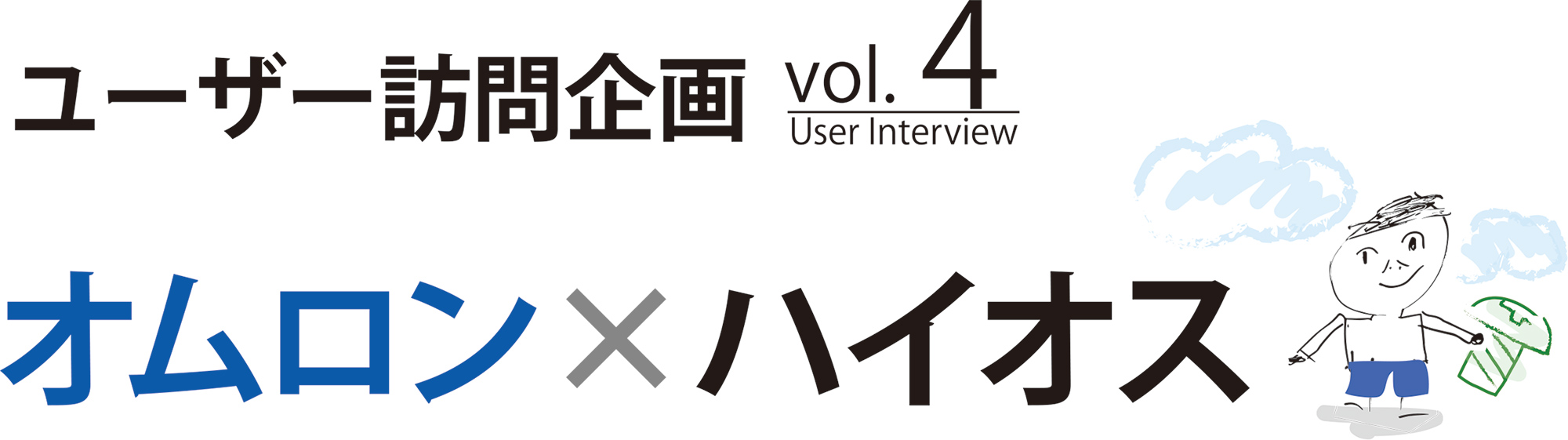
超少量多品種生産が挑む
次世代型モノづくり
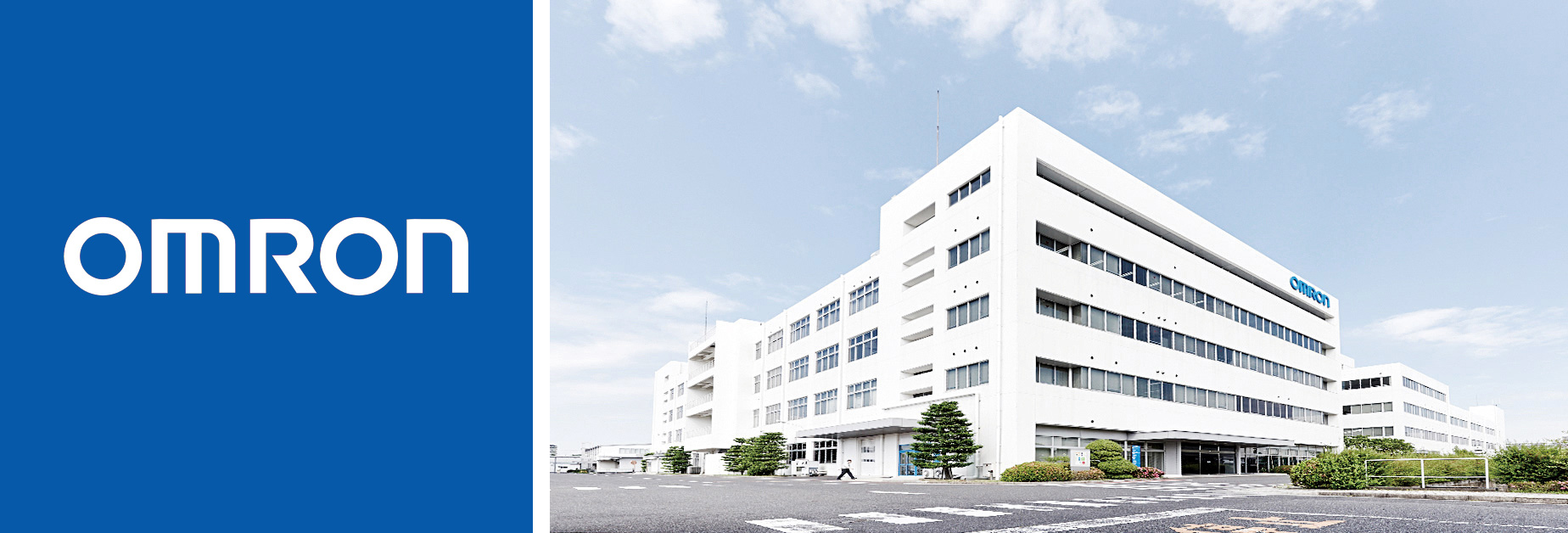
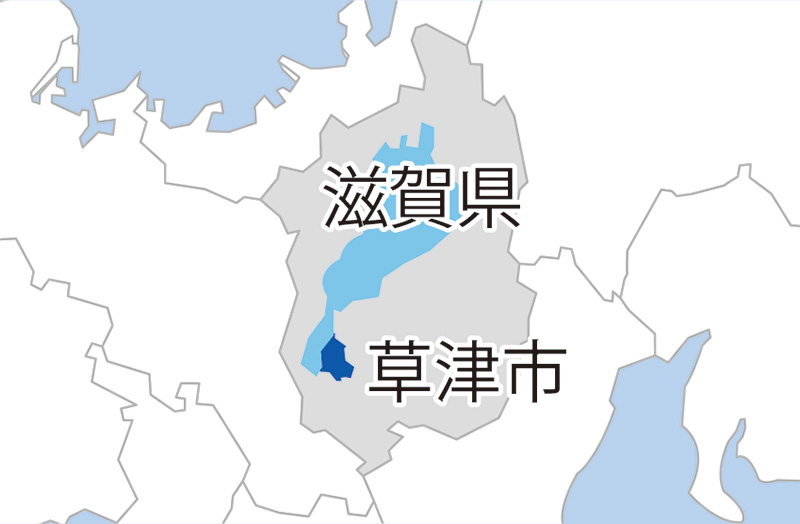
オムロン株式会社草津工場
(滋賀県草津市)
およそ400万年の歴史をもつとされる日本最大・最古の淡水湖、琵琶湖。その南東部に面し、近畿と中部の大都市圏の結節点として発展を続けるのが滋賀県草津市だ。少子高齢化の進む日本において今なお人口増加の続く数少ない都市でもある。そしてこの地でモノづくりの先端を走るのが、オムロン・FA事業の主力拠点である草津工場。創業者・立石一真氏の理念を受け継ぎつつ、終わりなき生産性向上に邁進する。
半自動化とビッグデータ解析が競争力の源に
オムロン・草津工場が生産するのはPLCやサーボドライバ、画像処理装置などFAの“心臓部”を司るコントローラ系の機器だ。同社の言葉を借りるなら「基板を実装した高機能製品」ということになる。効率化の難しい超少量多品種生産ながら、先進的な自動化やビッグデータ解析による徹底した生産改善を推し進める。取材で見えてきたのは同社の技術と現場力、そして独自の企業哲学とが融合した次世代の生産ラインの姿だった。
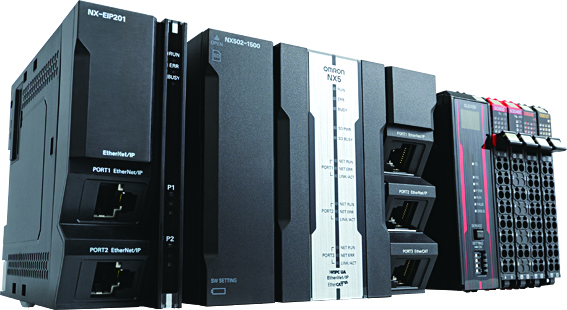
オムロンのオートメーションコントローラ「NX5」。
草津工場はこうしたFA系の制御機器を生産する。
草津工場はこうしたFA系の制御機器を生産する。
ILOR+Sが導く劇的生産性
オムロン・草津工場の特徴は「超」が付くレベルの多品種少量生産だ。工場は1棟のみで、1階で基板を実装し、2階で組立と検査を行う。つまり生産エリアは限られているのだが、そこで4800品目もの生産を担うというから驚いてしまう。「ニッチな製造を引き受けるうちに、いつの間にかこうなりました」。生産管理部生産技術課の国本将秀主査はそう説明し、事もなげに笑った。同工場の2階には6m×4mのセルラインが約50も並んでいた。常に4800品目を生産するわけではないが、月産20台以下の品目が85%以上を占めるため超多品種少量生産であるのは間違いないだろう。ラインに流れる品目は刻々と変わり、自動化や効率化の難しさは想像にかたくない。この壁をいかにして破るのだろうか。結論から言えば、その解は同社の事業内容にあった。オムロンはFAに必要な「ILOR+S」※をすべて自社製造し、勘所を押さえ効果的に活用できる。さらに熟練技術者の知見やIoTによる分析で課題を見極め、適所に絞った自動化を推進。無人化でなく人と機械の協調を志向した。これなら混流セル生産にも、企業哲学「機械にできることは機械に任せ、人間はより創造的な分野で活動を楽しむべき」にも合致する。「人の得意な領域は積極的に人に任せ、機械が得意な反復作業は機械に任せます。むやみな自動化はコスト増加につながりあまり意味もありません」(国本氏)
※「Input(入力機器)」「Logic(制御機器)」「Output(出力機器)」「Robot(ロボット)」「Safety(安全関連機器)」の総称
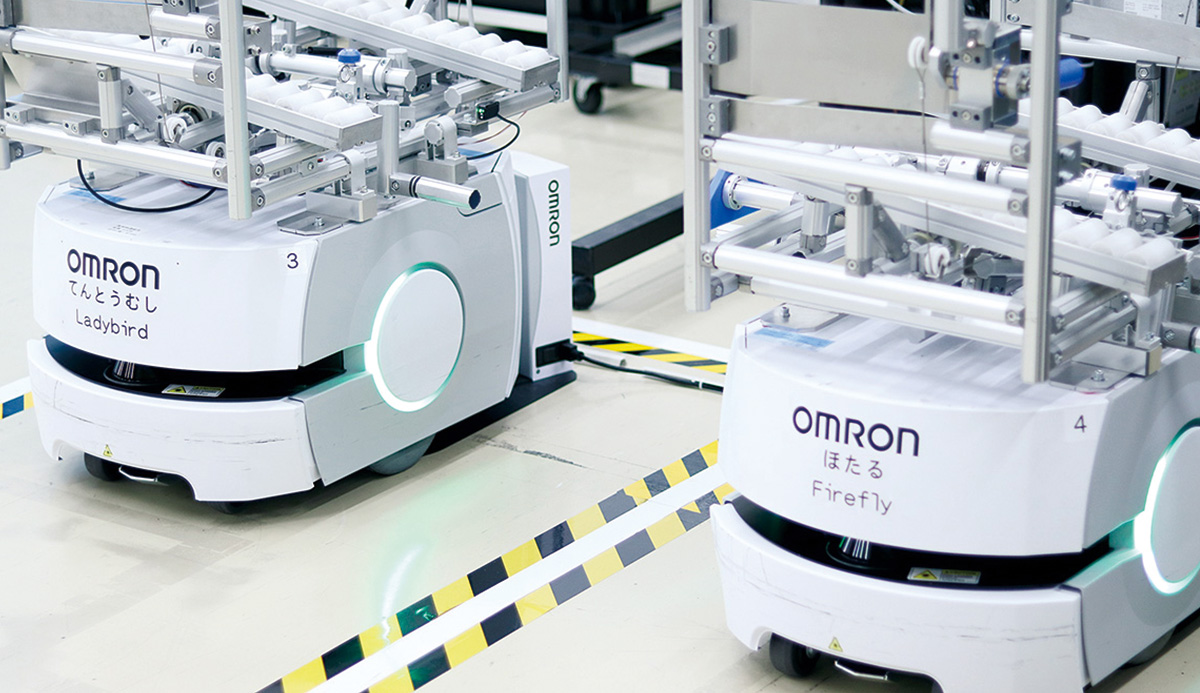
自社製AMRが完成品搬送と空箱供給を行う
データの海に溺れない現場発のシステム
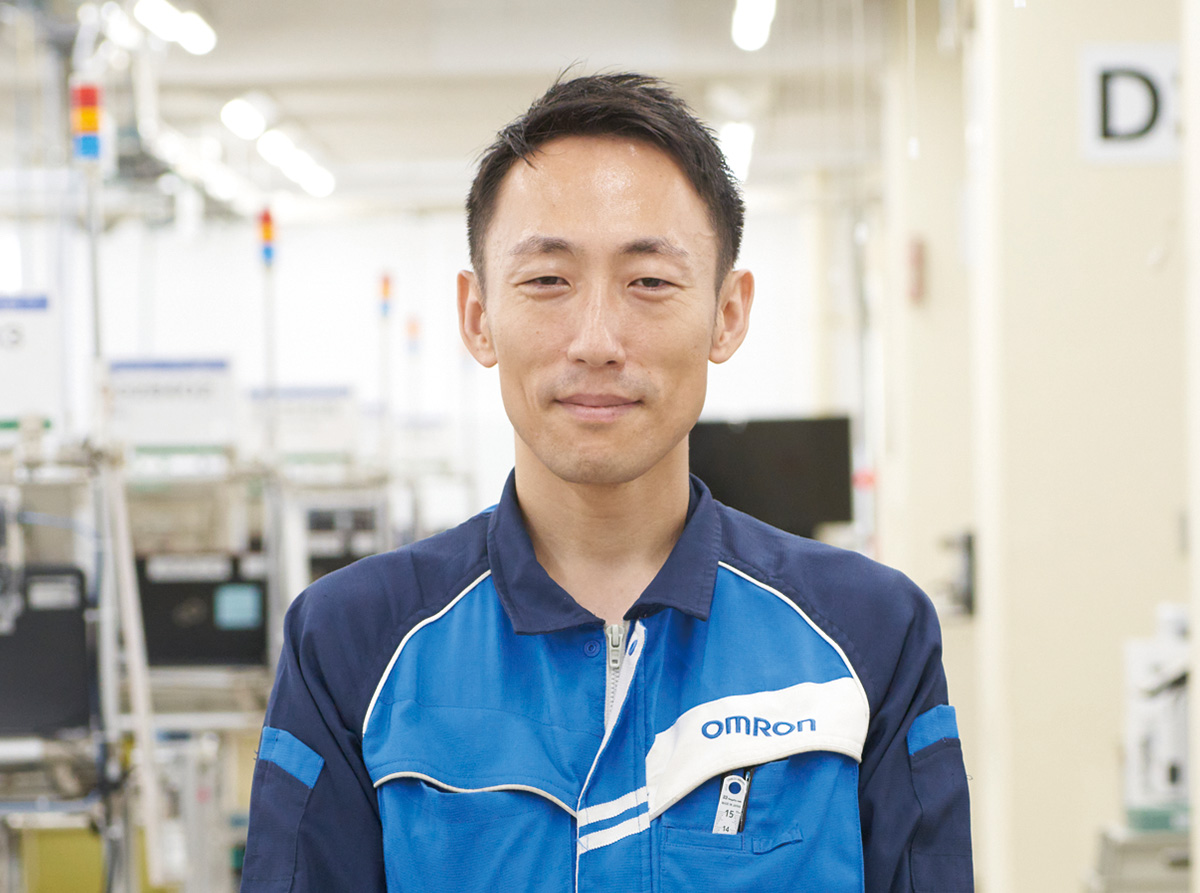
オムロンインダストリアル
オートメーションビジネスカンパニー
生産SCM本部 草津工場生産管理部
生産技術課主査 国本 将秀氏
オートメーションビジネスカンパニー
生産SCM本部 草津工場生産管理部
生産技術課主査 国本 将秀氏
草津工場は超多品種少量生産ですが、自動化を推進しています。例えば自社製AMRで完成品搬送を自動化しました。完成品を置くとセンサが検知する仕組みで、人の巡回と比べ相当の負荷低減です。サーボドライバの外観検査を自社の画像処理装置とAIに置き換えた例もあります。自動化で生産性は200%以上に高まりましたが、効果が上がる要因はCLCS。現場の機器からデータを吸い上げて図表にし、ライン内の生産を可視化するものです。仮に直行率が低いならそこから改善に着手します。課題が一目でわかるため感覚に頼る改善と比べ効率が段違い。導入ラインでは改善サイクルが3カ月縮まりました。このように改善活動に役立つCLCSですが、元々の狙いは品質向上でした。生産をセンシングし、例えば4回のねじ締めが必要なら4回正しくねじを締めないと次工程の設備が動かない仕組みを構築したわけです。IoTでは一挙にあらゆるデータを取ろうとして膨大なデータに溺れがち。しかし我々は必要なデータを現場で逆算し、低コストで高い効果を出せています。具体的にはNG回数やその内容などを様々な機器から取得するわけですが、手段の1つがハイオスの電動ドライバー「熟練工」です。
ミスを防ぐ「熟練工」が新人の教育ツールに
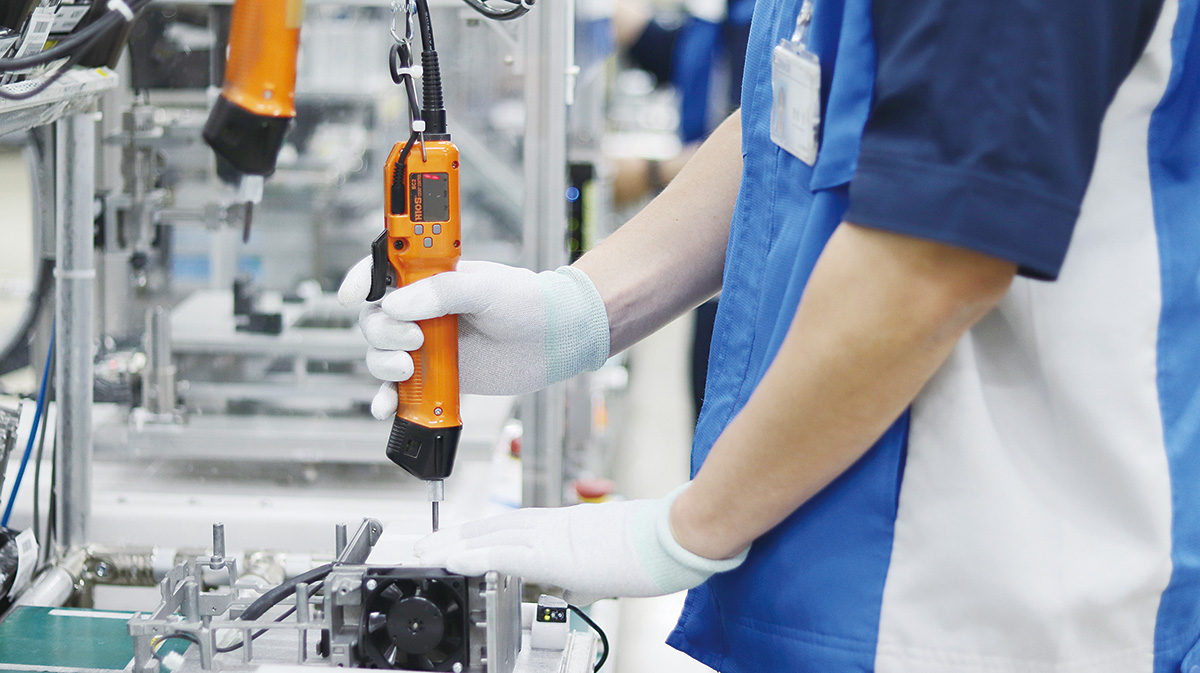
私より熟練工の方が「社歴」が長いのですが、少なくともかなり昔から熟練工を使っていました。特にねじが多くトルク管理も必要なサーボドライバの組立で重宝します。誰でも簡単に使える点とトルクやねじ間違い、締付回数などの品質が担保できる点が大きい。制御がドライバー1本で完結するのもメリットです。草津工場は熟練工の本数も多く外部機器が必要だと場所を取ります。草津工場のねじトラブルで最も多いのは締め忘れです。また品目ごとにねじの種類も本数も変わるため、ねじの種類間違いも起こりえます。これを熟練工を含むシステムが防いでいます。熟練工は外部から設定を変える機能があり、生産品目の切り替わりに応じて締付本数設定を自動で切り替えます。CLCSの導入で不良は目に見えて減りました。また新人はまずCLCSの導入ラインに入り、習熟後に他のラインに移るという登竜門の役割も担っています。熟練工やCLCSが「ミスをしてもシステムで防げる」という安心感を醸成してくれています。作業者は訓練のときから熟練工を使います。他の製品に変えると混乱するでしょうね。良い意味で生産風景に溶け込んでいます。草津工場の今後の方針についてお話ししますと、まず昨年は部材不足で皆様をお待たせしました。今後は生産性と需要変動への対応力を突き詰め、汎用性の高い自動化で1つのラインにとどまらない全体効率を追求します。また基板実装ではppb(不良率10億分の1)を目標に掲げています。難易度は非常に高いものの、我々のミッションとして引き続き生産改善に取り組みます。
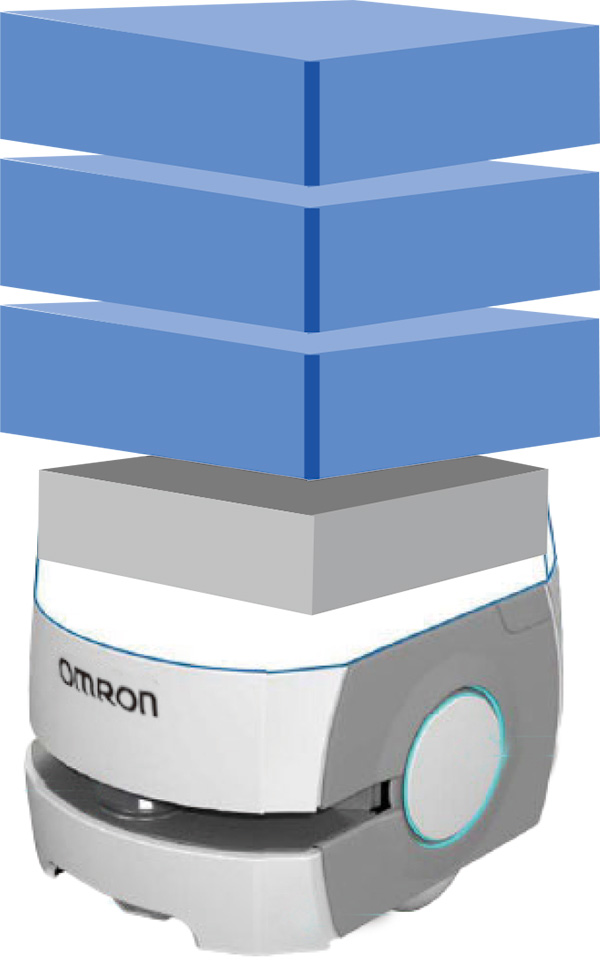
不良撲滅の鍵は電動ドライバー

サーボドライバの組立ラインにハイオスの熟練工ドライバーが並ぶ
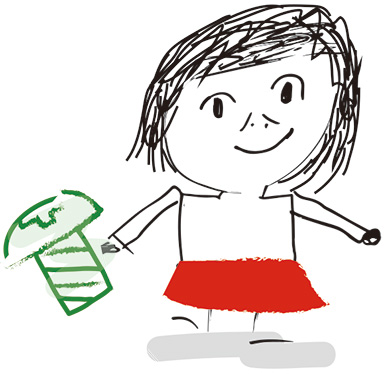
自動化の例として草津工場は基板実装に協働ロボットを導入した。部品を実装する際に金属マスクの上から半田ペーストを塗るが、品目ごとにマスクの交換と洗浄を行わねばならない。このマスクを協働ロボットが洗浄機へ投入するのだ。国本氏は導入背景をこう語る。「協働ロボットは柵がないぶん動きが遅く、生産性を求めるなら人の方が早い。しかし産業用ロボットは設置後に動かせずラインの柔軟性が失われる。人とロボットの切替という選択肢を残すため協働ロボットを選びました」。同工場は他にも自社製のAMRを活用した完成品搬送や、同じく自社の画像処理装置を使った外観検査など多角的な自動化を進める。一連の「半自動化」でセルラインの生産性は200%以上に劇的に高まったという。同工場の生産改善がこうも的確なのは「CLCS(セルラインコントロールシステム)」による部分が大きい。ライン内の生産を可視化するもので、例えば直行率やサイクルタイムなどを表に集約。これで課題をあぶり出し、的を得た改善を実行している。CLCSは品質向上にも有効だ。実際に同社は組立の13ラインで「前工程がOKでないと物理的に次のラインが起動しない」仕組みを構築。ここで鍵を握るのがハイオスの電動ドライバー「熟練工」で、ネジの締め忘れや長さ違いなど様々な不良を検知して未然に防ぐ。ドライバーから出力された作業データはCLCSのビッグデータ解析に役立てられる。不良の防止と生産性向上の両面に貢献しているわけだ。草津工場では一連の施策をより強化し、基板実装で「ppbレベル」の不良率を目指す。これは“不良率10億分の1”を意味。間違いなく業界トップ水準の目標だ。並の難度ではないが国本氏は「我々がppbを実現すればお客様に知見を提供できる」と意義を語る。草津工場の進化に終わりはない。