
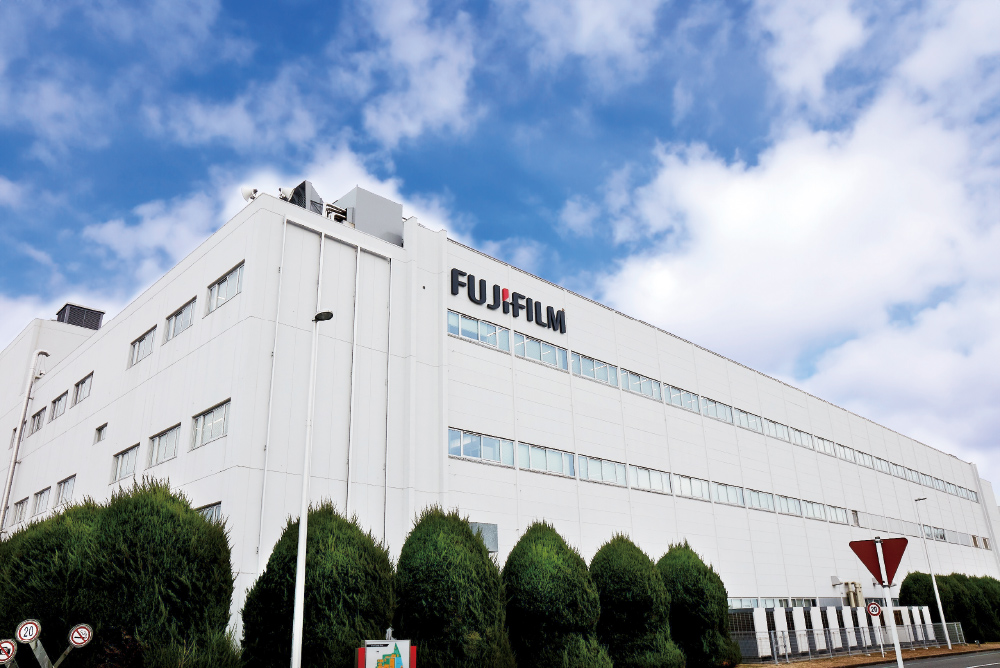
Ebina Plan, FUJIFILM Manufacturing
FUJIFILM Business Innovation Corp. is a leading manufacturer of multifunction printers and other types of printers. It owns FUJIFILM MFG as its production division and Ebina Plant is one of four domestic facilities. Ebina Plant assembles final products for commercial printers. The plant has realized a highly advanced production system through actively implementing production innovation activities based on IPW. They have standardized their long-held know-how and use it in their production platform. Especially, unlike general printers in offices, large products for commercial printing produced by Ebina Plant are production goods directly impacting customers' businesses, and therefore, they are promoting highly advanced manufacturing under strict quality control.
Ebina Plant, FUJIFILM MANUFACTURING Corp.
Shareholder: 100% owned by Fujifilm Business Innovation Corp.
Address: 2274 Hongo, Ebina City, Kanagawa Prefecture
Business: Final assembly of high-speed printers for the commercial printing market (Ebina Plant)
Address: 2274 Hongo, Ebina City, Kanagawa Prefecture
Business: Final assembly of high-speed printers for the commercial printing market (Ebina Plant)
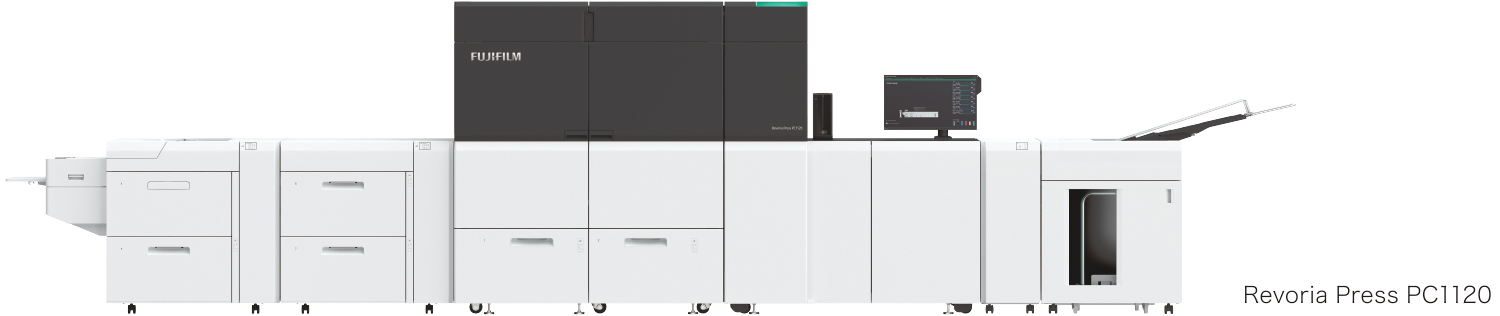
More than 100,000 screws are fastened per day. For Ebina Plant, FUJIFILM MANUFACTURING, which produces high-speed and high-performance printers for commercial printing, screw fastening is crucially important for every one of its manufacturing processes. Since a single missing or loose screw can lead to product defects, a strict control system for fastening is essential. While implementing production innovative activities based on FUJIFILM’s IPW (Innovative Production Way), the Ebina Plant decided to introduce HIOS’s digital screwdrivers, JUKUREN BLG-BC2, with a built-in screw counter pulse system to facilitate further quality improvement and high efficiency.
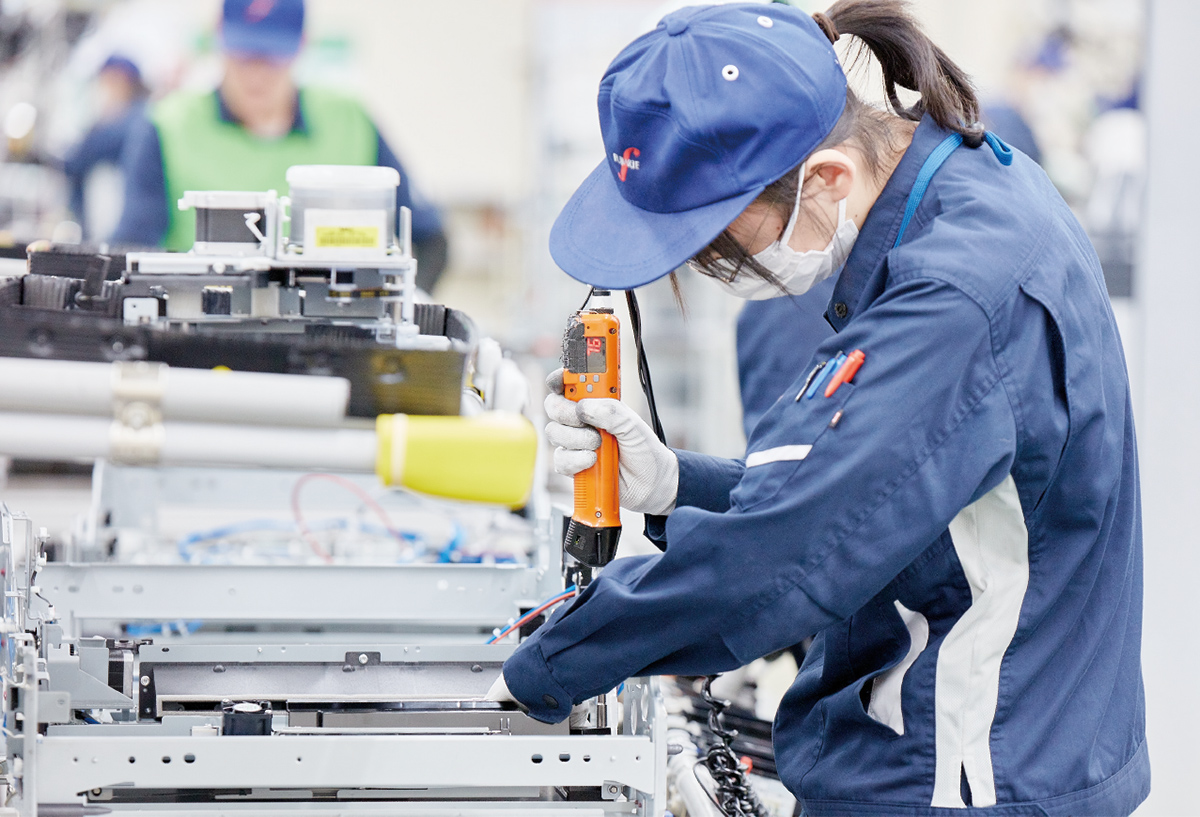
Monozukuri without defects while reducing operators' workload
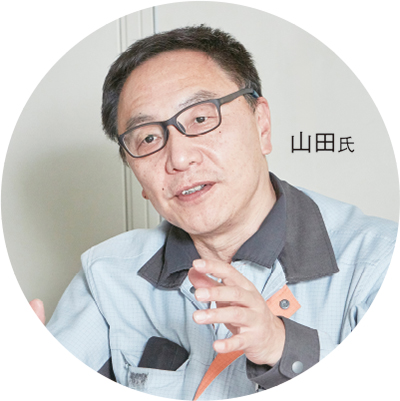
The Ebina Plant's production system is what is called "one-by-one production". In this system, parts of various types or for destinations flow on a single line. After an operator completes assembly in his/her process, he/she sends the parts to the next process on a one-by-one basis. A product starts out as a skeleton, and while it is moving down the line, parts or modules from the sub-lines are installed, and finally it is made into a finished product. Operators assigned to each process assemble in a lean and efficient manner. About the essence of this well-organized manner, Toshihiro Furuta, Manufacturing Manager, describes, "For us, ‘safety and quality’ matter most. While implementing various activities including work standardization and prevention of missing parts or wrong items, we place top priority on ensuring safety and reducing the workload of operators. Thus, our method will not only improve quality, but also lead to higher productivity." In other words, they aim to achieve unique Monozukuri (manufacturing) without defects while reducing the workload of operators.
In the Ebina Plant's production innovation activities based on IPW, screw fastening is one of the most important targets for improvement. This is because "a lot of time is spent on screw fastening," says Mr. Furuta, Manufacturing Manager. In the past, the use of electric screwdrivers became inevitable, because some operators suffered from tendonitis due to the hundreds of repetitive screw-fastening actions, and there were many female operators. Then, about three years ago, they decided on our JUKUREN, which weighed only 425 grams, significantly lighter than other manufacturers’ screwdrivers. They were fascinated by the JUKUREN’s slender and space-saving grip with a diameter ergonomically calculated to fit easily in a woman's hand.
In the Ebina Plant's production innovation activities based on IPW, screw fastening is one of the most important targets for improvement. This is because "a lot of time is spent on screw fastening," says Mr. Furuta, Manufacturing Manager. In the past, the use of electric screwdrivers became inevitable, because some operators suffered from tendonitis due to the hundreds of repetitive screw-fastening actions, and there were many female operators. Then, about three years ago, they decided on our JUKUREN, which weighed only 425 grams, significantly lighter than other manufacturers’ screwdrivers. They were fascinated by the JUKUREN’s slender and space-saving grip with a diameter ergonomically calculated to fit easily in a woman's hand.
Realized precise screw counting without relying on humans
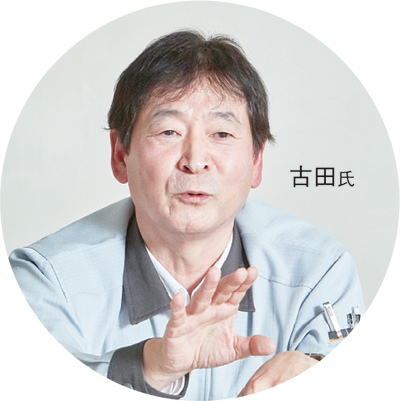
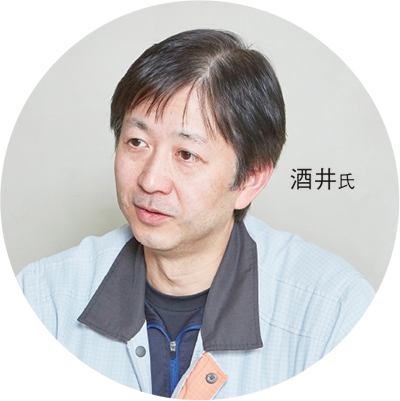
The customer decided on JUKUREN because of the following features: screw counter that accurately counts number of fastened screws, pass/fail judgment that detects fastening errors with high accuracy, and the new function that allows external output of fastening data. Mr. Yoshihiko Yamada, who supervises the Manufacturing Engineering Group, confided, "To tell the truth, there used to be people who counted the number of screws required for each process and then distributed them to each line. In other words, the screw number control was done through an inefficient scheme relying on manpower." Then, the introduction of JUKUREN made it possible for them to input the number of screws required for each model. He explained, "that reduced the man-hours required for screw control and guaranteed the precise screw-fastening result without relying on humans. We also achieved quality improvement through detection of defects, such as floating or skewed screws."
JUKUREN can reduce the workload of operators and ensure stable screw-fastening quality. For example, consider losses caused by poor screw-fastening quality. What needs to be discarded should include not only screws but also damaged components, and even a finished product may be wasted. From another perspective, JUKUREN is a tool that can contribute to an environmentally friendly society. JUKUREN has the advantages of energy saving and no carbon emissions due to the brushless motor. Thus, HIOS’s screw fastening system with the "digital screwdrivers" in focus won the 2022 Encouragement Award at the “EcoPro Awards”, which recognizes products and services that incorporate excellent environmental considerations.
“By the way, the setting of JUKUREN can be changed from the outside. That is also an important feature," said Mr. Katsutoshi Saka, Manufacturing Engineering Group, who is involved in selecting jigs and instruments for improvement of production lines. Such an abundant lineup of accessories to support JUKUREN is another attraction. So, it provides the functions useful for production innovations. Specifically, it can save up to four patterns of screw fastening data including the number of screws to be fastened and the number of rotation pulses, and it can switch the pattern from outside by using BLG-IF2 (available as an optional accessary). Especially on the process lines at Ebina Plant, where models requiring different numbers of screws and rotational pulses for different destinations are handled, "JUKUREN is very helpful for reduction of the workload of operators and line managers because you don’t have to switch the settings on the screwdrivers, but it can be done from outside,” said Mr. Sakai. Consequently, JUKUREN has brought about drastic innovation of the manufacturing site.
JUKUREN can reduce the workload of operators and ensure stable screw-fastening quality. For example, consider losses caused by poor screw-fastening quality. What needs to be discarded should include not only screws but also damaged components, and even a finished product may be wasted. From another perspective, JUKUREN is a tool that can contribute to an environmentally friendly society. JUKUREN has the advantages of energy saving and no carbon emissions due to the brushless motor. Thus, HIOS’s screw fastening system with the "digital screwdrivers" in focus won the 2022 Encouragement Award at the “EcoPro Awards”, which recognizes products and services that incorporate excellent environmental considerations.
“By the way, the setting of JUKUREN can be changed from the outside. That is also an important feature," said Mr. Katsutoshi Saka, Manufacturing Engineering Group, who is involved in selecting jigs and instruments for improvement of production lines. Such an abundant lineup of accessories to support JUKUREN is another attraction. So, it provides the functions useful for production innovations. Specifically, it can save up to four patterns of screw fastening data including the number of screws to be fastened and the number of rotation pulses, and it can switch the pattern from outside by using BLG-IF2 (available as an optional accessary). Especially on the process lines at Ebina Plant, where models requiring different numbers of screws and rotational pulses for different destinations are handled, "JUKUREN is very helpful for reduction of the workload of operators and line managers because you don’t have to switch the settings on the screwdrivers, but it can be done from outside,” said Mr. Sakai. Consequently, JUKUREN has brought about drastic innovation of the manufacturing site.
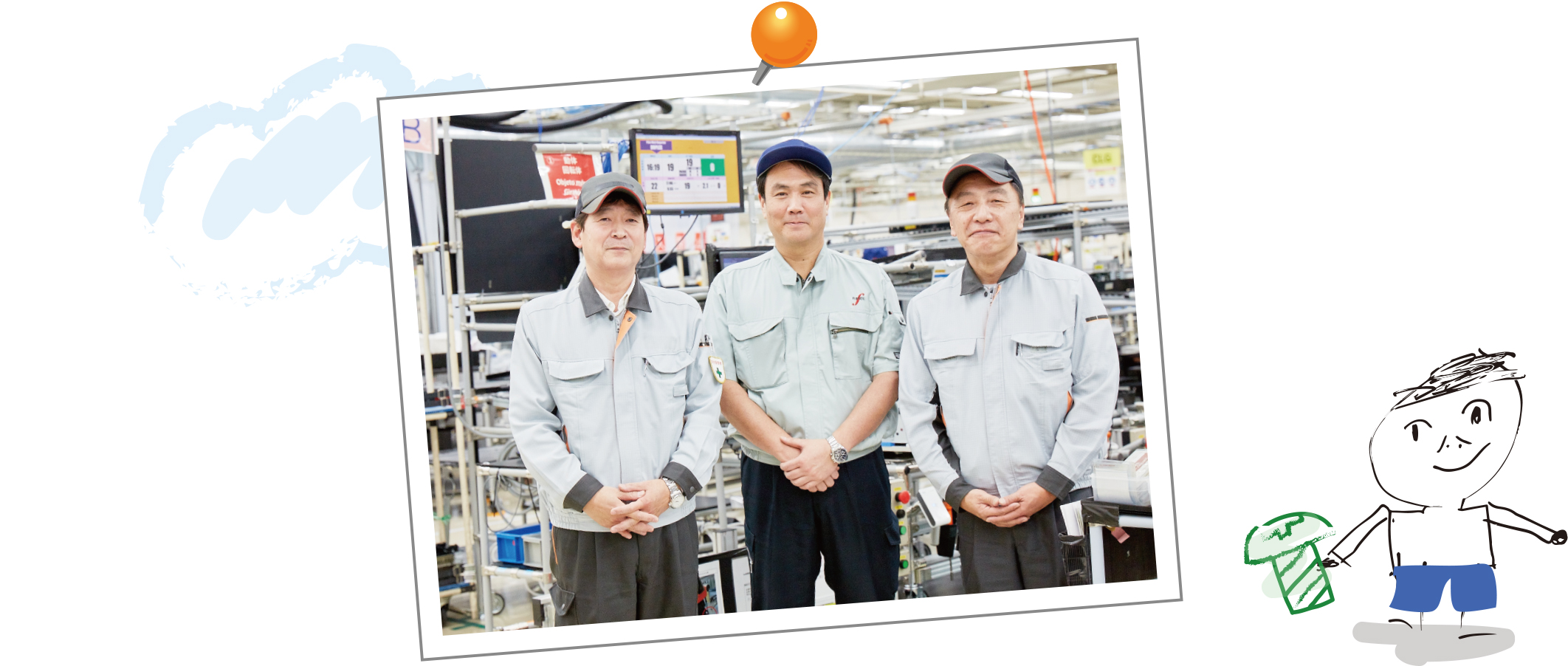
Towards further production innovation through cooperation between HIOS and FUJIFILM MANUFACTURING
Currently, a total of 230 JUKUREN screwdrivers are in operation at the Ebina Plant. Almost all screw fastenings are performed by JUKUREN. The use of brushless motors has "extended the service life and reduced the frequency of breakdowns," and the lightweight and compact design has prevented tendonitis caused by screw-fastening. Furthermore, since the screwdriver itself judges whether a screw has been fastened correctly, an operator can naturally learn the correct fastening process “without being conscious of it," which "makes it easier to train new employees," according to Mr. Furuta. On the other hand, HIOS's customer support is also noteworthy. For example, to avoid the risk of the power cord of a screwdriver getting caught in the legs when an operator is fastening screws while moving around the shop floor, HIOS offers a custom-made lightweight curled cord, demonstrating HIOS’s flexible customer response. The demand level is so high at the Ebina Plant, where innovative production activities based on IPW are being seriously pursued. The plant seeks such a high level because "our products are production goods that support our customers' businesses, and any quality problem will directly affect their production activities" (Mr. Furuta).
Ebina Plant aims further quality improvement. HIOS is striving to meet the diverse needs of individual companies. This way, it is likely that both companies will continue to work together to engage in further production innovation initiatives.
Ebina Plant aims further quality improvement. HIOS is striving to meet the diverse needs of individual companies. This way, it is likely that both companies will continue to work together to engage in further production innovation initiatives.
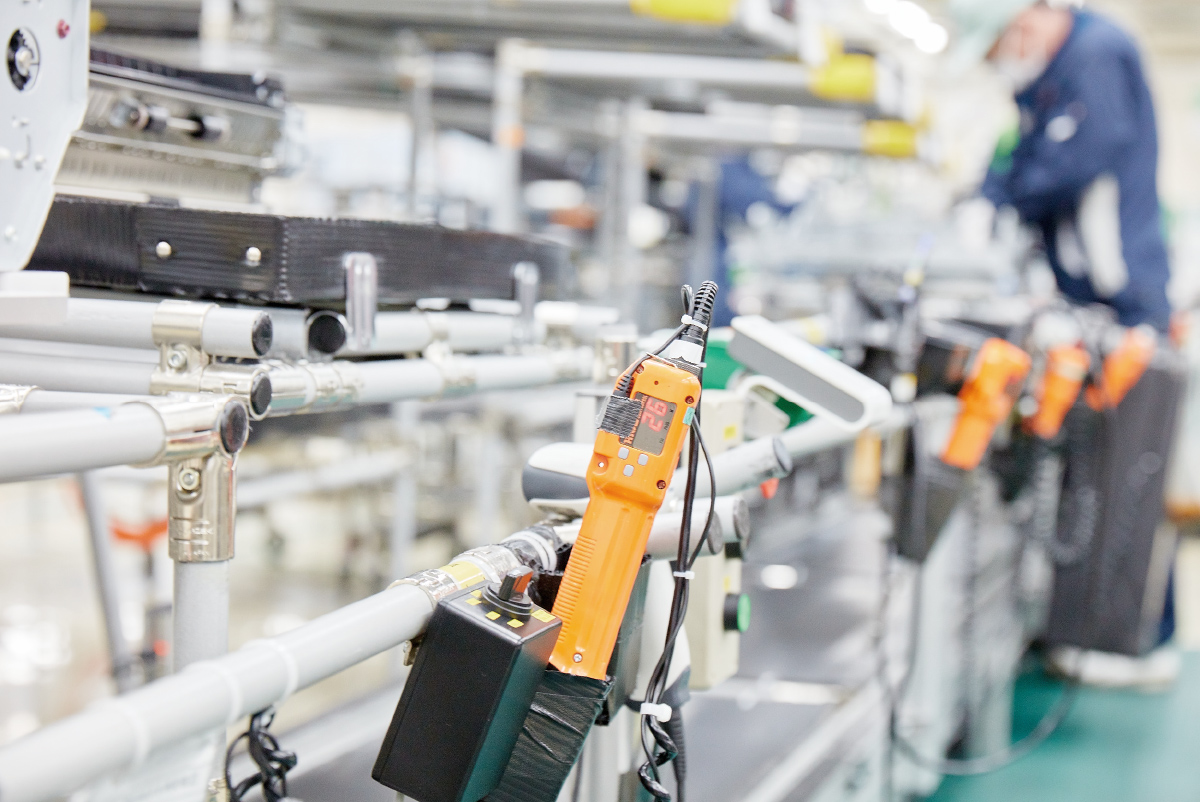
