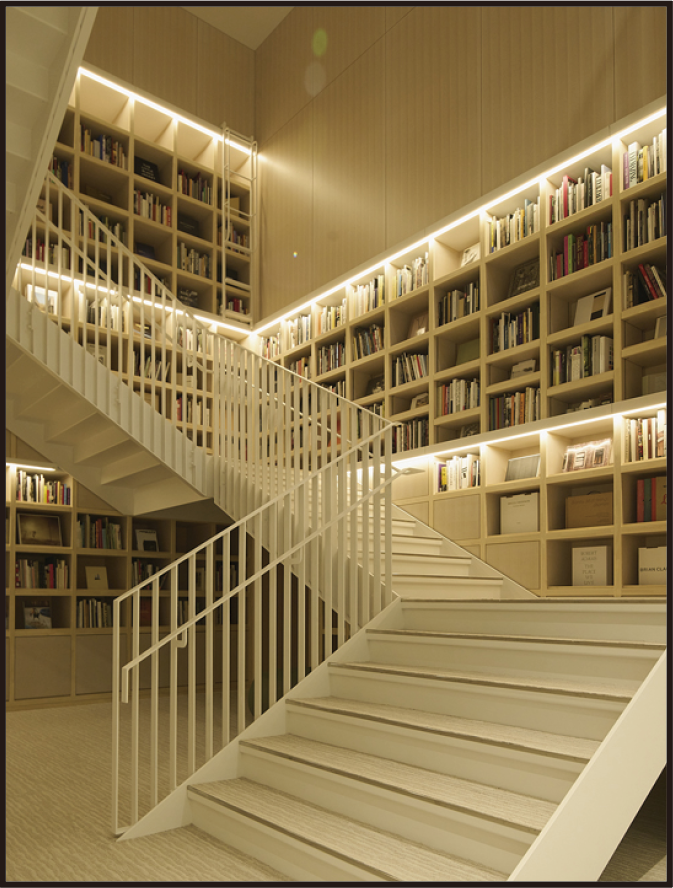
致力于压倒性品质的产品
户津:与大型相机制造商不同,SIGMA开发了很多突破性产品。这背后有什么样的目标和想法呢?
山木:想买相机的时候,首先想到的是佳能、尼康、索尼等国内厂商的产品。这样的话,镜头自然会匹配到同一厂家的东西上。然而我们公司作为交换镜头制造商,想要必须选择我们公司的产品,也就要必须研发出能获好评的具有压倒性的尖端性能、品质的产品。 HIOS也不断开发出具有高竞争力的产品给到市场。贵公司的很多电动螺丝刀我司的工厂也在采用。
户津:感谢。HIOS是1970年,在螺丝槽还是广泛使用一字螺丝的时代设立的公司。一字螺丝使用不方便,大约在此前3年,我们就考量了改良槽的中心部,开发可以稳定作业的 “户津螺丝”。为了将此推广到市场就创立了公司,从那以后经过半个世纪,作为专门的螺丝和螺丝紧固的专业制造商一步步发展过来。山木社长是怎样去致力于制造的呢?
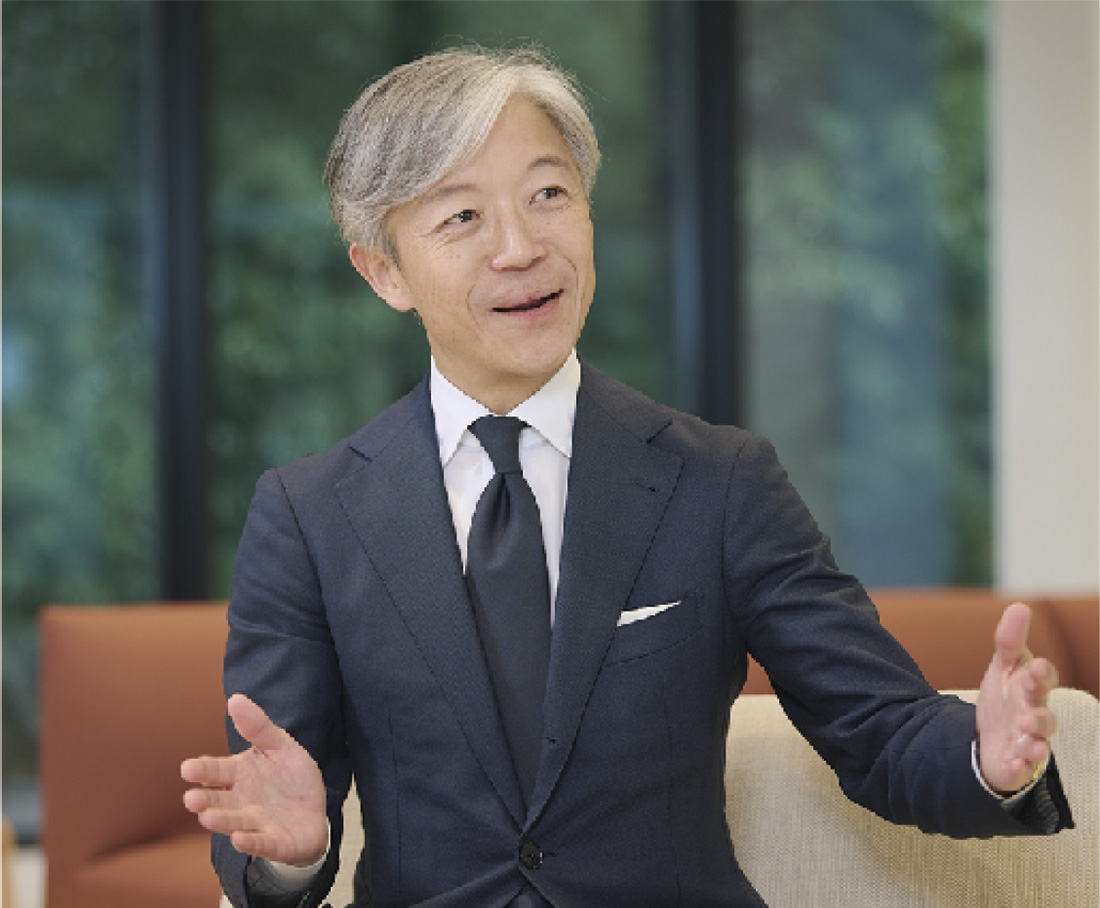
山木:SIGMA的产品并不是从市场研究开始的。开端是“想创造自己发自内心想要的产品、值得骄傲的产品”。不管能不能卖出去,而是自己能不能引以为傲。始终诚实地面对是我们的做事方法。为了贯彻这个做事方法,我们不会上市。户津社长是怎么想的呢?
热情是创新的动力
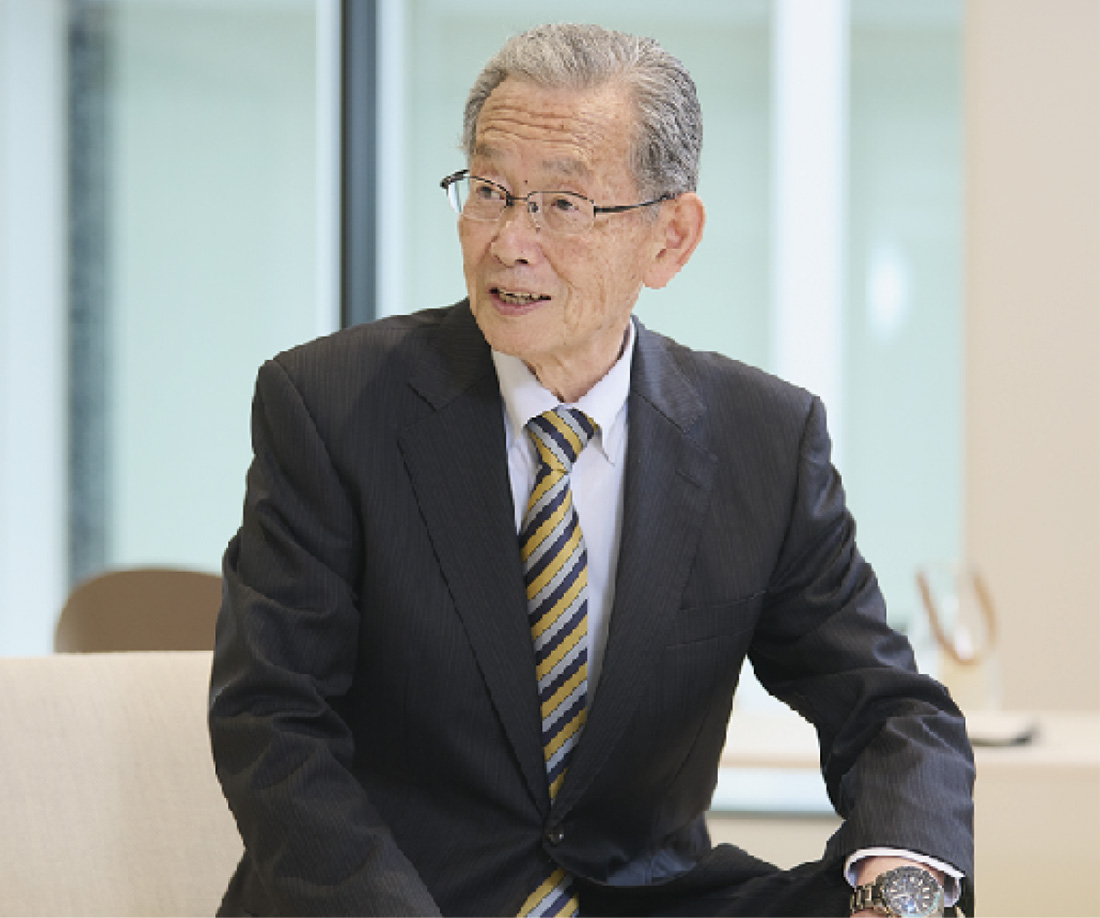
户津:螺丝和螺丝紧固看起来很简单,实际上是各种各样的要素综合在一起的深奥的事情。螺丝和螺丝紧固的合理化,对产品的安全性以及工作人员的作业简便性都有很大的影响。思考螺丝的创新就会发现新的事物,继而发现看不见新事物。我们从容易被忽视的紧固领域发起创新,不断地进行研究,到目前为止专利等知识产权申请了2000件左右。我们的想法是:我们不想模仿,也不想被模仿。听说在实际的生产中,SIGMA的产品全数是在国内生产的。
山木:镜头和相机84款机型全都是在福岛县磐梯町的会津工厂生产的。目前在日元接二连三的贬值和雷曼事件引起的不景气情况下要保住就业岗位。还要生产出附加价值高的产品且追求国内生产。现在不仅是镜头加工,注塑成型、镁加工、涂装、基板安装、产品组装、模具和微小金属零件的加工也几乎达到了自己能完成的最高水平。
户津:听闻组装现场使用了我司的电动螺丝刀。
山木:要使光轴符合设计要求,交换镜头必须正确组装。有听到反馈,贵公司的电动螺丝刀能稳定地拧紧小而精密的螺丝,是生产现场很多女性工作者希望的那种不仅是小型、轻巧,操作也简单的螺丝刀。HIOS今后的产品开发是怎样的方向呢?
以世界称赞的品牌为目标
户津:大主题是螺丝紧固的自动化和保护环境两个方面。机器人的螺丝拧装自动化的潮流日益变化,追求用更小的机器人的拧装技术、高精度化、高耐久性等。另一方面,针对世界关注的环境问题作出的对策,致力于开发容易降解的适应性高的螺丝。那么,山木社长想把SIGMA做成什么样的公司呢?
山木:在为影像和摄影文化的发展做出贡献的同时,也希望成为世界上光学技术最高的公司。20世纪德国制造商处最高地位。21世纪光学技术的发展,我是想SIGMA将其作为原动力。
户津:我认为螺丝和螺丝紧固其实是可以改变很多领域的。为让HIOS的姿态在世界上得到认可,本公司也会继续努力的。今天感谢交流。
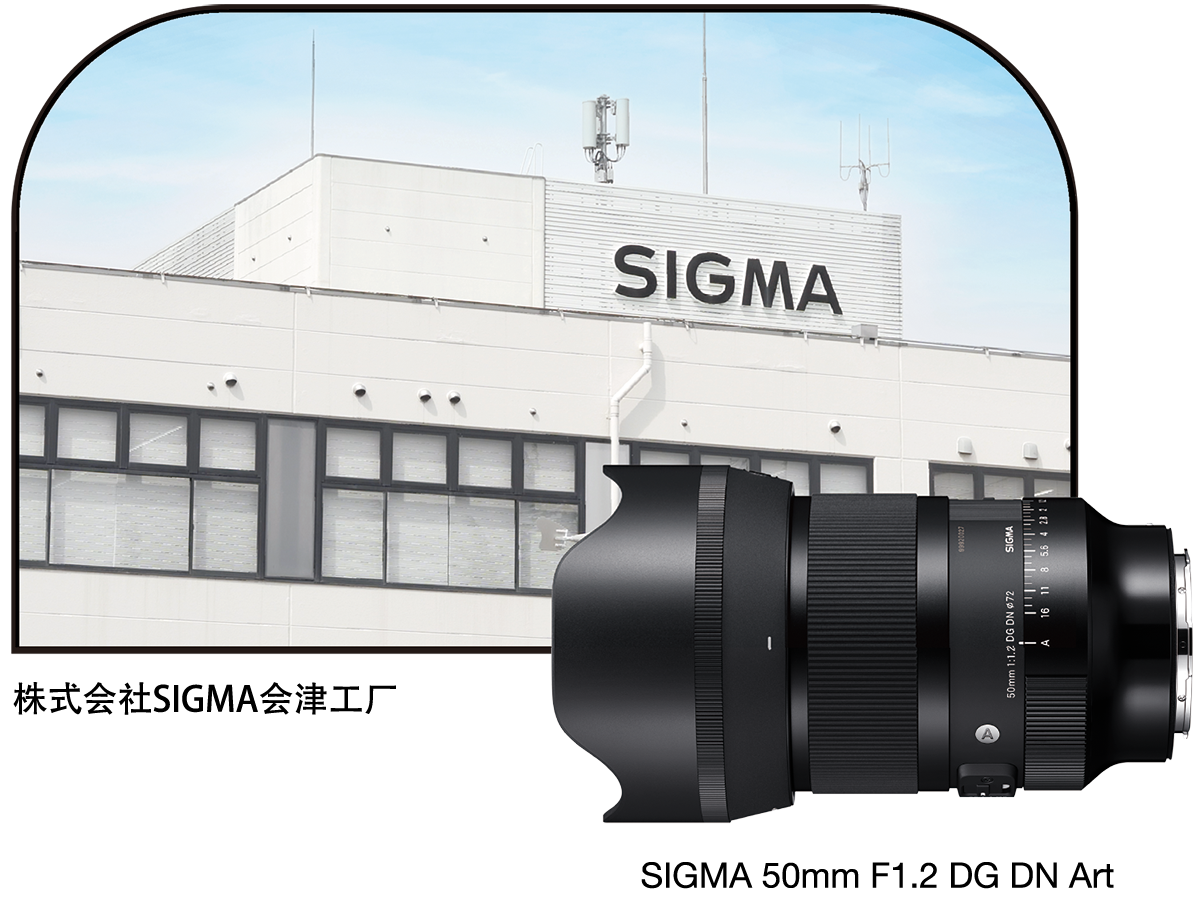
组装现场的绝对信赖
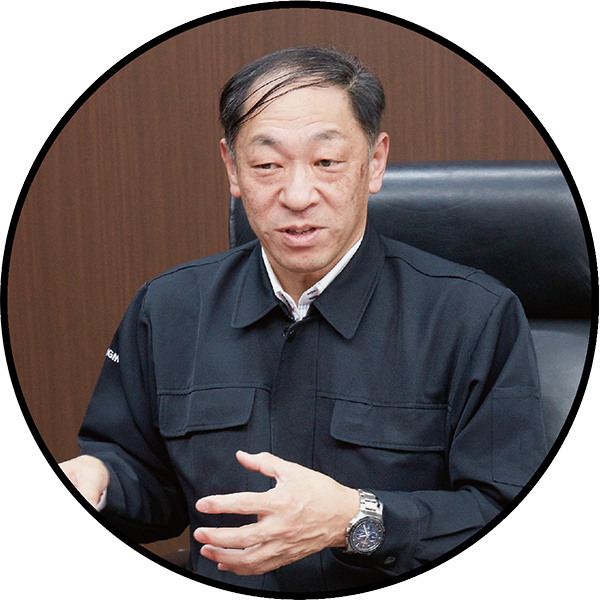
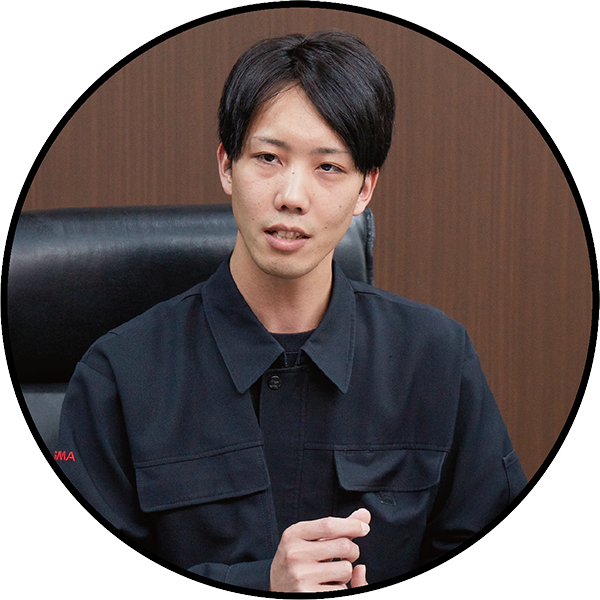
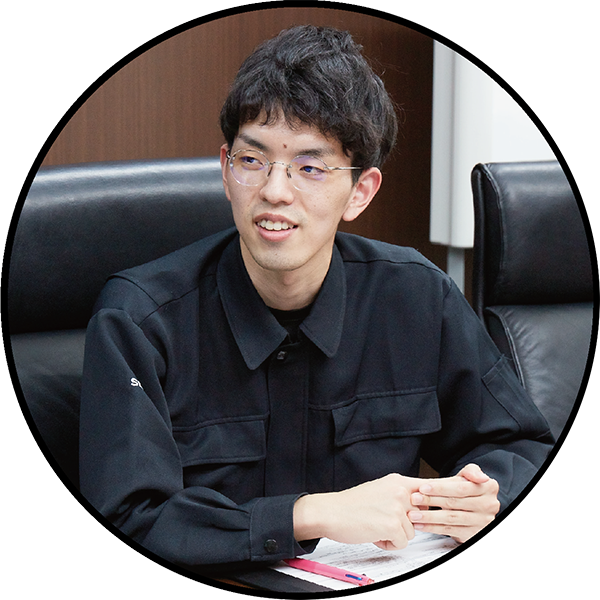
无碳刷电动螺丝刀支持每月7万生产量
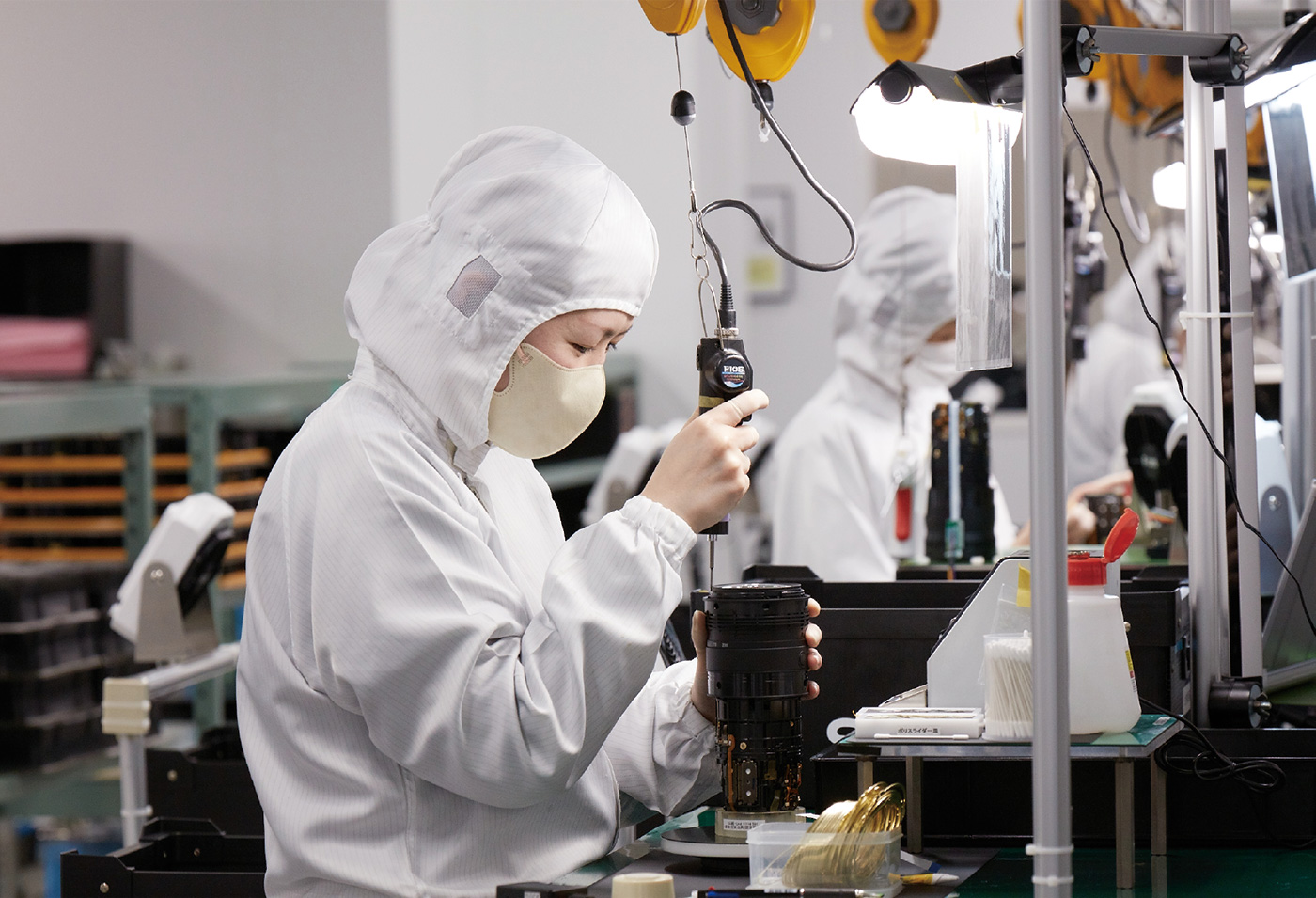
从事生产技术入职第6年的木田悠太郎说,关于SIGMA 的产品制造“有意让人感受到产品是有品位的”。例如,在操作变焦镜头时,为了能感受到高级感,变焦环做成了能丝滑顺畅的转动。戴遮光罩时咔嚓的触感和观察交换镜头时镜筒内部的美观也重视品位。交换镜头在清洁的室内进行组装,以免混入灰尘等。零件数达200~300,每道工序都配备了作业人员,工作的大部分是女性工作者。虽然处理精密的零件,但组装的难度通过设计阶段的努力和治具的设计等提高了作业性,作业人员可以很容易熟练地组装零件。
能支撑这份熟练的是HIOS电动螺丝刀。使用的螺丝的直径是1.4~2mm,长度1.0~10mm,电动螺丝刀能有节奏地拧装小而难操作的螺丝。整个工厂使用了650把电动螺丝刀,全都是HIOS 电动螺丝刀。无碳刷电动螺丝刀采用机型是BL-2000,约占9成。进入公司第10年的组装技术管理科的员工铃木优希评价说:“不仅维护简单性能也很稳定,这与没有偏差的组装品质紧密相关。”
没有碳刷的无刷电机,不会产生废弃的碳粒子。因此也不用每月一次的内部清洁。会津工厂用7年替换成BL-2000,3年前已全部完成。
追求高水准的组装品质
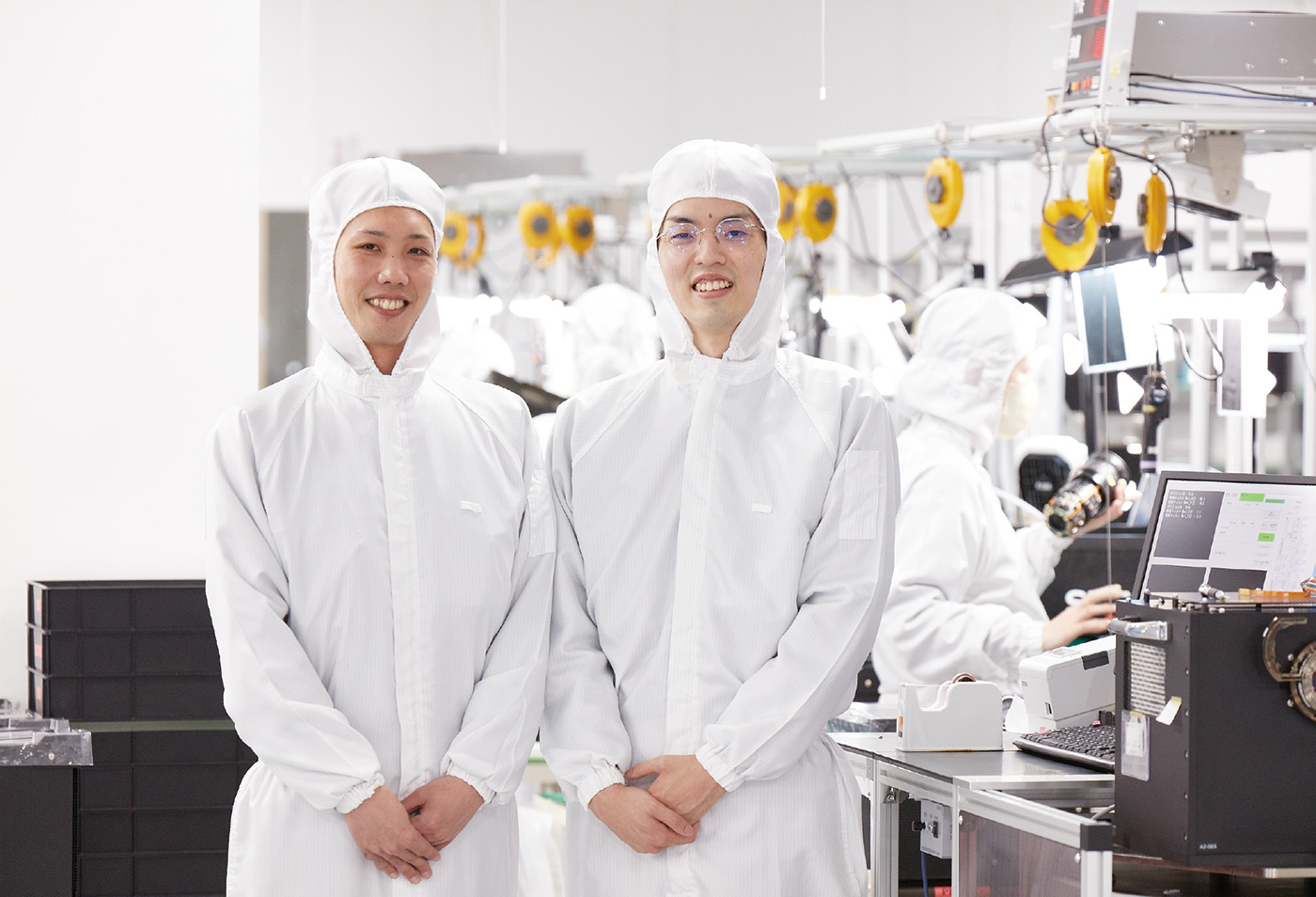
仅254g的电动螺丝刀,其本体轻巧也与组装交换镜头的品质很有关系。可稳定地保持住电动螺丝刀,提高作业精度和效率。减轻了作业负担和疲劳。
本体外形、操作开关的位置也以提升效率和减轻疲劳作为第一开发要素,容易握住,触感也好。更重要的是“没有听说过故障”(铃木),且对 HIOS 电动螺丝刀寄予着深厚的信赖。
致力于国内生产,会津工厂是唯一的生产基地。其竞争力掌握着SIGMA发展的关键,追求高精度的产品制造力是不会止步。为了今后也得到顾客不动摇的信赖,HIOS的产品也继续向更高的水准挑战。(敬称略)