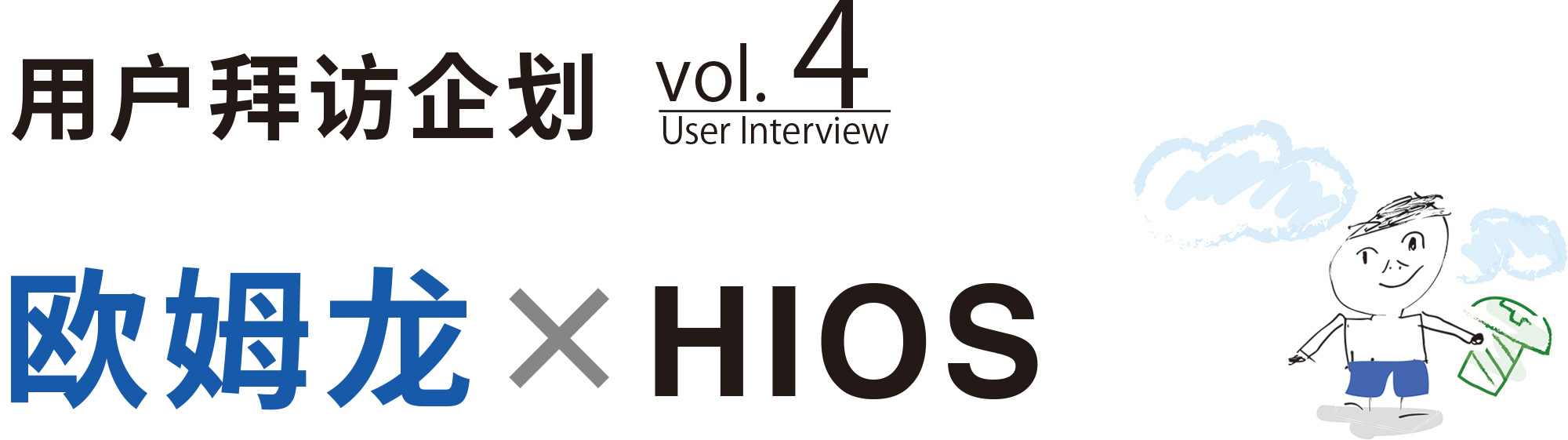
超少量多品种生产挑战下一代产品制造
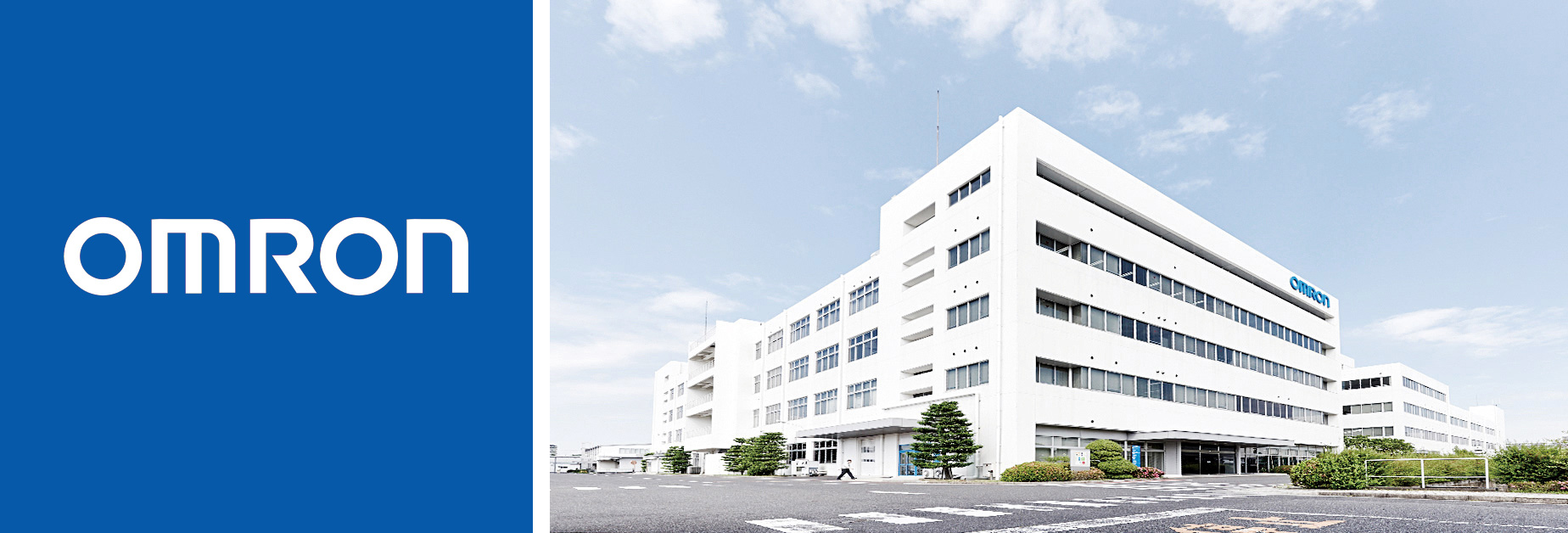
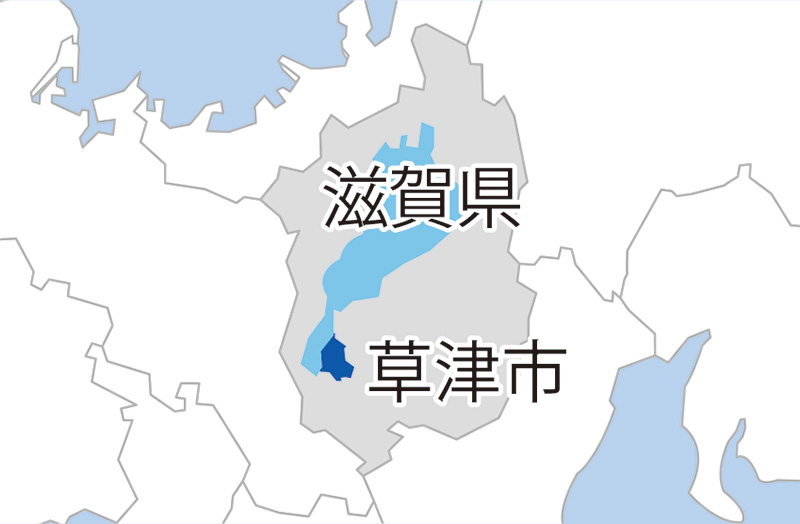
欧姆龙株式会社草津工厂
(滋贺县草津市)
琵琶湖有着大约400万年的历史,是日本最大最古老的淡水湖。滋贺县草津市面向琵琶湖的东南面,作为近畿和中部大城市圈的枢纽不断发展。在少子老龄化日趋严峻的日本,草津市是一座为数不多的现在人口仍在持续增加的城市。当地产品制造的领先企业是欧姆龙FA事业的主力基地草津工厂。该厂传承创业人立石一真先生的理念,不断地提高生产率。
将半自动化和大数据分析作为竞争力之源
欧姆龙草津工厂生产的是掌管PLC、伺服驱动器、图像处理器等FA的“心脏”的控制类设备。借用该公司之言,就是“贴装了基板的高功能产品”。通过先进的自动化和大数据分析对难以高效化的超少量多品种生产进行彻底的改善。采访中能看到该公司的技术力量和现场生产力,以及与独家企业哲学融合的下一代生产线的状况。
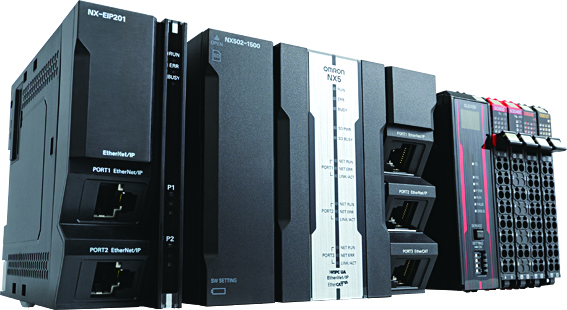
欧姆龙的自动控制器“NX5”。草津工厂生产这种FA类的控制设备
ILOR+S带来的突飞猛进的生产率
欧姆龙草津工厂的特点是超多品种少量生产,即它的多品种少量生产已达到了必须加个“超”字的级别。工厂只有一栋厂房,在1楼贴装基板,在2楼进行装配和检验。也就是说让我们吃惊的是在有限的生产区域要生产4800种产品。生产管理部生产技术课的国本将秀审查主任淡定自若地笑着说“在接单制造利基产品的过程中,不知不觉地就变得这么多了”。该厂房的2楼约50条6m×4m的单元生产线井然有序。并非一直生产4800个品种,因为月产20台以下的品种占85%以上,毫无疑问属于超多品种少量生产。生产线上流动着的产品时不时地变化着,不难想像,要自动化和高效化是多么难。如何才能解决这个问题呢?从结论上来说,其解就在于该公司的事业内容。欧姆龙的FA所需的所有“ILOR+S”※全部都由公司自己制造,从而能够抓住关键有效使用。并凭借资深技术人员的智慧,通过IoT分析找出课题,在适当的部位进行自动化。不是无人化,而是以人机协调为发展方向。这与混流单元生产、与企业哲学“机械能做的事交给机械,人应在更具创造性的领域享受创造性活动带来的快乐”一致。“人擅长的领域交给人去做,机械擅长的反复作业交给机械去做。自动化搞得过分会增加成本,也没什么意义”(国本先生)
※ “Input(输入设备)”、“Logic(控制设备)”、“Output(输出设备)”、“Robot(机器人)”、“Safety(安全相关设备)”的总称
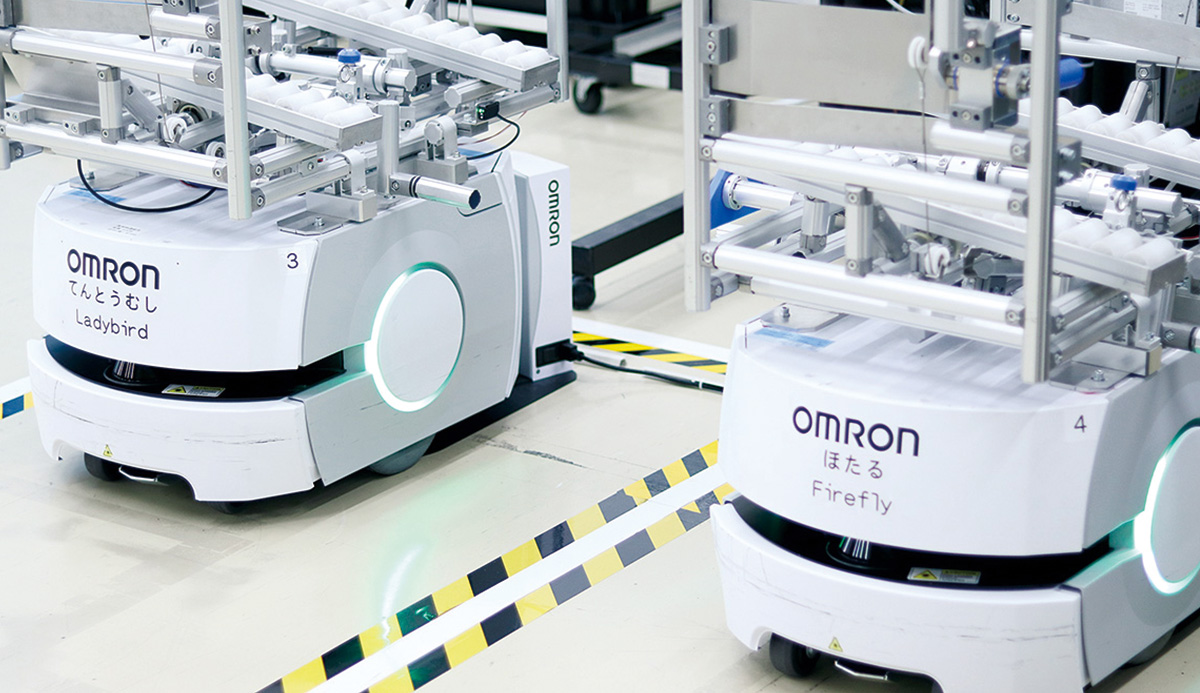
公司自制AMR进行成品搬运和空箱供给
不沉溺于数据的汪洋大海现场推出的系统
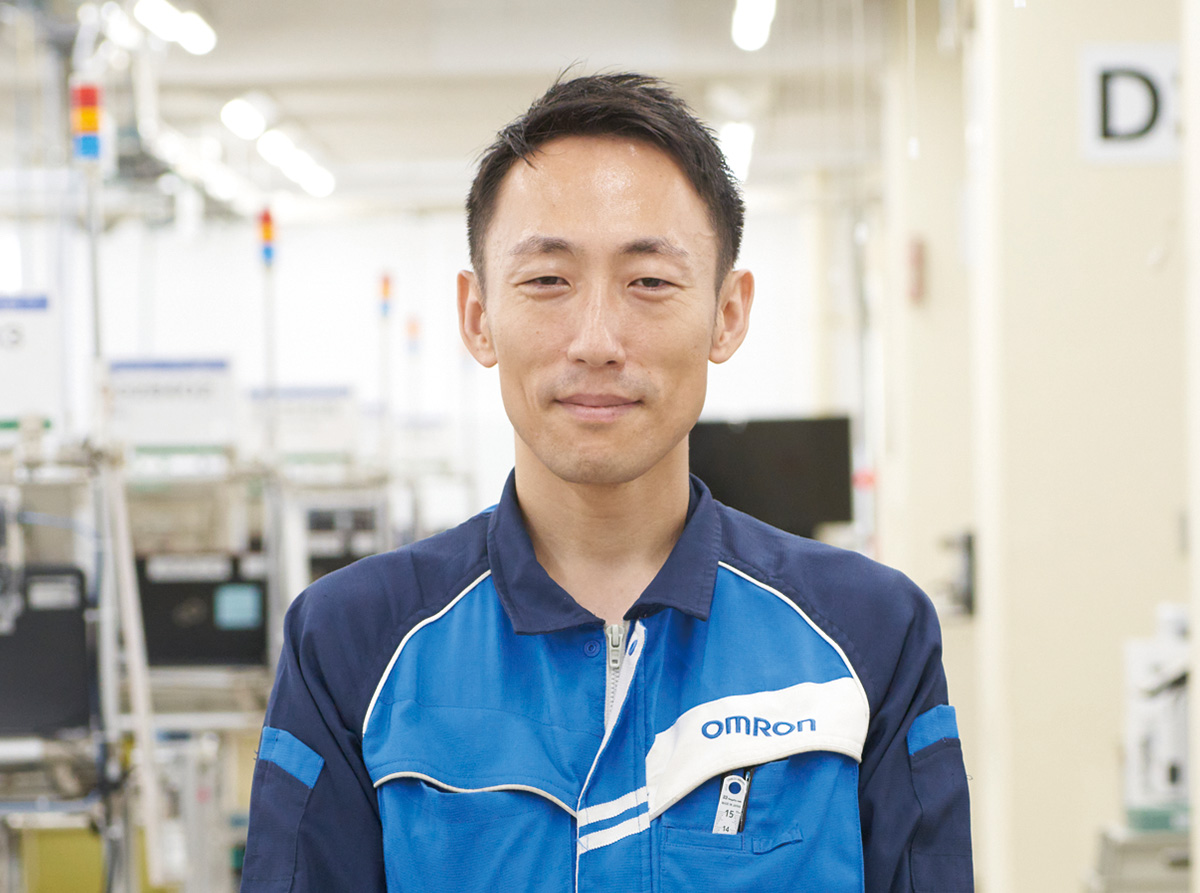
欧姆龙工业自动化
商务公司
生产SCM本部 草津工厂生产管理部
生产技术课审查主任 国本 将秀先生
商务公司
生产SCM本部 草津工厂生产管理部
生产技术课审查主任 国本 将秀先生
草津工厂是超多品种少量生产,正在推进自动化。例如用公司自制AMR将成品搬运自动化。一放上成品后传感器就进行检测的机制与由人巡回相比,负荷减轻了不少。对伺服驱动器的外观检验,置换为公司自制的图像处理器和AI也是一例。靠自动化生产率提高到200%以上,效果提升的主要原因是CLCS。从现场的设备收集数据,制成图表,使生产线内的生产可视化。假如直行率较低,就由此开始改善。由于一眼就能看出问题,与靠感觉进行改善相比,效率绝然不同。在导入生产线,改善循环缩短了3个月。CLCS如此有助于改善活动,但原来的目的是提高质量。对生产进行感测,例如构建这样的机制:需要拧4下的螺丝,没有准确地拧4下的话,下一道工序的设备就无法启动。IoT要一下子获取所有的数据,很容易沉溺于庞大的数据中。但是我们在现场倒过来算所需的数据,以低成本创出高效果。具体就是从各种设备获得NG次数及其内容等数据,手段之一是HIOS的电动螺丝刀“熟练工”。
将防止出错的“熟练工”变成培训新手的工具
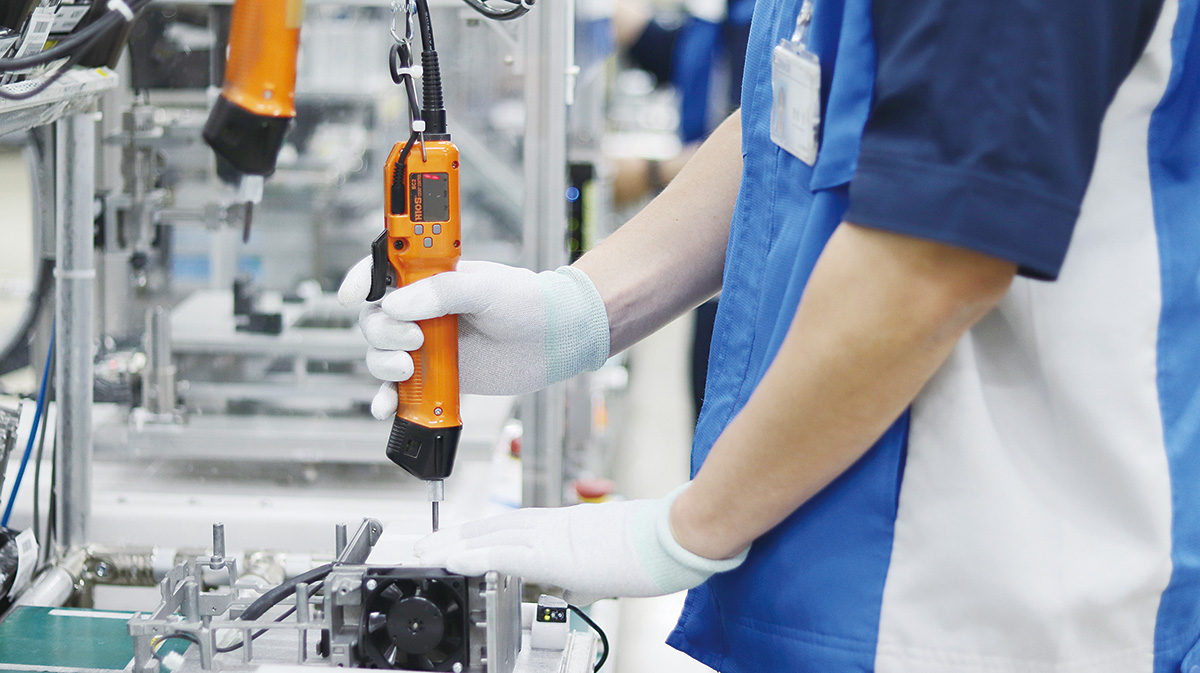
熟练工比我的“工龄”还要长,至少很早以前就使用熟练工了。尤其是在螺丝较多,还需要扭矩管理的伺服驱动器的装配中更是受到器重。谁都能方便地使用,并能担保扭矩或螺丝差错、拧紧次数等质量,这两点是很重要的。由1把螺丝刀进行控制也是一个优点。草津工厂有很多熟练工,放在需要外部设备的地方。草津工厂的螺丝问题中最多的是忘记拧紧。而且各品种的螺丝种类和数量也不同,所以容易发生螺丝种类差错。这由包括熟练工在内的系统防止这一问题。熟练工具有可从外面改变设置的功能,根据生产品种的切换,自动切换拧紧数量设置。导入CLCS后次品明显减少了。新手先上导入CLCS的生产线,熟练后再转到其它生产线,熟练工还承担这种登龙门的作用。熟练工和CLCS给人带来了“即使出错,系统也能防止”的放心感。操作员从培训起就使用熟练工。如果改成其它产品,会发生混乱吧。从好的意义上来说溶入了生产情景中。说到草津工厂的今后方针,首先是去年因缺乏构件让大家待工了。今后将追求生产率和对需求变化的应对力,利用通用性较高的自动化,提高整体效率而不是仅仅一条生产线的效率。我们还提出了基板贴装以ppb(次品率为十亿分之一)为目标。难度非常高,将此作为我们的使命,继续改善生产。
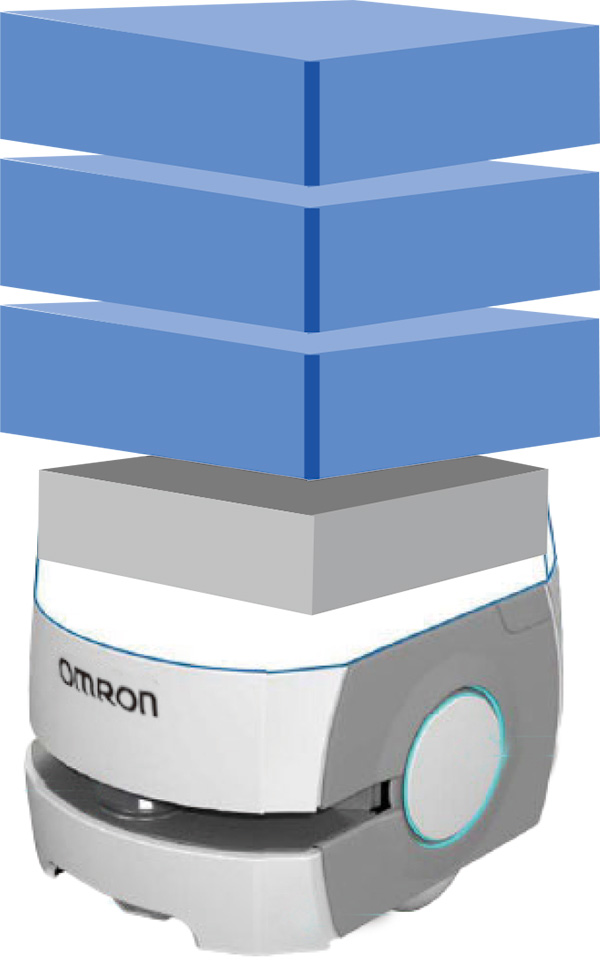
消除次品的关键在于电动螺丝刀

伺服驱动器的装配生产线上HIOS的熟练工螺丝刀排列成行
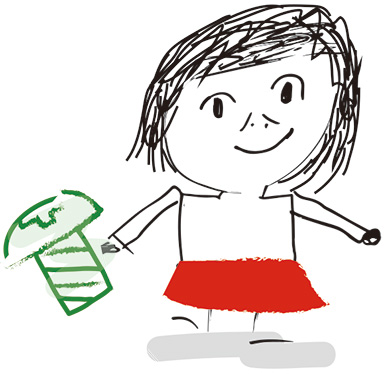
自动化案例:草津工厂对基板贴装导入了协作机器人。贴装元器件时,在金属掩模版上涂上锡膏,每个品种都必须更换和清洗掩模版。这个掩模版就是由协作机器人放入清洗机的。国本先生讲述了导入的背景。“协作机器人虽然没有栏栅,但动作缓慢,如果要追求生产率,那还是人工更快。但是如果工业机器人设置后不启用,生产线就失去了灵活性。为了留下切换人和机器人这一选项,选择了协作机器人”。另外,该工厂还进行使用公司自制的AMR的成品搬运、同样使用公司自制的图像处理器的外观检验等多方位自动化。靠一系列的“半自动化”,单元生产线的生产率被戏剧性地提高到200%以上。该工厂的生产改善如此扎实很大部分是通过 “CLCS(单元生产线控制系统)”。生产线内的生产可视化,例如将直行率、循环时间等制表,从而找出问题,有的放矢地进行改善。CLCS对提高质量也很有效。实际上该公司在13条装配生产线构建了“只有上一道工序OK了才能物理上启动下一道生产线”的机制。这里掌握着关键的是HIOS的电动螺丝刀“熟练工”,对忘记拧紧螺丝、长度不对等各种问题进行检测,防患于未然。螺丝刀输出的操作数据有助于CLCS的大数据分析,从而既有助于防止出次品又有助于提高生产率。草津工厂努力通过一系列的措施变得更强,基板贴装以“ppb等级”的次品率为目标。这意味着“次品率为十亿分之一”。毫无疑问是业界顶级水准的目标。难度非同一般,国本先生述说了它的意义所在“如果我们达到了ppb,就能向客户提供知识和见识”。草津工厂的发展无止境。